Product
Your trusted supplier of customized metal products
Customized supplier of high quality metal
Looking for high-quality metals? Explore our extraordinary range of metal products from renowned suppliers and manufacturers. From being content with fewer products to embracing unparalleled reliability. Enhance your efforts with our top metals. Contact us today to redefine quality!
Provide revolutionary custom metal parts for your industry
Metal parts play a vital role in modern industry, especially in industries that require high strength, durability, and precision, such as automotive, electronics, and mechanical manufacturing. Prime is committed to providing a wide range of metal products, including stampings, CNC machining parts, castings, screws, plastic parts, etc. , all products are in line with international quality standards to ensure that the needs of customers around the world.
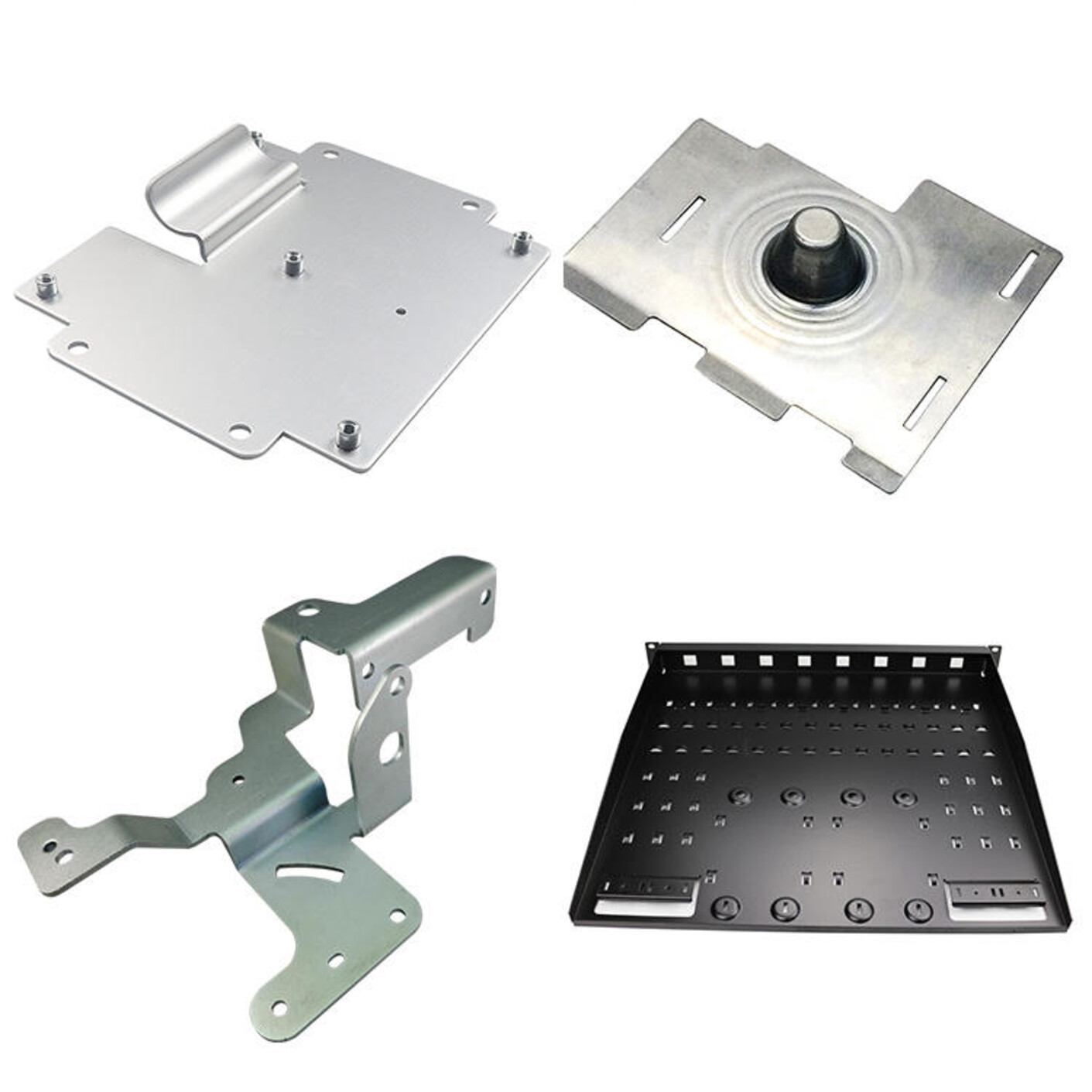
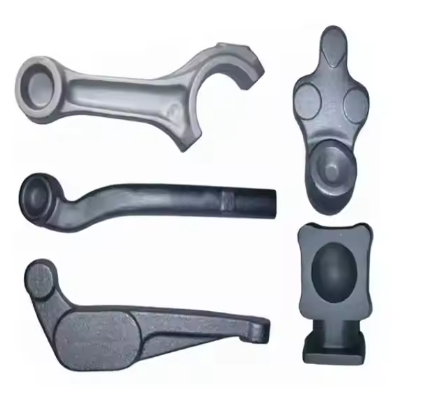
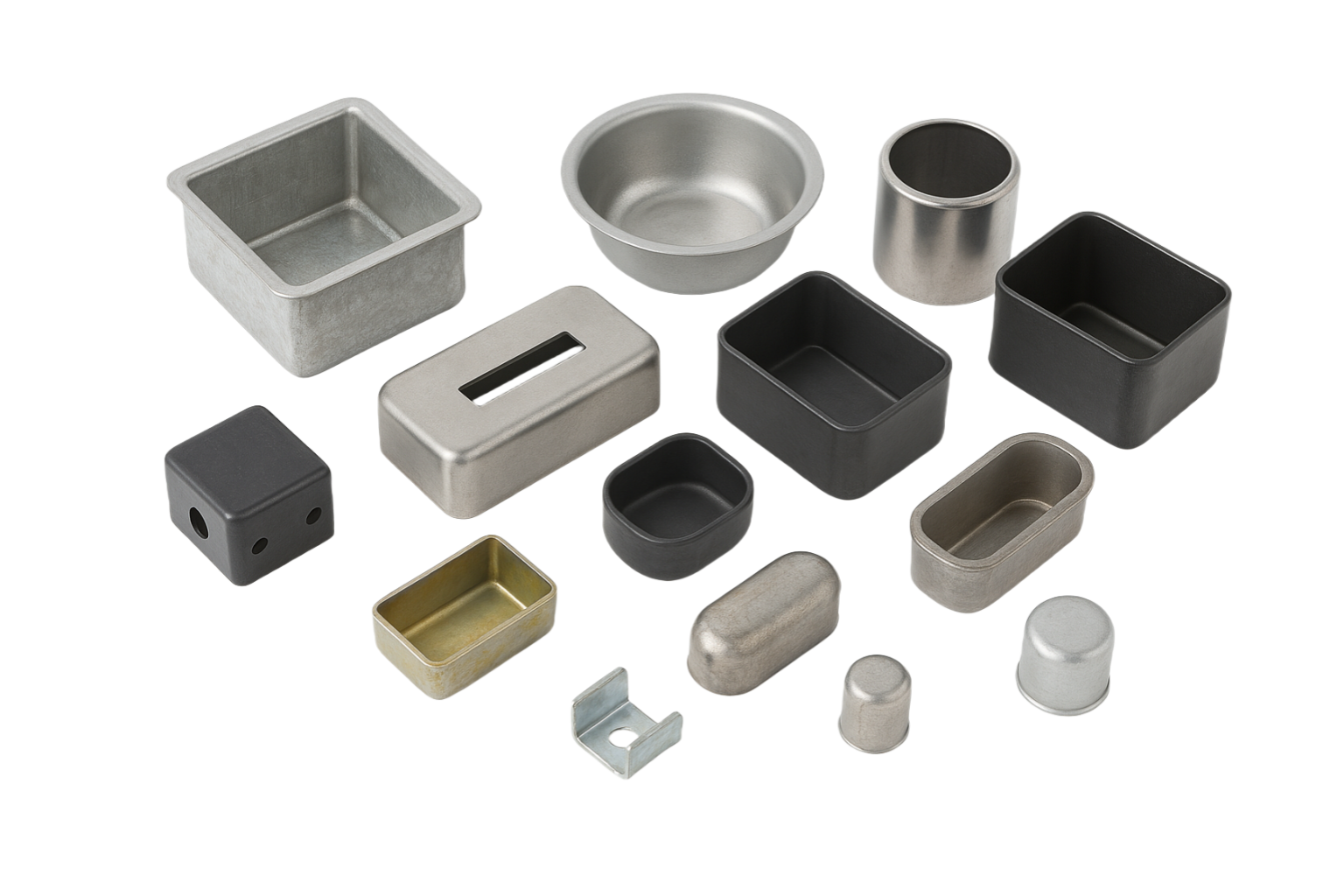
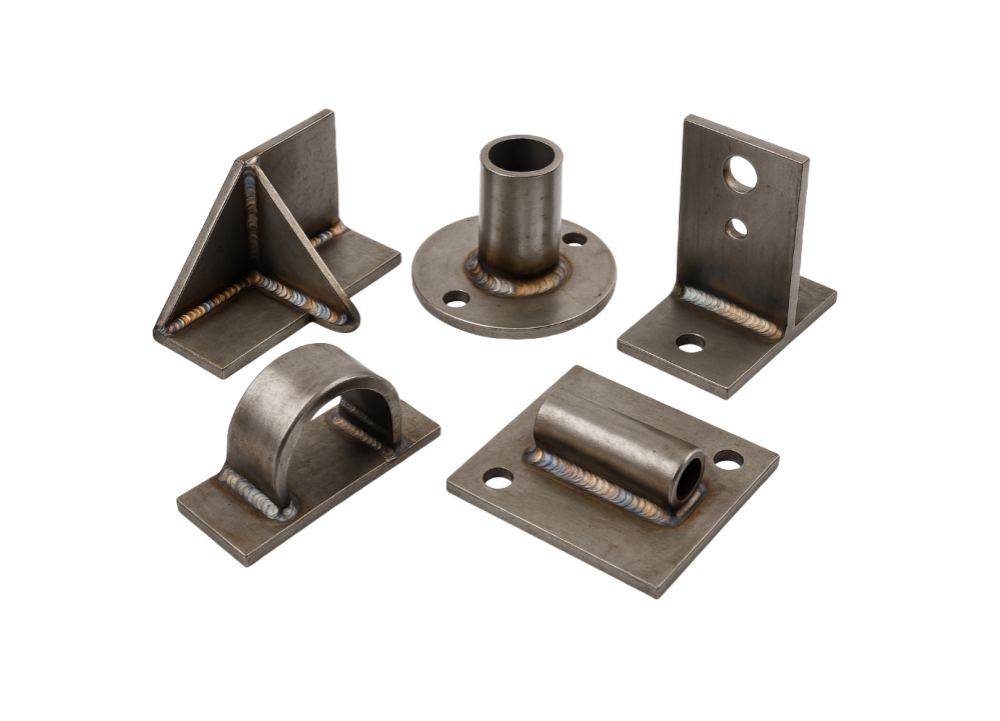
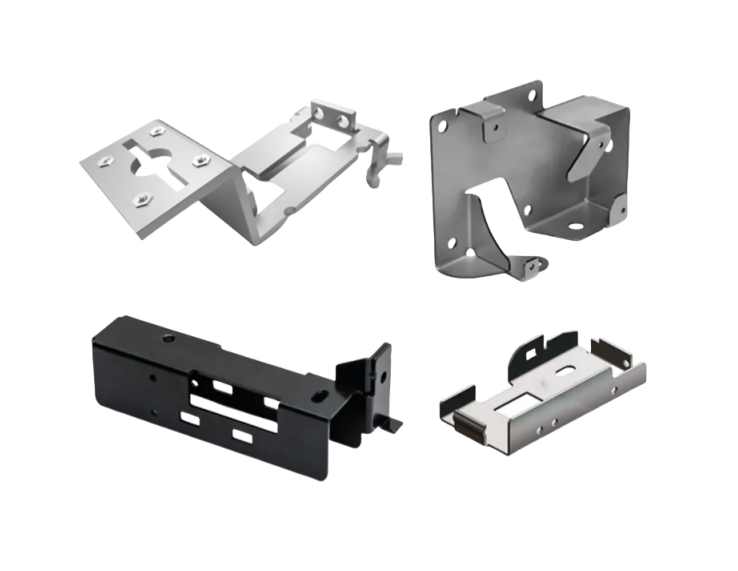
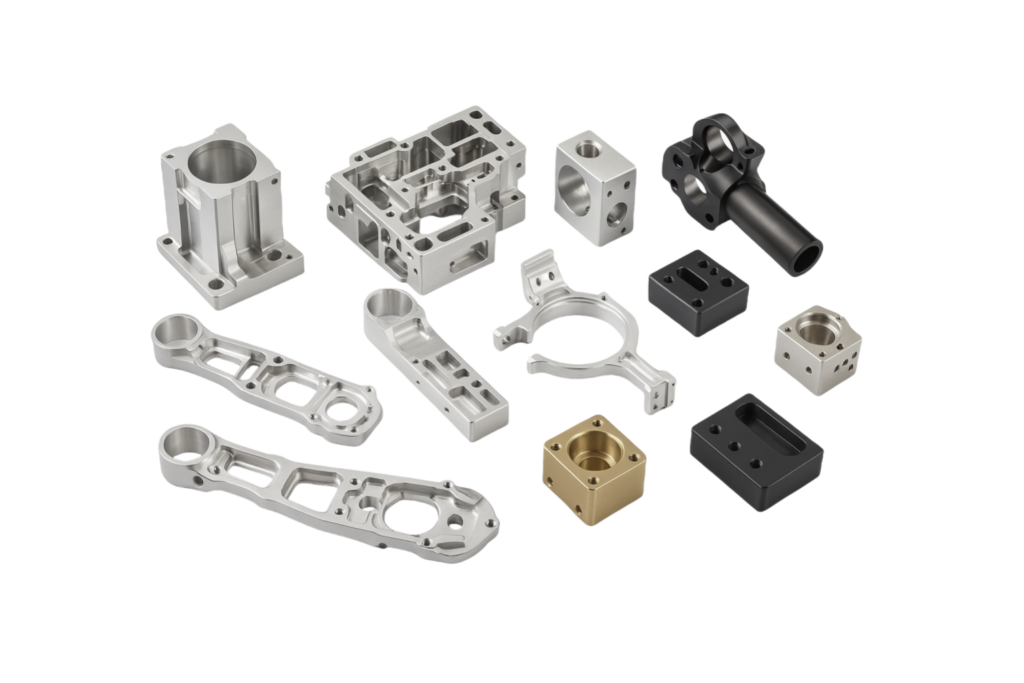
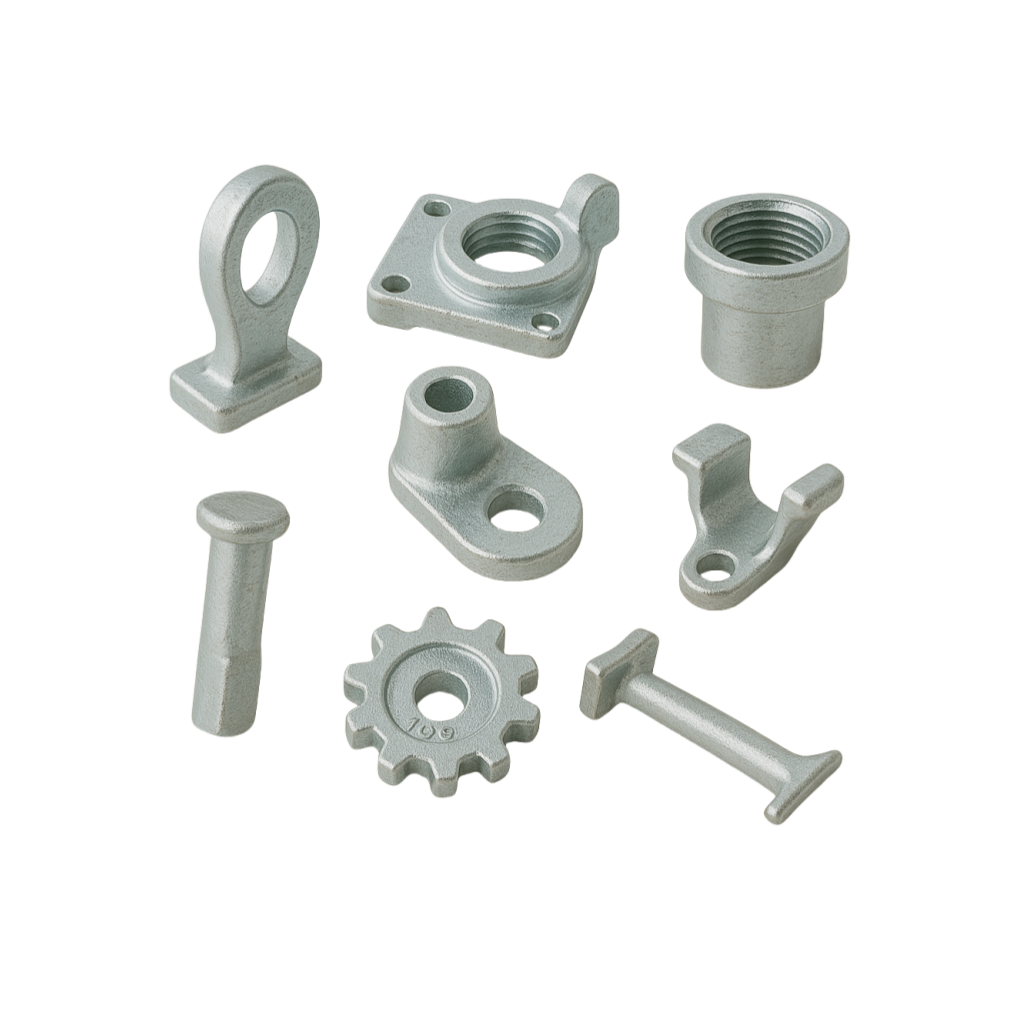
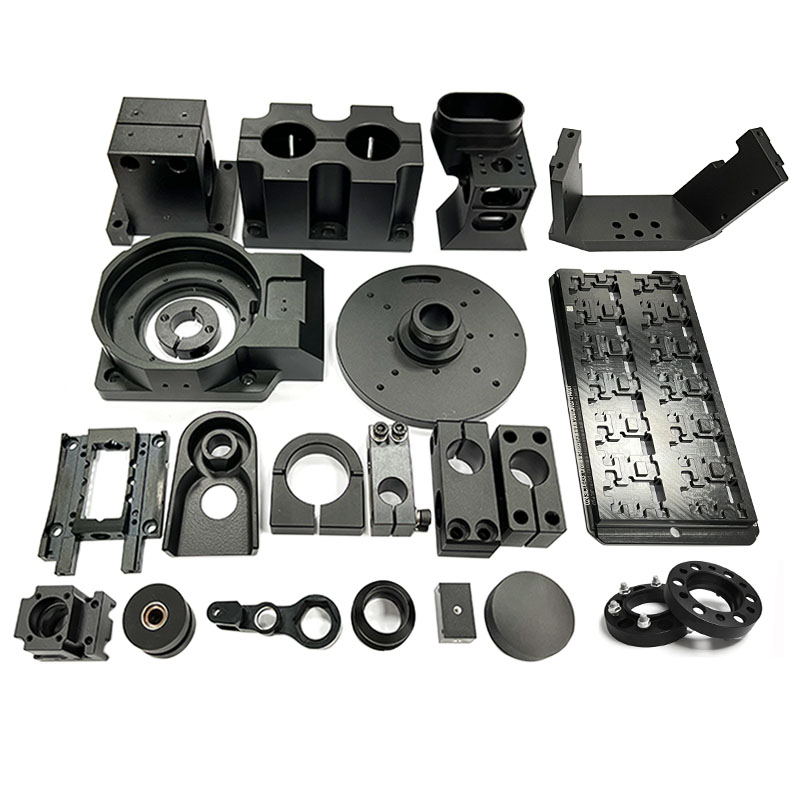
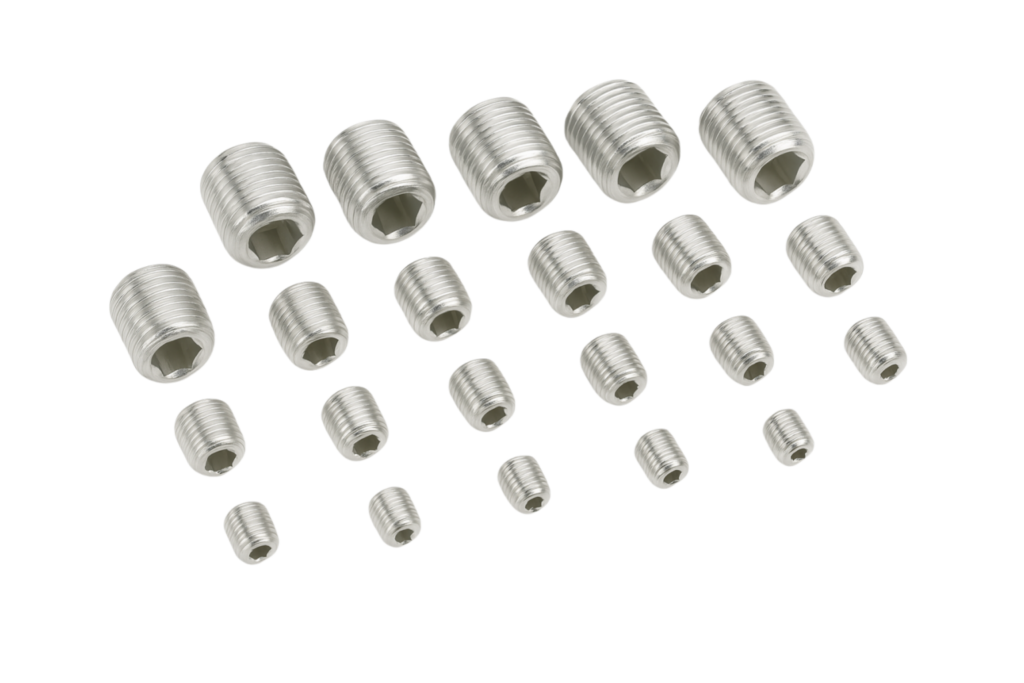
What Sets Us Apart
We offer a wide variety of custom metal parts to meet your needs and budget.
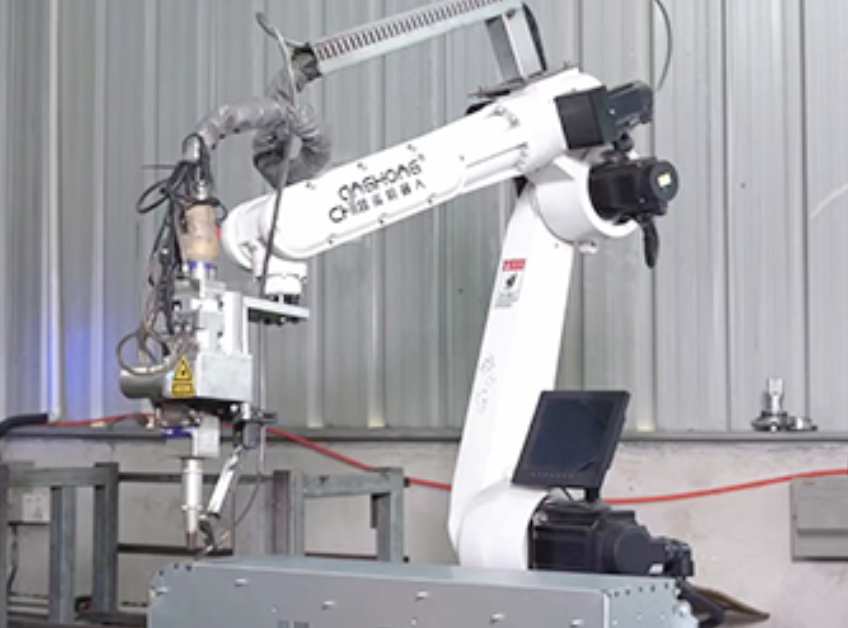
Well-Equipped Facility
We are equipped with fully automatic production lines, as well as specialized mold manufacturing and deep processing workshop.Can provide high-precision production for your products.
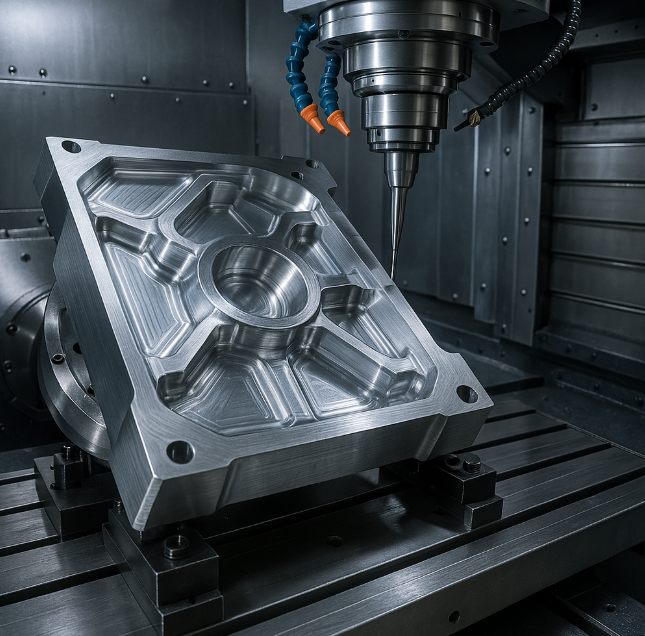
Advanced Manufacturing Capabilities
We are equipped with a number of stamping production lines, our advanced machines to ensure the highest efficiency, improve your production efficiency.
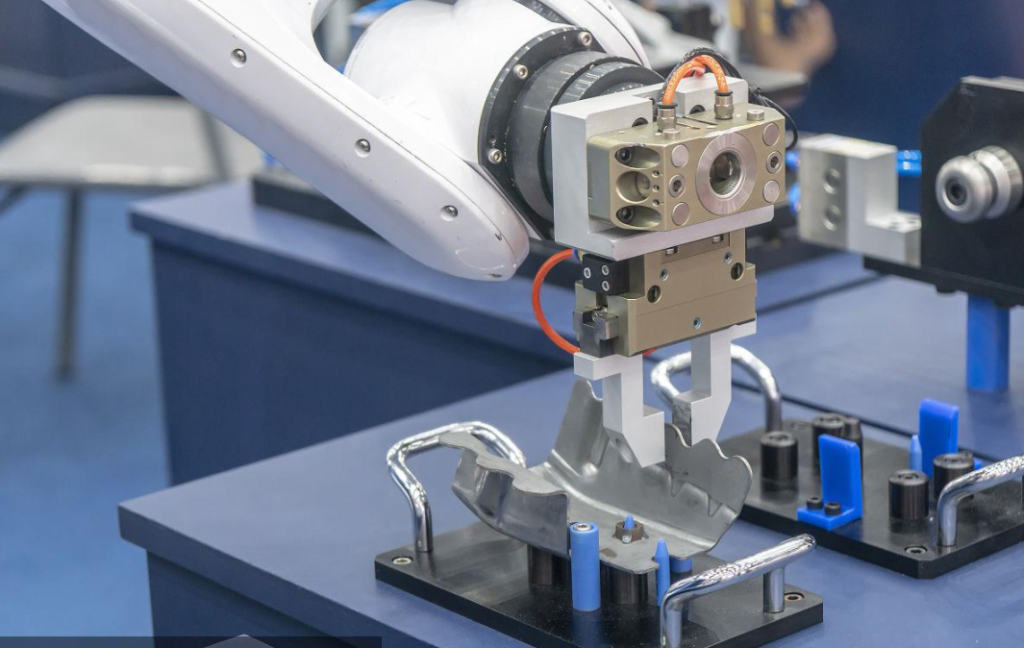
Competitive Pricing
Up to 10% savings on raw material costs, achieved through bulk ordering and a stable supply chain supported by our streamlined manufacturing process, enable us to offer you highly competitive pricing.
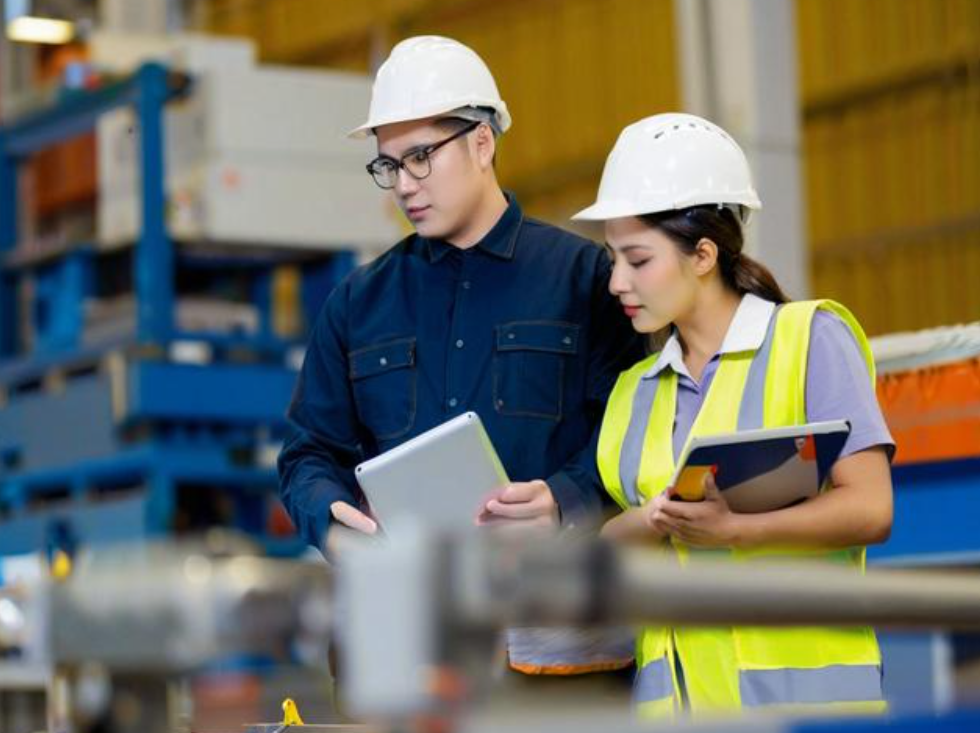
Comprehensive Support & Services
From pre-sales consultations to manufacturing and after-sales care, we deliver tailored solutions based on your design requirements, with a guaranteed quote within 24 hours.
Chapter 1
Product quality control
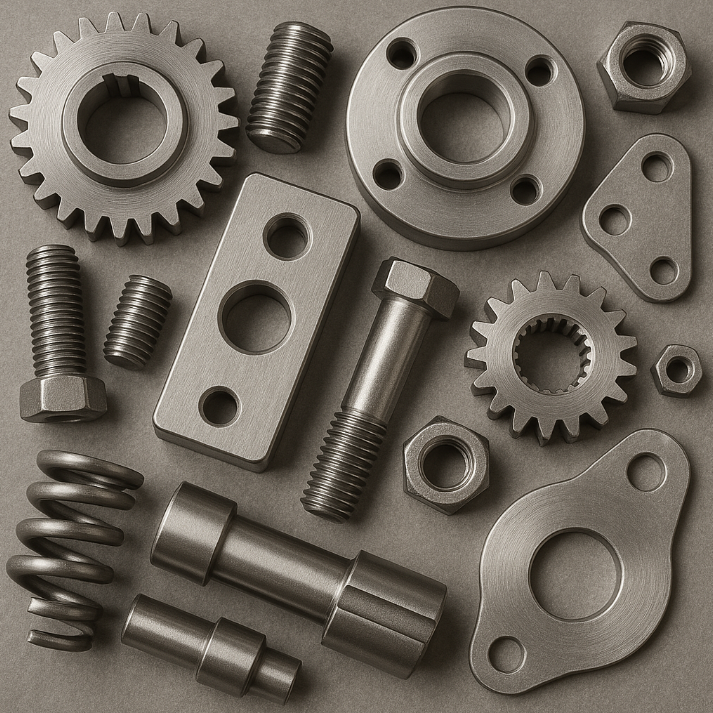
Metal Products are essential components widely used across various industries due to their durability, strength, and versatility. These products can take various forms such as plates, rods, strips, and more, depending on the specific application.
Common types of metal products include stamped parts, casting components, CNC machined parts, and fasteners, which are integral to the functioning of industrial machinery, electronics, and automotive systems.
At Prime, we offer a wide selection of high-quality metal products that are customizable to meet your specific needs. With over 20 years of expertise and ISO certifications, our products ensure consistent quality and timely delivery to clients worldwide.
Our company ensures the quality of products through a strict quality control system. All production processes are professional quality inspection personnel for inspection. We hold ISO 9001 certification, and before each shipment will be a comprehensive quality testing to ensure that products meet customer requirements.
Chapter 2
Sources of raw materials and production capacity
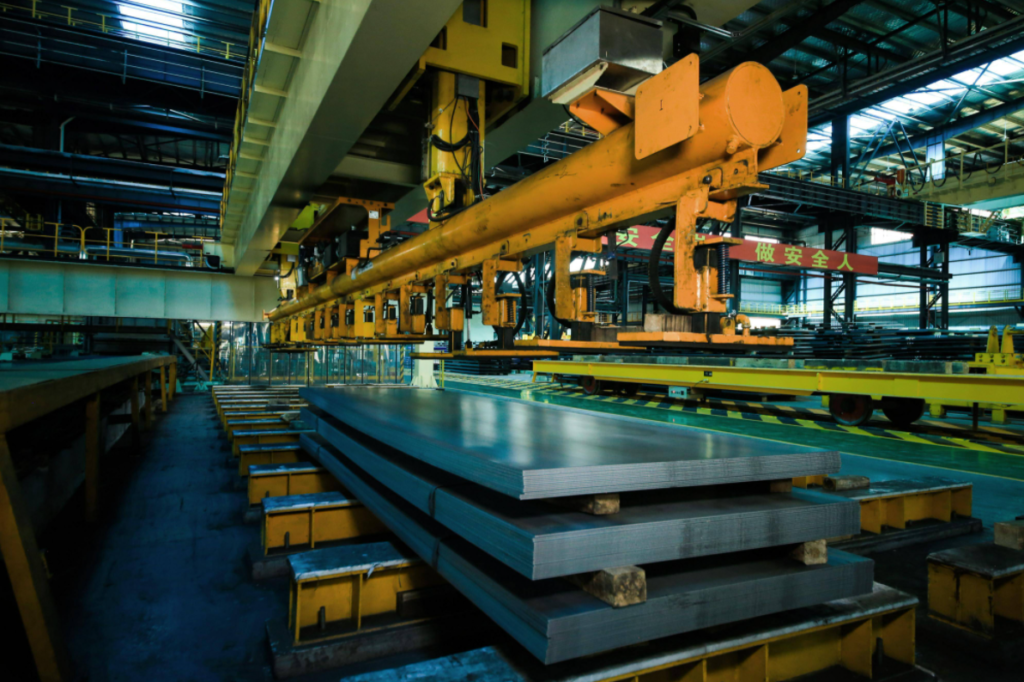
We have long-term cooperation with a number of domestic and foreign high-quality steel suppliers to ensure a stable supply of raw materials. We can provide raw material quality certification and compliance reports to ensure that each batch of raw materials are in line with international standards.
And our annual production capacity of over 5000 tons, to meet the needs of most customers. According to your demand, we can adjust the production plan to ensure timely delivery.
At Prime, we provide you with revolutionary parts for your success by virtue of our high-quality raw material supply and strong production capacity.
Chapter 3
Advantages of Metal Components
- Metal components are widely recognized for their superior performance and versatility in various industrial applications. Compared to traditional materials, such as plastics and composites, metal parts offer a broad range of significant advantages:
- Dimensional Stability:Metal components, such as stamped parts and CNC machined components, ensure high precision and consistent dimensions throughout production. This results in enhanced accuracy and reliability, making them ideal for demanding applications that require uniformity.
- Superior Durability:Metals, especially alloys like stainless steel, titanium, and aluminum, are known for their exceptional strength and resistance to wear. These materials are designed to withstand extreme conditions, ensuring a longer service life compared to other materials like plastics or rubber.
- Energy Efficiency:Many metal components, such as cast parts and fasteners, are highly efficient in energy transfer and mechanical performance. Their ability to operate under high pressure and temperature conditions reduces energy consumption and optimizes system performance, contributing to overall energy savings in industrial machinery.
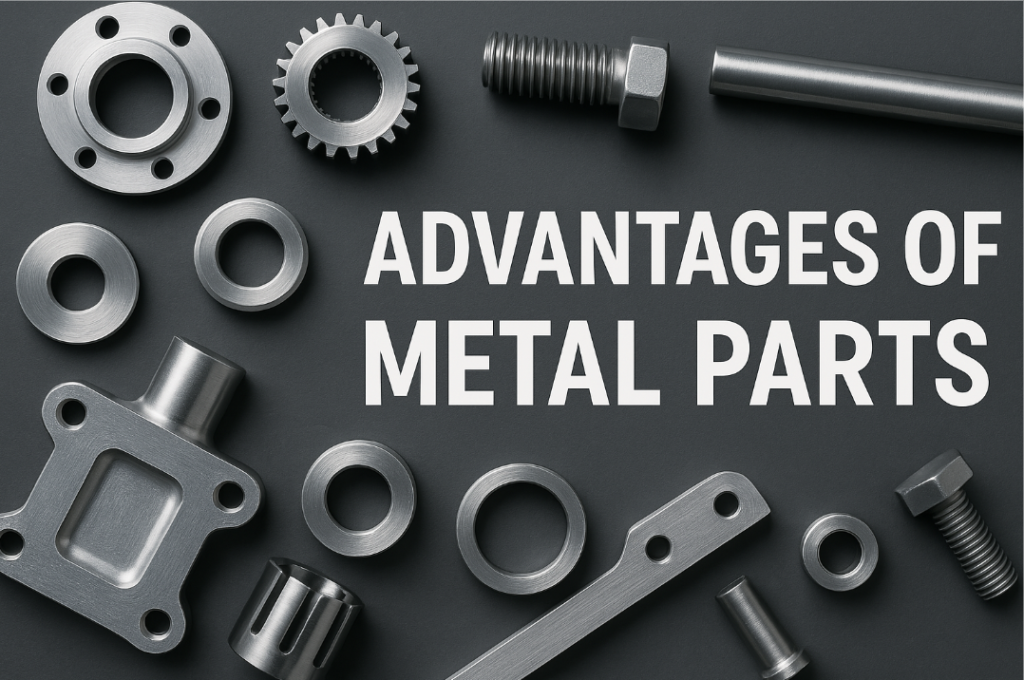
- Enhanced Structural Performance: Metal parts offer superior strength, durability, and load-bearing capabilities. With enhanced mechanical properties, they are able to perform effectively under high-stress conditions, ensuring reliability and safety in critical applications.
- Improved Operational Efficiency: Metal components are less prone to issues like deformation or failure under stress, which can be common in plastic parts. Their strength and reliability ensure smoother operations in machinery, reducing downtime and maintenance costs.
- Manufacturing Flexibility:The flexibility of metal materials allows for a wide variety of fabrication methods, from stamping and casting to CNC machining. This adaptability makes it easier to produce metal components with precise specifications, catering to diverse industry needs.
Summary:In conclusion, metal components offer outstanding advantages, including strength, durability, energy efficiency, and environmental benefits. Their versatility and performance make them the material of choice for a wide range of industrial applications, setting them apart from traditional materials in terms of reliability, longevity, and cost-effectiveness.
Chapter 4
Guide for the design of metallic components
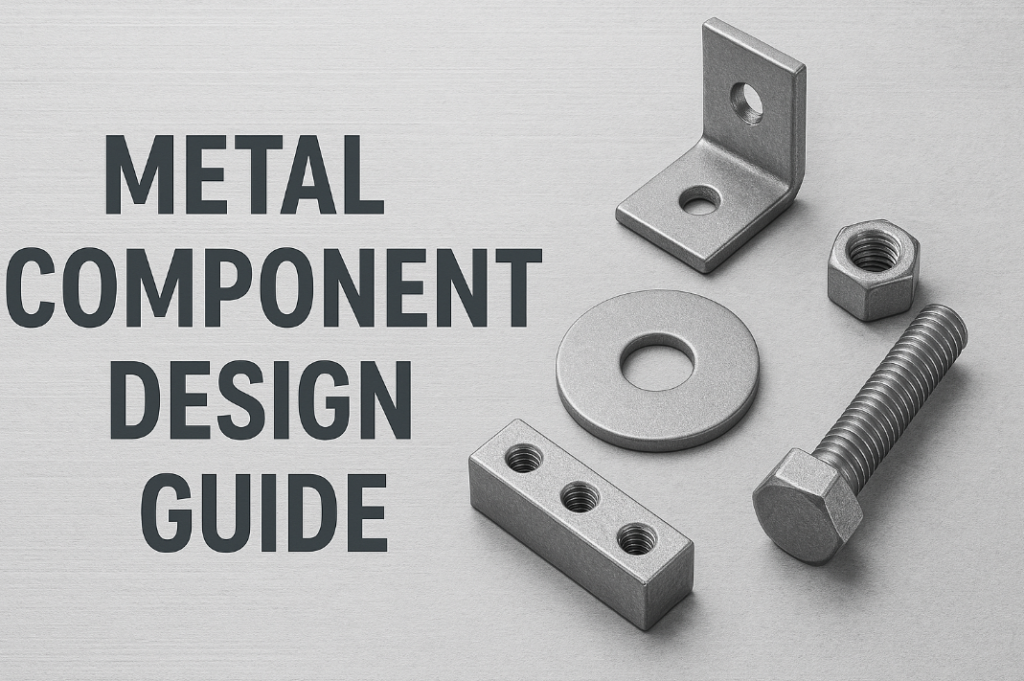
At Prime, we specialize in creating custom-designed metal components tailored to meet the specific needs of our clients. Working alongside leading contractors and metal fabricators, we are committed to producing high-quality parts in various configurations, including:
- Sheets: We provide metal sheets in both square and rectangular patterns, manufactured to precise specifications for a wide range of industrial applications.
- Strips, Foils, and Plates: Our metal strips, foils, and plates are engineered with precision, ensuring they meet the exacting needs of our clients in industries such as automotive, electronics, and machinery.
- Metal Forms: We offer a variety of metal forms, from expanded metal and meshes to corrugated plates and perforated designs, providing flexible solutions for diverse applications.
- Design Approach: Our design philosophy focuses on optimizing the functionality of each metal component. By carefully considering factors such as strength, durability, and ease of fabrication, we ensure that each part performs efficiently while minimizing production costs.
This attention to detail results in superior operational performance, enhanced quality control, and greater value for our clients, enabling them to meet their specific needs while driving productivity.
Chapter 5
How to Select the Right Metal Component?
Selecting the ideal metal component is a key step in ensuring product quality, production efficiency, and long-term performance in any industrial application. The right choice can reduce costs, improve reliability, and streamline your entire manufacturing process. At Prime, we help our clients make informed decisions by considering a range of critical factors during the customization process.
- Application Requirements: Begin by clearly identifying the intended use of the metal component. Whether it’s for automotive, electronics, construction, or industrial machinery, each application demands specific material properties and precision.
- Material Selection: Choosing the right metal—such as stainless steel, aluminum, titanium, or custom alloys—is essential. Consider properties like strength, corrosion resistance, conductivity, and weight to match your operational environment.
- Manufacturing Method: Determine the most suitable production process for your needs—stamping, CNC machining, casting, or welding. Each method offers different levels of precision, cost, and production speed.
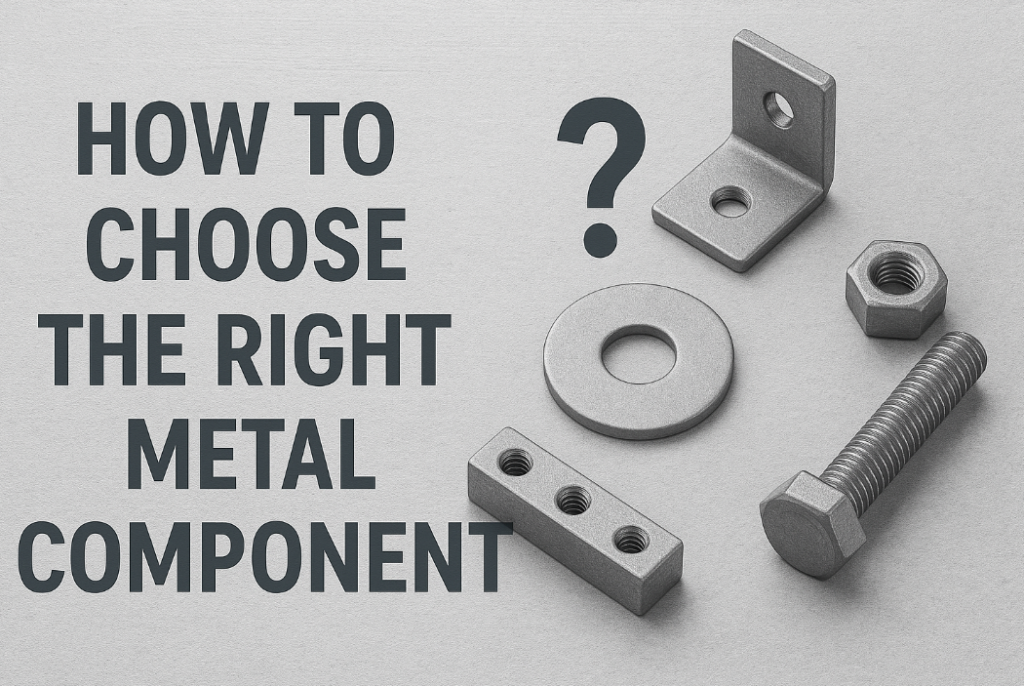
- Production Volume & Lead Time: Estimate your order volume and required delivery timeline. Our scalable production lines and fast turnaround ensure we can meet both small and bulk orders without compromising on quality.
- Cost Efficiency: Work with our experienced team to find the right balance between performance and price. We offer flexible solutions tailored to your budget, without sacrificing material quality or processing standards.
- Surface Treatment Needs: Depending on the application, surface finishing processes such as polishing, anodizing, or plating may be required to improve corrosion resistance, appearance, or durability.
- Dimensional Accuracy & Tolerance: Evaluate the tolerance requirements of your application. Components with tight tolerances are essential for applications where precision and fit are critical to performance and safety.
At Prime, we’re committed to helping you choose the perfect metal component for your project—customized to your technical specifications, application needs, and budget.Our promise is in our quality.
Chapter 6
Metal Component Pricing
Understanding the pricing of metal components involves recognizing the key factors that influence their cost. As a leading supplier of industrial hardware, Prime is dedicated to clarifying the various factors that affect the cost of metal parts.
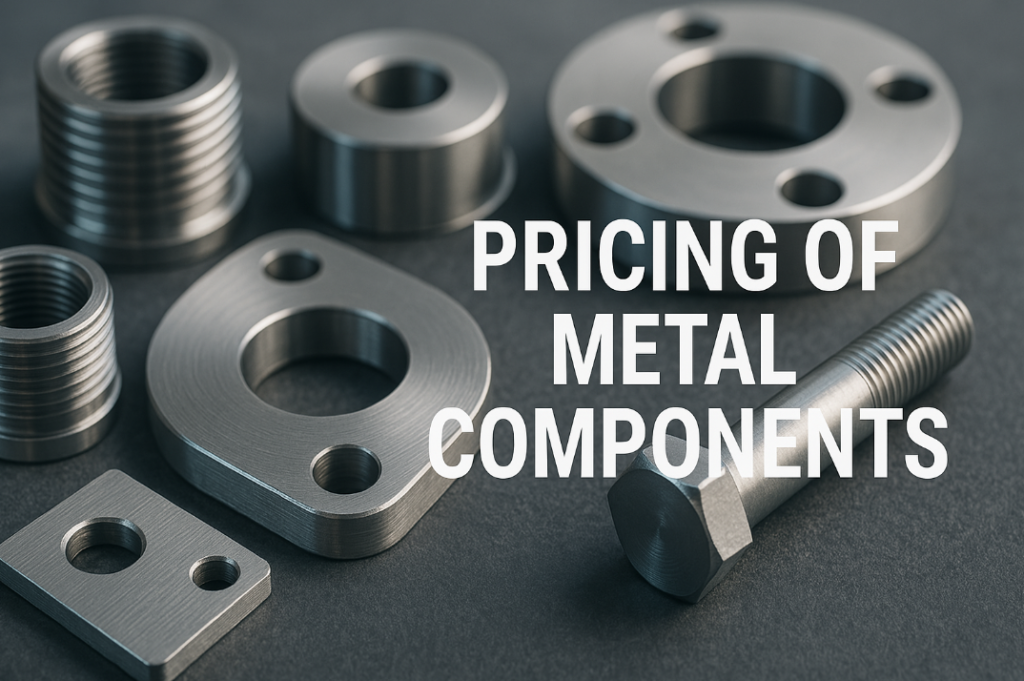
Decoding the Price: Material Costs: The price of raw materials, such as steel, aluminum, and other metals, is directly impacted by market fluctuations. As global demand shifts and material availability changes, the cost of these materials adjusts accordingly. Prime closely monitors these fluctuations to ensure competitive pricing for our customers.
Manufacturing Costs: Despite variations in material costs, manufacturing expenses tend to remain stable. However, costs related to labor, production equipment, and energy consumption can lead to slight price adjustments. We strive to maintain efficiency in production while ensuring high-quality standards.
Customization & Finishing: Customization options, such as specific dimensions, coatings, and finishes, can also affect the price of the metal components. Customization is often required for specialized projects, and Prime offers tailored solutions to meet your needs while remaining cost-effective.
Logistics & Shipping: Shipping and handling costs are another key consideration. The size, weight, and destination of the order can affect the final pricing. Prime works with trusted logistics partners to offer reliable and efficient shipping solutions.
At Prime, we advocate for transparent and competitive pricing. When you share your requirements with us, you can expect a comprehensive quote that fits your specifications. Contact us today to find the best metal components at the most competitive prices.
Chapter 7
We're There Every Step of The Way
One
Preparation for design and engineering
- Product Design: According to customer demand or product function, design the shape, size and structure of stamping parts.
- Die design: According to the product design, develop the corresponding stamping die, including progressive die, single engineering die, etc.
- Process planning: Determine the stamping process route, including blanking, bending, drawing and other processes.
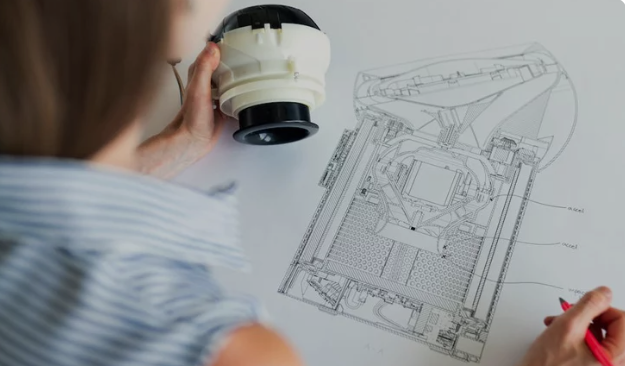
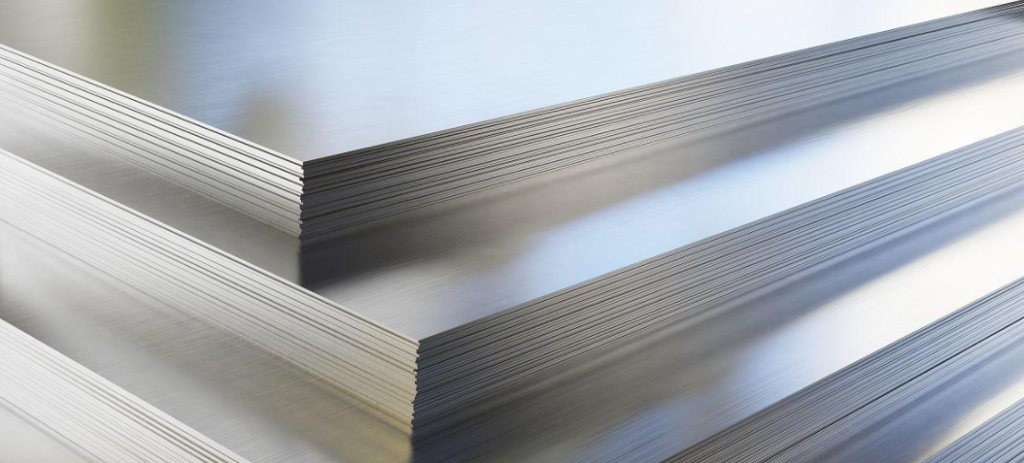
Two
Material preparation
- Material selection: According to product requirements to select the appropriate metal materials, such as steel, etc.
- Material Cutting: Cutting a coil or plate of metal into a size suitable for stamping.
- Material Inspection: Check the material thickness, hardness, surface quality, etc.
Three
Stamping
- Blanking: Cutting a sheet of metal into a desired shape.
- Drawing: The Drawing of flat metal into three-dimensional shapes, such as cups or boxes.
- Forming: The partial shaping of metal by means of a die, such as embossing, flanging, etc. .
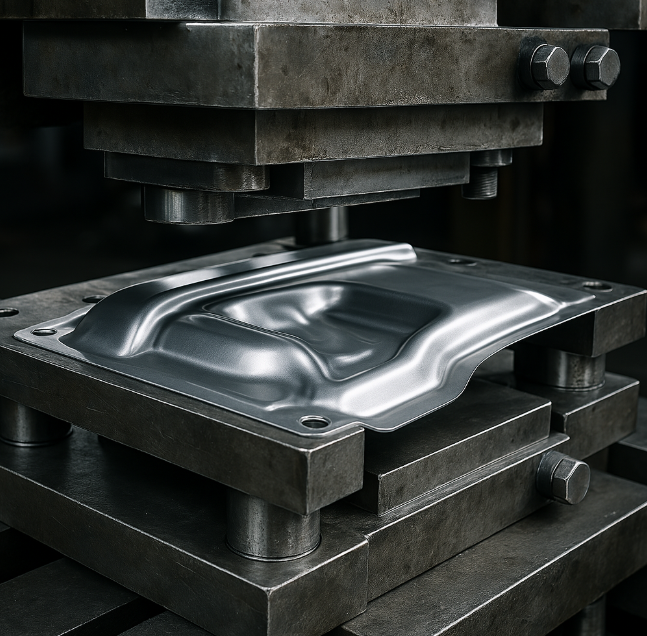
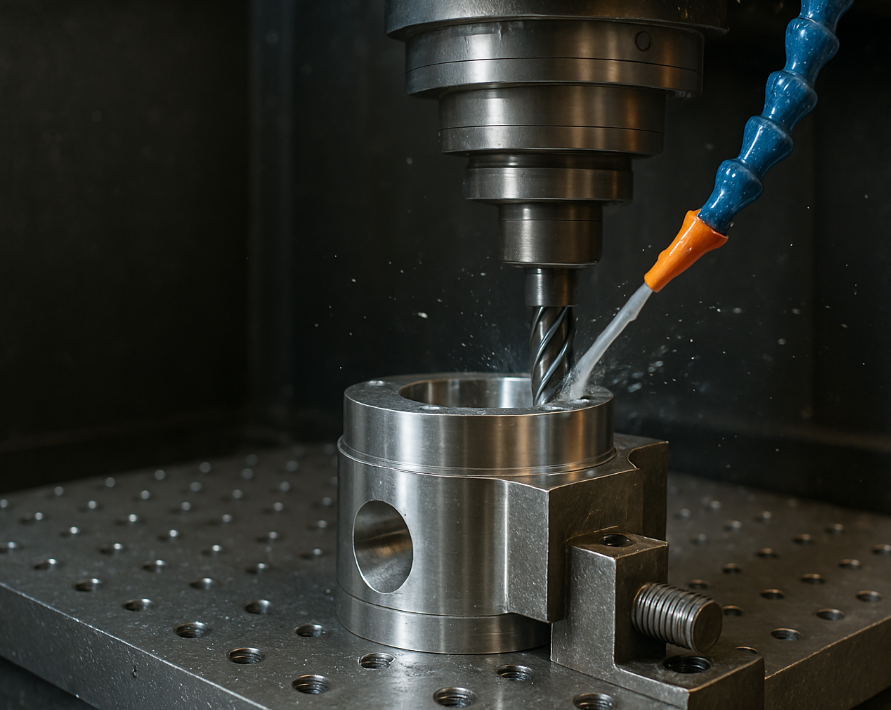
Four
CNC Machining
- communicate with technical engineer:Confirm machining feasibility with engineer during mold design phase;
- Feedback on production issues: Define CNC machining requirements (E. G. Tolerances, surface finish) to suppliers;
- Trade and documentation: Retrospective CNC process issues when analyzing stamping defects.
Five
Secondary processing
- Deburring: Removing burrs from the stamping process to ensure a smooth edge.
- Coining: Precise Coining of parts to improve dimensional accuracy.
- Welding: Welding parts that need to be assembled.
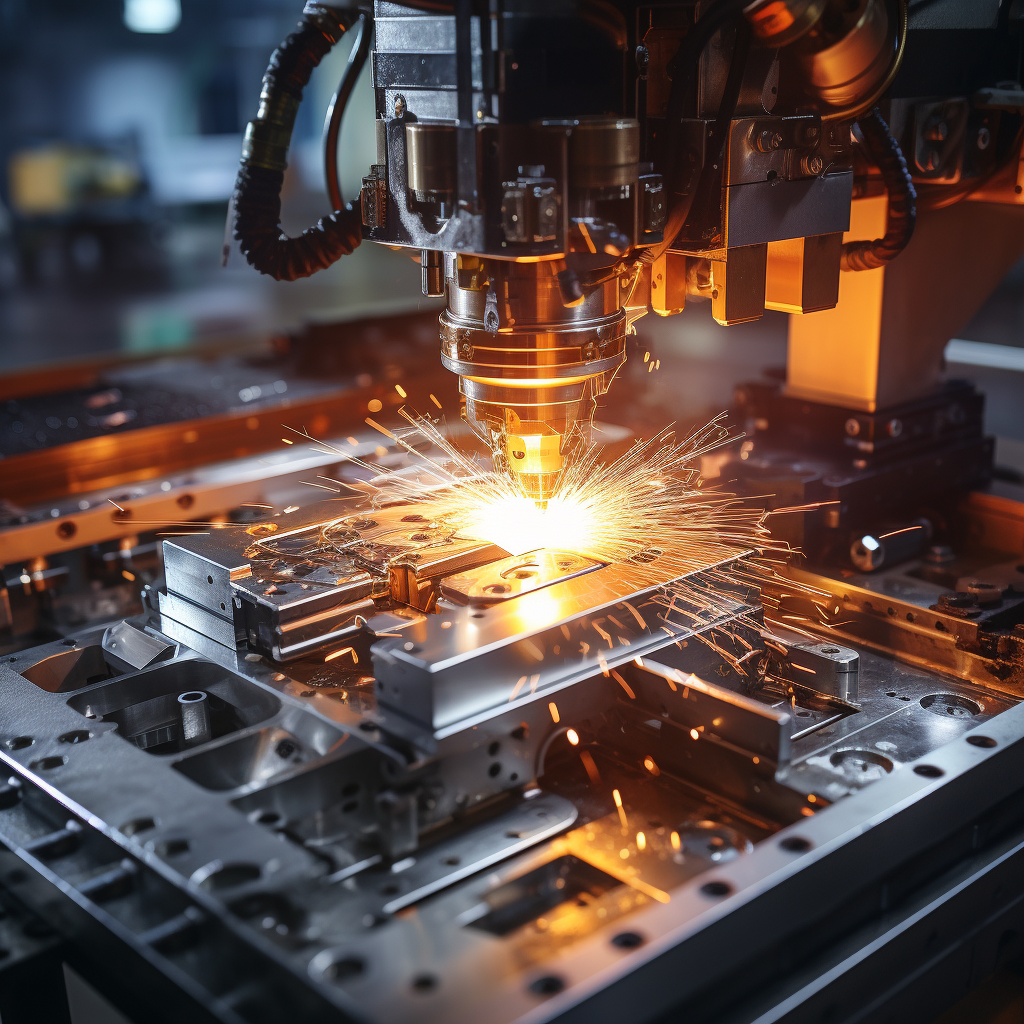
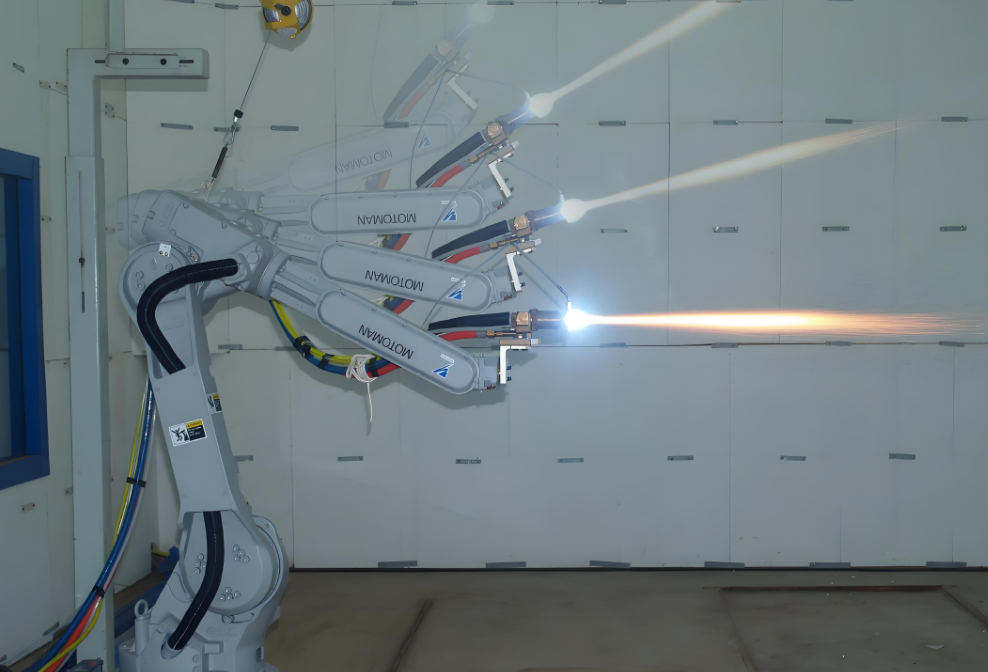
Six
Surface treatment
- Electroplating: To coat the surface of a part with a metal, such as zinc or nickel, to improve corrosion resistance.
- Painting: To spray on the surface of the parts to increase aesthetics and corrosion resistance.
- Polishing: Polishing the surface of a part to improve its finish.
Seven
Quality control
- First Article Inspection (FAI) : Inspection of the First Article before production to ensure compliance with design requirements.
- Dimensional Inspection: Checking part dimensions using calipers, projectors, etc. .
- Visual Inspection: Examination of a surface for defects such as scratches, cracks, etc.
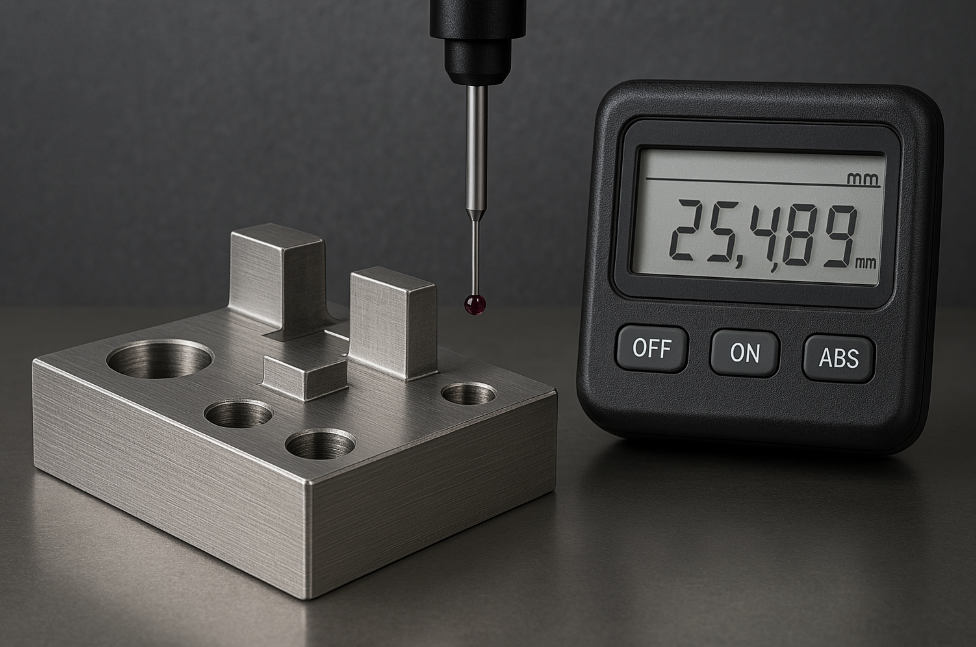
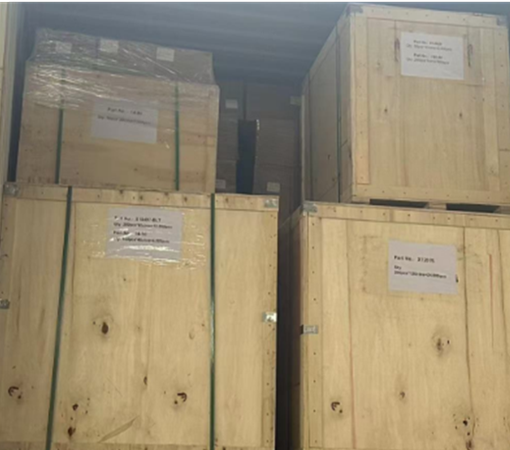
Eight
Assembly and packaging
- Assembly: The Assembly of several stampings into a final product.
- Cleaning: Removing oil and other impurities from the surface of a part.
- Packaging: According to the customer's requirements for Packaging, to ensure that the transport process is not damaged.
Nine
Logistics and delivery
- Inventory management: Manage the inventory of finished products to ensure timely delivery.
- Logistics: Arrange for the mode of transportation, such as by sea, air, or land.
- Deliver to customer: Deliver the product to customer and provide relevant documents, such as quality inspection report, invoice, etc. .
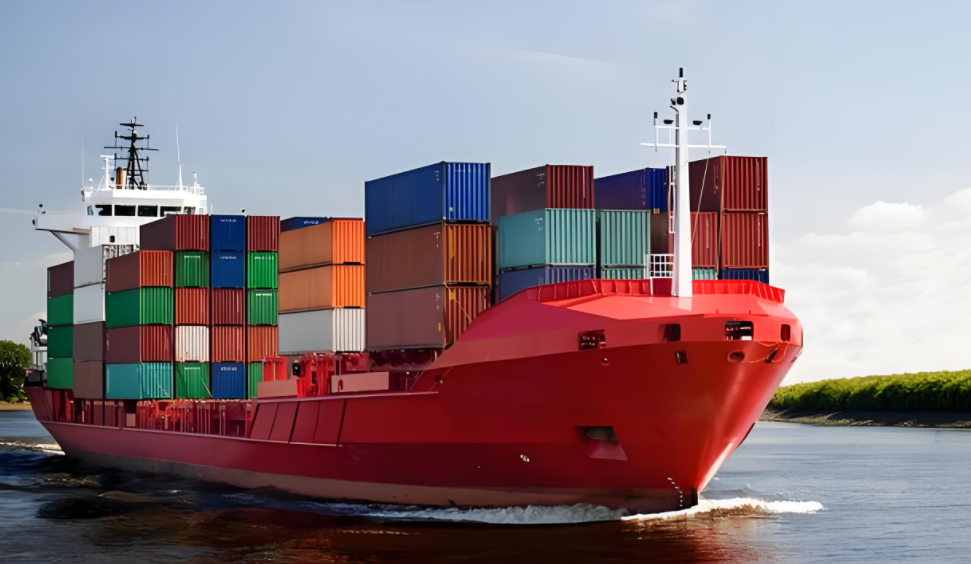
Chapter 8
Why Are Metal Components the Optimal Choice for Industrial Applications?
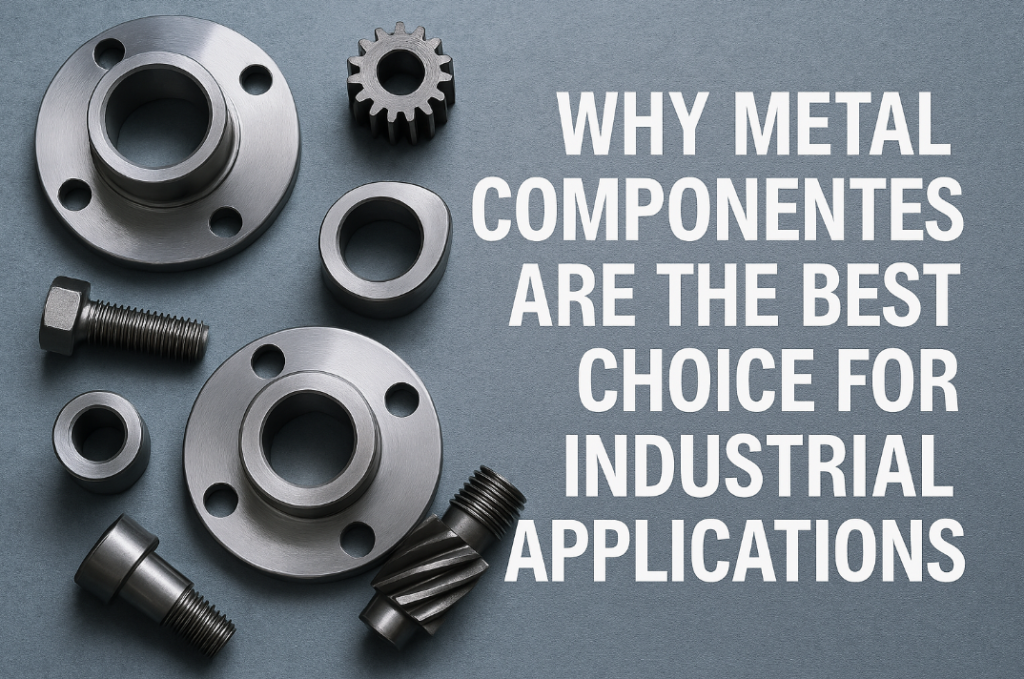
Metal components are at the core of many industrial operations, offering unmatched strength, durability, and versatility. Below, we highlight the key reasons why metal components are ideal for various applications, and how Prime maximizes these qualities:
The Metal Component Advantage
- High Strength: Metals are known for their exceptional strength, making them the perfect material for structural components that need to withstand heavy loads and high-stress environments. This reliability ensures that metal parts perform consistently in demanding industrial settings.
- Corrosion Resistance: Many metals, such as stainless steel, offer excellent resistance to corrosion, even in harsh environments. This quality makes them highly durable, extending the lifespan of components, and reducing the need for frequent maintenance or replacements.
- Versatility and Customizability: Metals can be shaped, treated, and finished in a wide variety of ways, making them adaptable to nearly any industrial requirement. Whether it’s precision CNC machining, stamping, or casting, metal components can be customized to meet specific design and functional needs.
At Prime, we harness the advantages of metal components to deliver products that meet the highest standards of performance. From stamping parts to CNC components, we provide reliable and durable solutions designed for industries across the globe.
Chapter 9
Metal Components Lifespan and Its Impact on Industry Success
The durability and reliability of metal components in various industrial applications are crucial, significantly influencing processes such as manufacturing, assembly, and material handling. The lifespan of these components directly affects operational efficiency, product quality, and sustainability in industries worldwide.
Understanding the Life of Metal Components
The longevity of metal components plays a vital role in:
- Cost-Efficiency: A longer lifespan results in fewer replacements, leading to decreased downtime and reduced operational costs.
- Consistent Output: Durable components ensure steady performance, which is essential for maintaining high-quality output and process efficiency.
- Sustainability: The durability of these components supports eco-friendly practices by reducing the frequency of replacements and the associated waste.
Determinants of Metal Component Lifespan
The life expectancy of metal components is influenced by several key factors:
- Operating Conditions: The combination of environmental factors, temperature, and pressure can affect wear and tear, influencing lifespan.
- Material Quality: High-quality materials, such as stainless steel or specialized alloys, play a crucial role in minimizing degradation and enhancing durability.
- Environmental Exposure: Harsh chemicals, moisture, or temperature extremes can accelerate corrosion or wear, shortening the lifespan of metal components.
- Maintenance: Regular inspection and maintenance are essential to ensure optimal performance and longevity of metal components.
- Load and Stress: The mechanical stress and strain exerted on components can significantly impact their structural integrity and lifespan.
- Design and Manufacturing Precision: Components designed with precision and manufactured to high standards generally exhibit superior durability and performance.
By managing these factors effectively, industries can maximize the lifespan of metal components, improving process efficiency, reducing costs, and promoting sustainability.
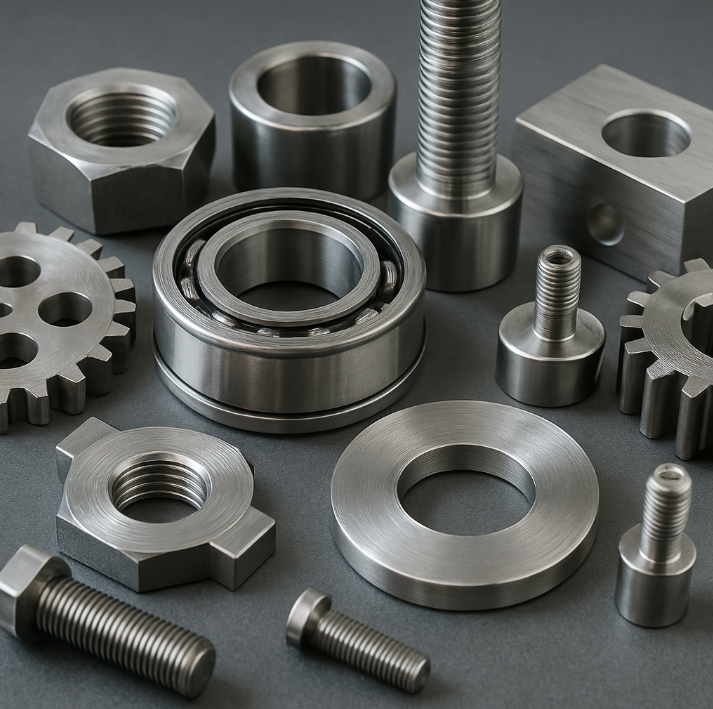
Customized Metal Component Solutions for Enhanced Performance
To meet the diverse demands of industrial operations, we offer a wide range of metal components, including:
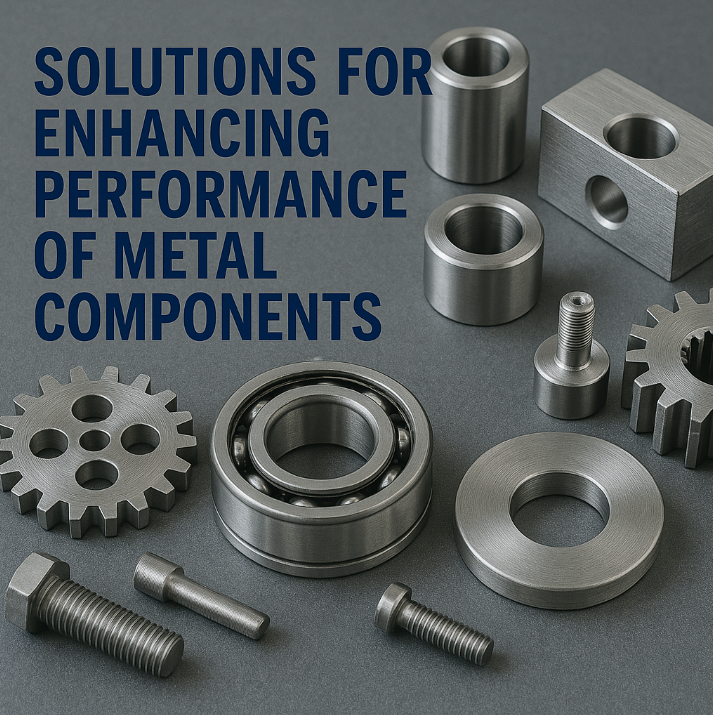
- Light Duty Components: Ideal for low-stress or intermittent use, these components provide cost-effective solutions for lighter applications.
- Moderate Duty Components: Designed for regular use under moderate conditions, these components balance performance and cost, making them suitable for standard industrial settings.
- Heavy Duty Components: Engineered for continuous operation in harsh environments, these components offer superior durability and longevity, making them perfect for demanding applications.
- Extreme Duty Components: Built for the most challenging conditions, these components provide exceptional performance and durability in highly corrosive or high-temperature environments.
By offering a variety of metal components, we empower industries to select the optimal solution that aligns with their specific operational requirements and budget. This approach ensures that every customer can achieve the best balance of performance, cost, and lifespan, ultimately enhancing the efficiency, sustainability, and cost-effectiveness of their operations. Our commitment to delivering versatile and durable metal components underscores our dedication to supporting industrial success and promoting sustainable practices worldwide.
Chapter 10
Precautions for Handling and Use of Metal Components
Metal components, including stamping parts, CNC parts, casting parts, screws, and plastic parts, are crucial in various industrial applications. These components, known for their strength, durability, and versatility, play an essential role in machinery, vehicles, and electronic systems. To ensure optimal performance, product quality, and longevity, it is critical to follow specific handling and usage guidelines.
Identification: Metal components can have different finishes based on the production process. For instance, stamped parts may exhibit smooth surfaces, while cast components may show varying textures. Proper identification ensures the correct part is used for the intended application.
Transport: Handle metal components carefully during transport to prevent damage. Ensure proper packaging, especially for delicate or precision parts like CNC-machined components.
Installation: Install parts with proper alignment and torque specifications. Avoid excessive force during installation to prevent distortion or failure.
Dismantling: During removal or replacement, avoid unnecessary impact or stress on metal parts. Use appropriate tools to avoid scratching or damaging the surface.
Storage Environmen:Store metal components in a dry, temperature-controlled environment. Humidity can cause corrosion, especially in untreated metal parts.
Protection: Use anti-corrosion coatings, such as oil or protective films, to extend the life of metal components, especially in environments with high moisture or saline exposure.
Electrolyte and Chemical Composition:
When metal components are used in electroplating or water treatment, ensure the electrolyte solution is free from aggressive chemicals like cyanide or fluoride. These chemicals can degrade the integrity of the metal and cause corrosion.
Cleaning Methods: Use soft cloths or brushes to clean metal parts. Avoid abrasive materials that could scratch or damage the surface.
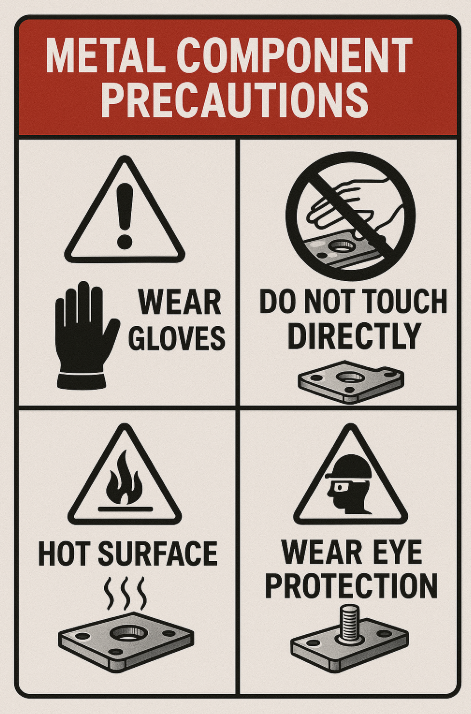
Handling of Special Components (e.g., CNC Parts):
CNC parts often have tight tolerances and need to be handled with extra care to avoid deformation. Use special tools designed for precise handling and avoid excessive pressure during installation.
By adhering to these precautions, metal components can achieve optimal performance, reduce downtime, and increase the longevity of industrial machinery and products.
Chapter 11
Application of metal parts
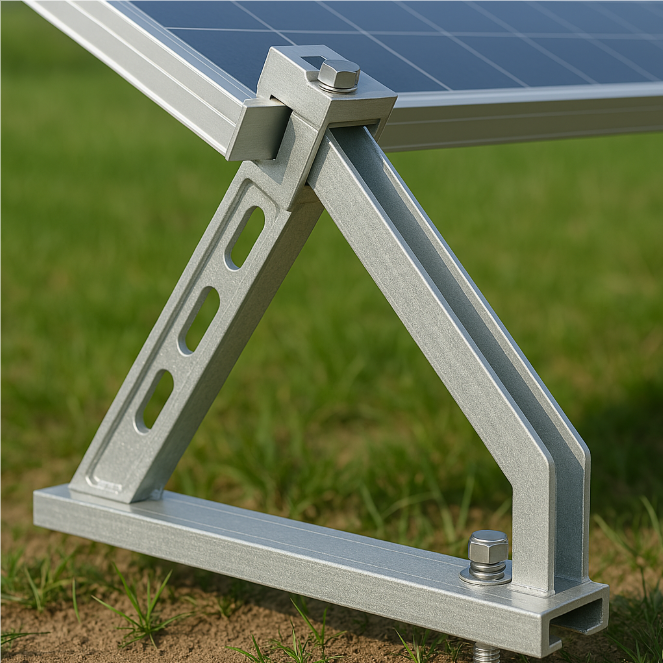
The energy industry
Application: Solar energy bracket, wind turbine parts, battery components, etc.
Features: Stamping parts with high strength and corrosion resistance, suitable for harsh environments.
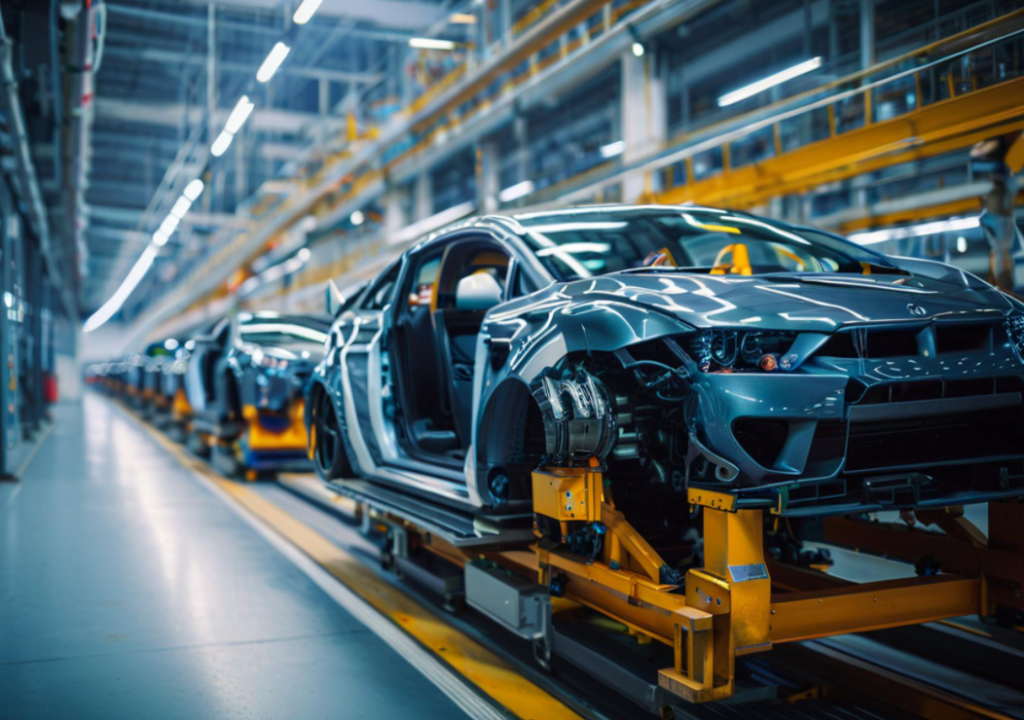
Car Manufacturing
Applications: Auto body parts, chassis parts, engine parts, doors, frames, fuel tanks and so on.
Features: Stamping parts with high strength, light weight and high precision, suitable for mass production.
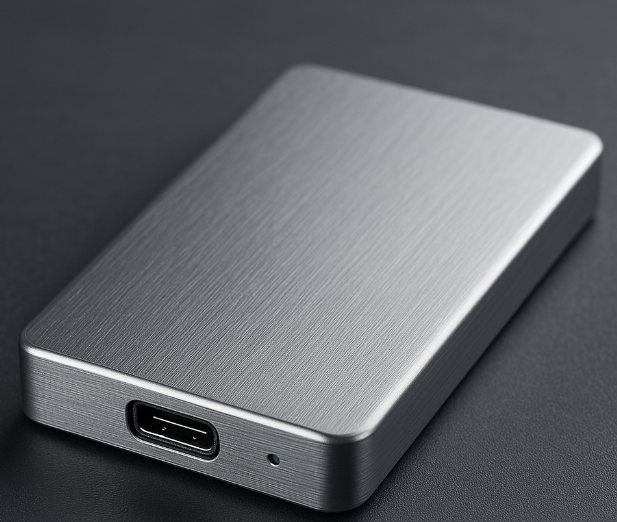
Electronic equipment
Applications: Electronic enclosures, heat sinks, connectors, shields, battery enclosures, etc. .
Features: Stamping process can produce small, precision and complex parts to meet the high-precision requirements of electronic equipment.
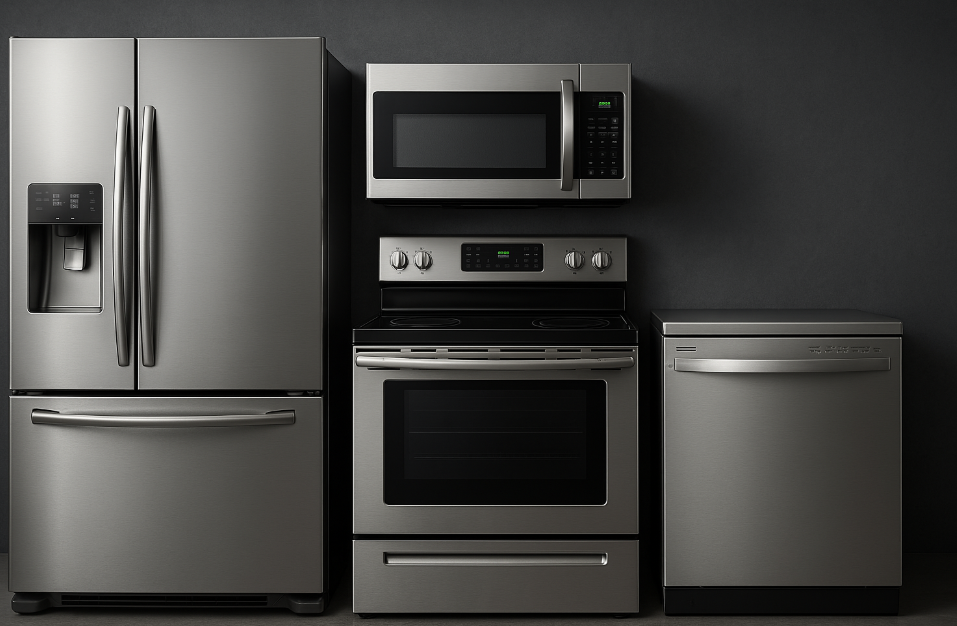
The home appliance industry
Applications: Refrigerators, washing machines, air conditioners, microwave ovens and other household appliances, the shell and internal structure.
Features: Stamping parts with good strength and appearance, suitable for mass production.
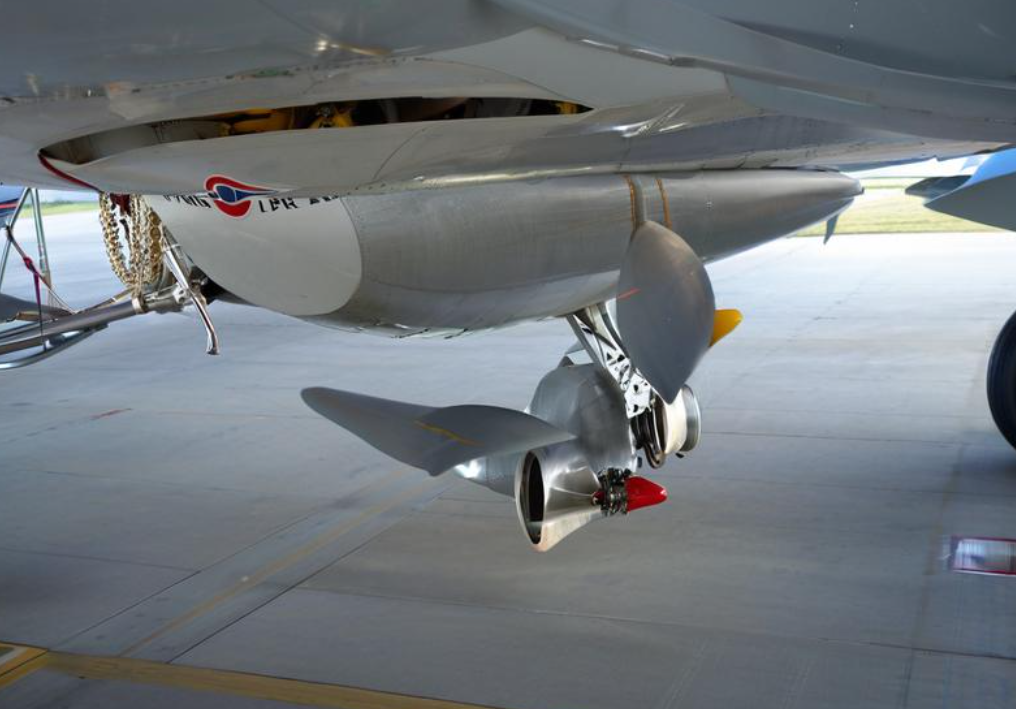
Aerospace
Applications: Aircraft structural parts, engine parts, spacecraft shells, etc. .
Features: Stamping process can handle high-strength alloy materials, meet the aerospace field of lightweight and high-strength requirements.
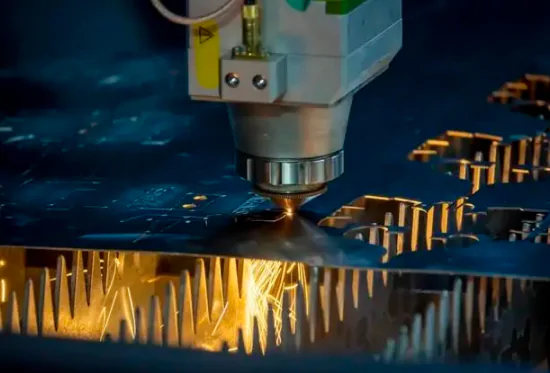
Hardware
Applications: locks, hinges, tools, fasteners, etc. .
Features: Stamping process for the production of small, standardized and large demand for parts.Can meet your stamping aspects of any needs.
Chapter 12
In Summary
When choosing the right metal parts manufacturer, the key is to select one that not only offers a wide range of customized products but also possesses deep expertise in various applications. This ensures that every unique requirement, from stamping and casting to precision machining, is met with precision and professionalism.
Prime stands at the forefront of the metal parts manufacturing industry with over 30 years of exceptional experience. Our commitment is reflected in the superior quality of our materials, processing techniques, and product specifications, all of which contribute to the success of numerous projects worldwide. Regardless of the project size, our experienced team is ready to meet your specific needs. Partner with Prime to discover the perfect solution tailored to your project’s requirements, reinforcing our position as your reliable partner in achieving your business goals.
Our Happy Clinets
Get in touch
Custom Hardware Parts Made Easy
Share detailed information about your needs, including drawings, reference images, and any specific ideas or specifications you have in mind.
Based on your requirements and design, we’ll provide a custom solution and send you a detailed quote within 24 hours.
Once you approve the design and quote, we’ll begin mass production and take care of the shipping, ensuring timely delivery.
Get a Free Quote
Reach out to us for a free quote and expert advice on your custom hardware needs. At Prime, we’ll provide the right solution for your project, ensuring quality and precision every step of the way.