Casting parts
The world's leading supplier of metal castings.
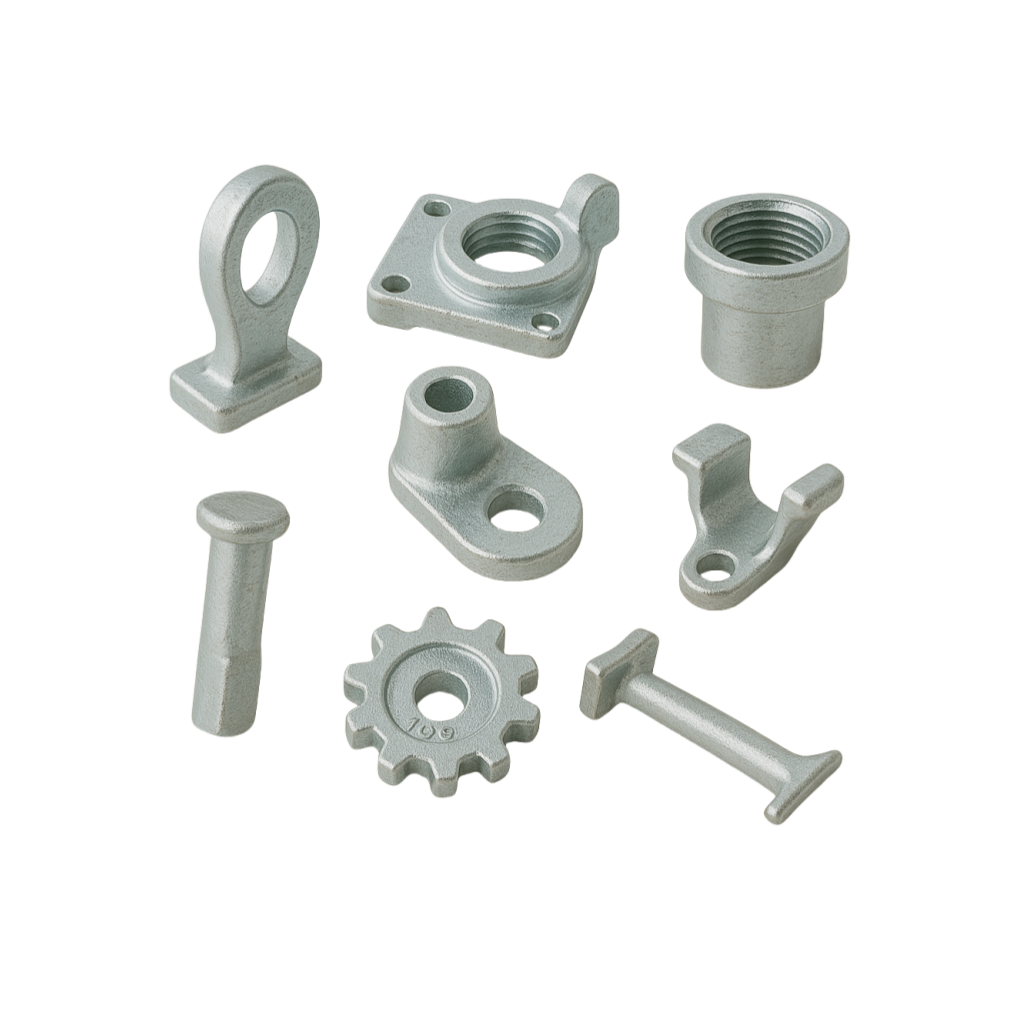
Custom made metal castings
Custom metal casting is an indispensable key component in modern industry, which is widely used in many fields. Through precision casting technology, we provide high-quality custom casting to meet the unique needs of all walks of life for metal parts. Whether it’s structural parts or sophisticated components, we can tailor our products to ensure they meet the highest standards of performance and quality and meet your needs and budget.
Table Of Contents For This Page
At Prime, we provide you with professional service and high-quality products.
Application fields of customized metal castings
Metal castings are widely used in many industries, including automobile, aviation, construction, machinery manufacturing, electronic equipment, energy, etc. . Its precision design and durability make it a key component of modern industrial production. Whether it is complex mechanical parts, high-strength structural components, or detailed appearance decoration, custom metal castings can provide a stable solution for a variety of industries.
General Hot Selling Products
Castings can be divided into several main types according to different processes, and each process has different characteristics and application fields. The following are some common foundry processes and their characteristics and applications:
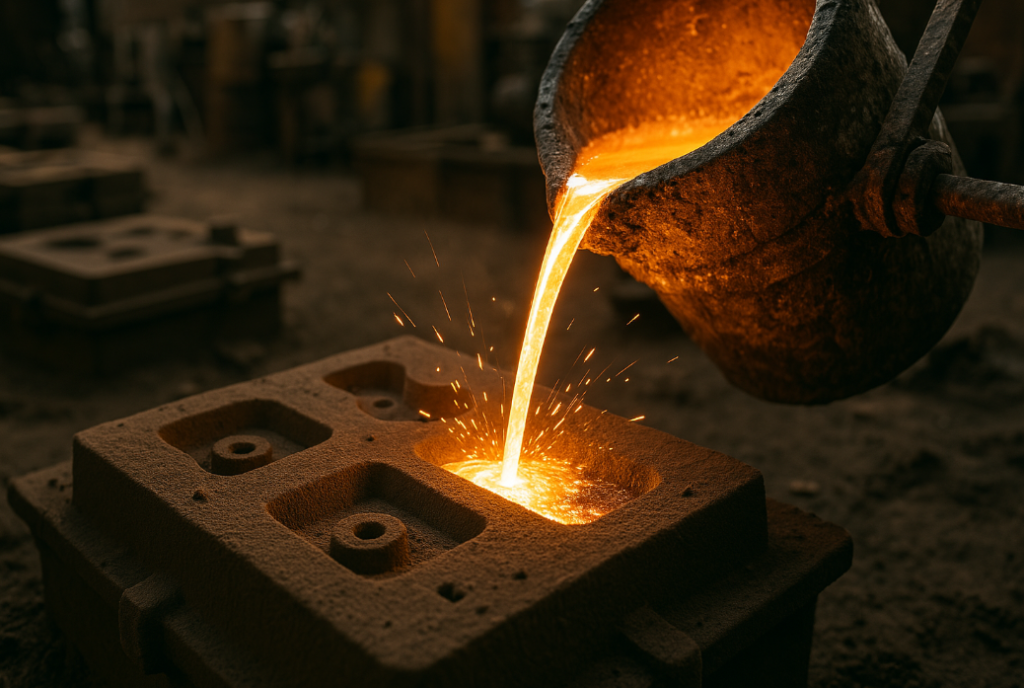
Sand casting
- Features:
- Sand casting is the most common and economical casting method, suitable for small and medium-sized batch production.
- Sand molds are made by hand or by machine using sand and binder.
- Mold can withstand higher temperature and pressure, suitable for casting complex shape castings.
- Low cost, suitable for most metal materials.
Applications: widely used in engines, pumps, valves, auto parts and other fields. Suitable for casting all kinds of metal materials, especially cast iron, aluminum alloy, steel, etc. .
Precision casting (lost wax method)
- Features:
- The mold used in precision casting is made of wax with high precision, which can produce very fine and complex parts.
- The manufacturing process is complicated and suitable for castings with very high precision requirement.
- Casting out of the product surface is smooth, without too much post-treatment.
Applications: commonly used in aerospace, medical equipment, jewelry, precision instruments and other fields. It is suitable for casting parts with complex shape and high precision.
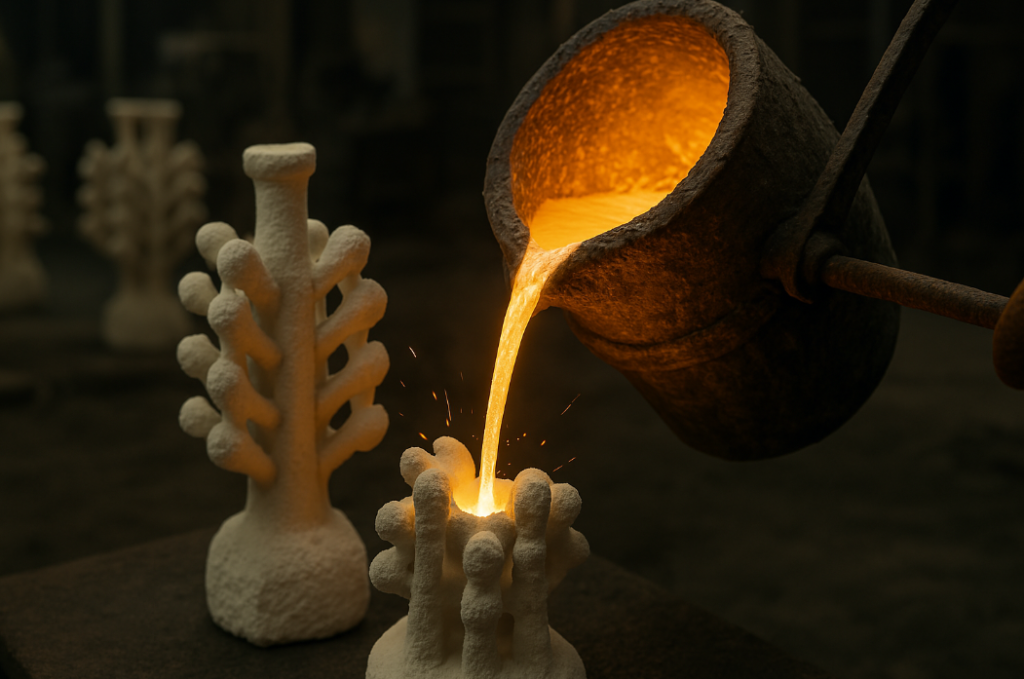
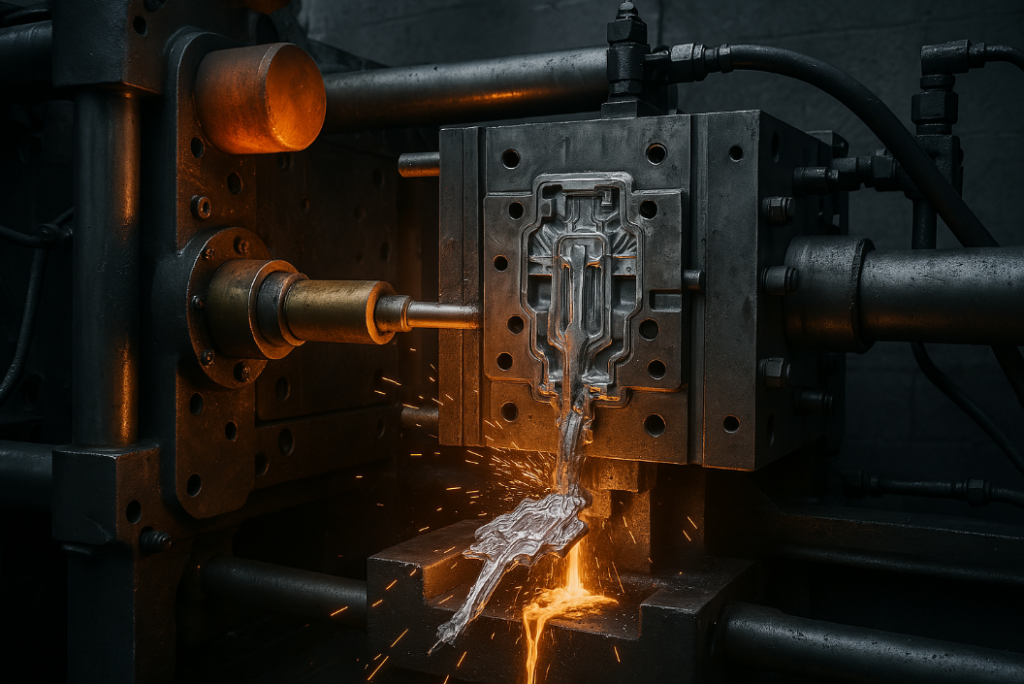
Die casting
- Features:
- Die casting process by high pressure will be molten metal into the steel mold, can produce smooth surface, accurate size of aluminum, zinc, copper and other alloy castings.
- High production efficiency, suitable for large-scale production.
- Long die life and good surface quality of castings.
Application: mainly used in automotive industry, home appliances, electronic equipment and other fields, especially for the production of complex shape parts, such as mobile phone shell, car shell, etc. .
High pressure casting
- Features:
- The process is similar to die casting, using high pressure to melt metal into the mold, mainly for aluminum alloy and magnesium alloy casting.
- Compared with die casting, high pressure casting requires higher injection pressure, and the castings produced by high pressure casting are more dense and have better mechanical properties.
Application: mainly used in the production of aluminum alloy and magnesium alloy castings, widely used in automobile parts, aerospace, precision instruments and other fields.
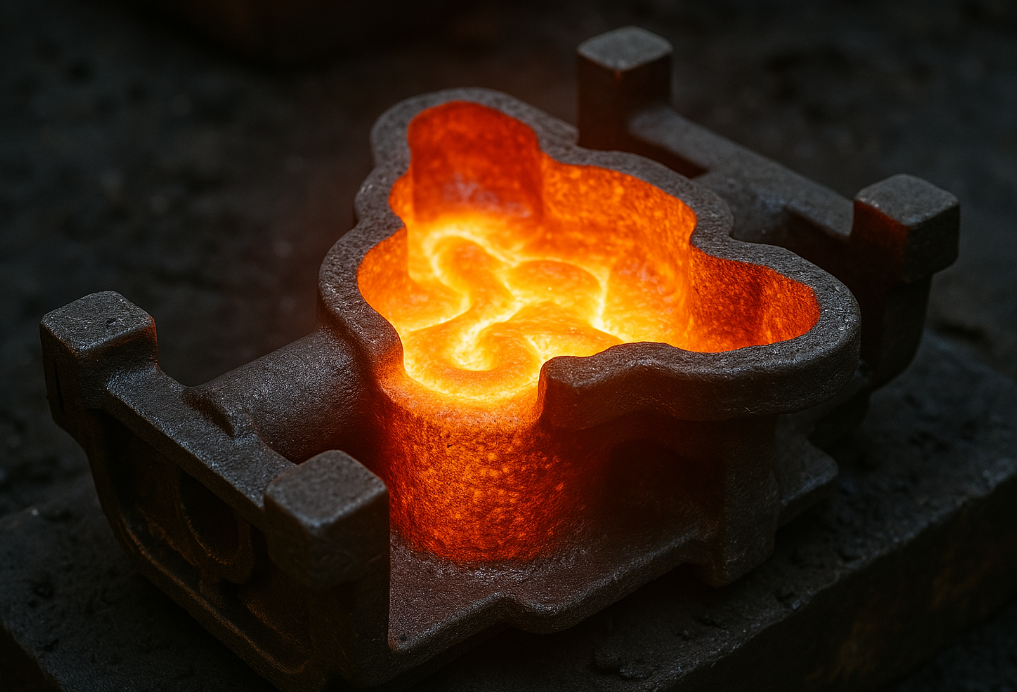
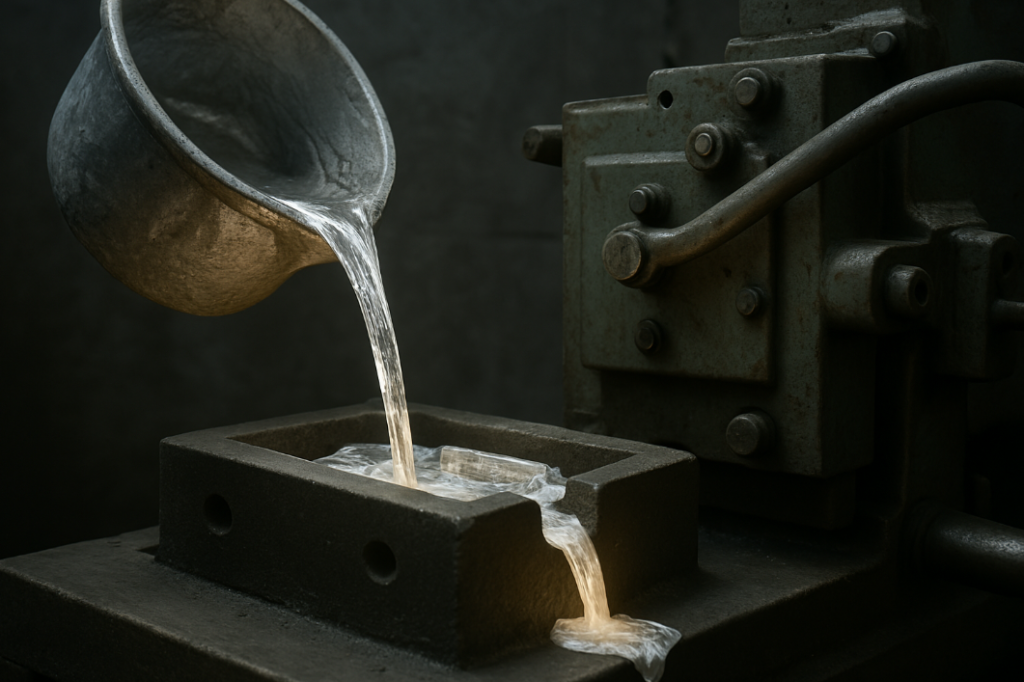
Cast aluminum alloy
- Features:
- Aluminum alloy casting has good corrosion resistance and good mechanical properties, which is often used in castings that need to be lightweight.
- The production of aluminum alloy castings can be realized by sand casting and die casting.
Applications: mainly used in automotive, aerospace, electronics, electrical appliances, furniture and other fields.
Centrifugal casting
- Features:
- Centrifugal casting by high-speed rotation of the mold to generate centrifugal force, so that molten metal evenly fill the various parts of the mold, suitable for casting tubular parts.
- This process is suitable for castings with large diameter and thin wall thickness.
Applications: mainly used in the production of pipes, cylindrical castings, widely used in petroleum, chemical, electric power and other industries.
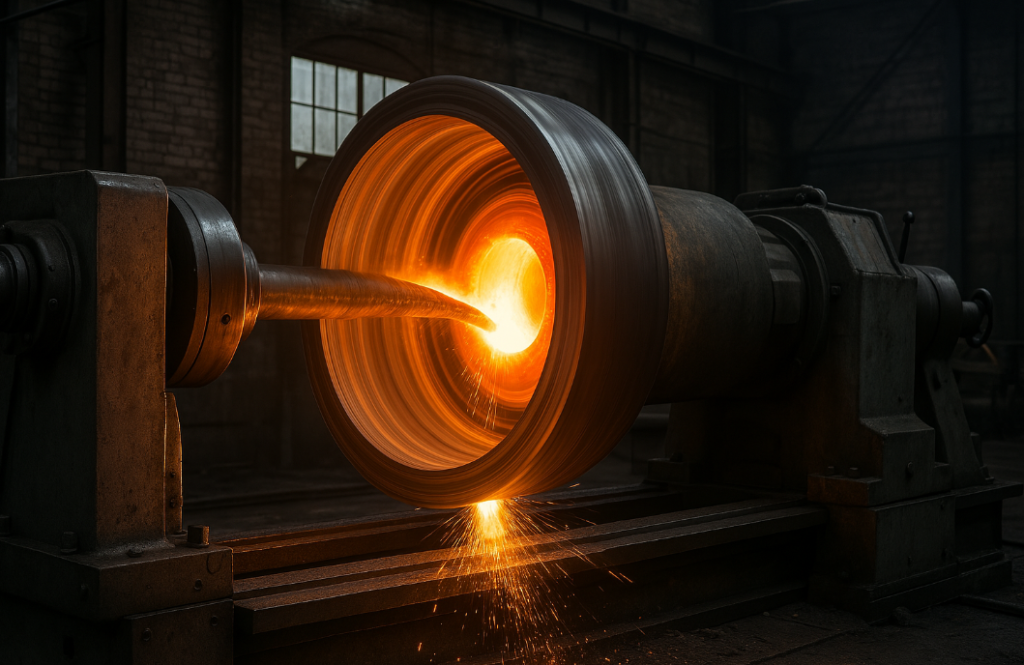
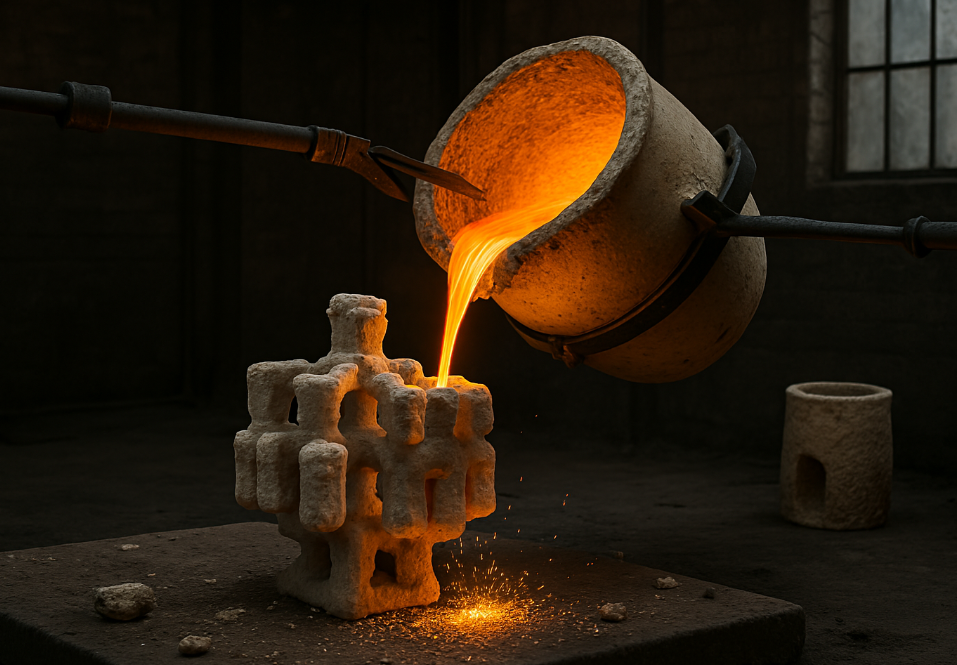
Investment casting
- Features:
- Similar to precision casting, investment casting is a kind of casting method using fusible mold, which is often used to produce castings with complex shape and high precision.
- Mold using fusible materials, such as wax, plastic, etc. , after pouring the mold can be burned.
Applications: mainly used in aerospace, military, automotive and other fields, especially for small batch production of precision castings.
Metal mould casting
- Features:
- Metal mold casting metal molds are used for casting, molds can be reused, suitable for mass production.
- The castings with high precision can be obtained by this process, which is especially suitable for producing thin-walled castings.
Application: mainly used in mechanical industry, automobile, valves, pumps and other fields, suitable for the production of high precision requirements of castings.
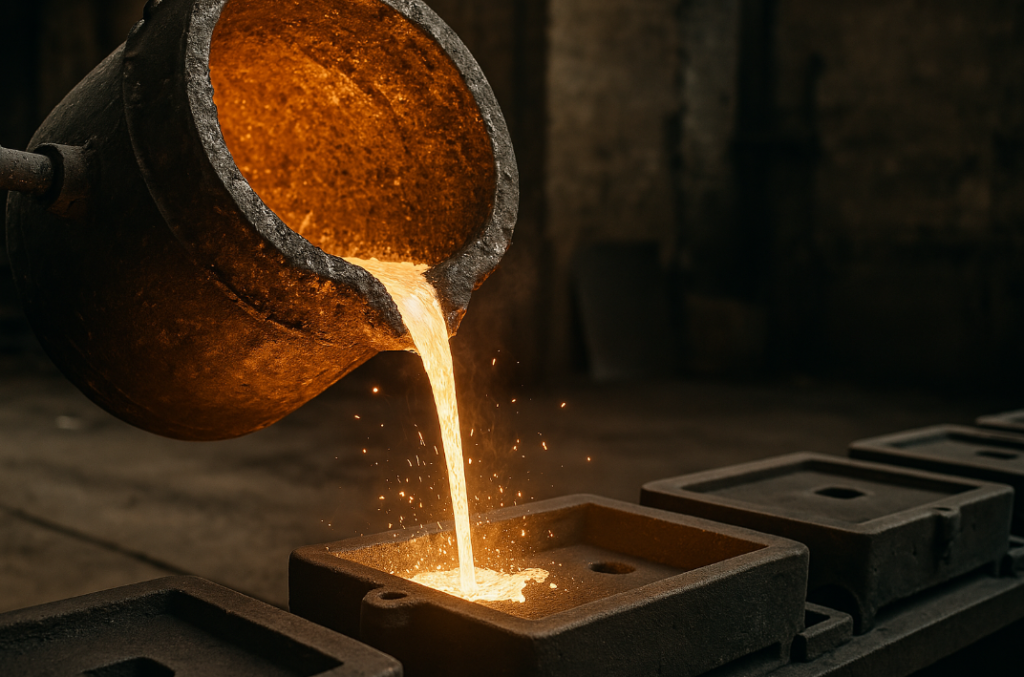
In Summary
These casting processes have their own characteristics and are suitable for different casting types and production requirements. For example, precision casting is suitable for high precision and small batch production, die casting is suitable for mass production lightweight aluminum alloy parts, and sand casting is suitable for the production of complex castings that do not require high precision. By selecting the appropriate casting process, the production efficiency can be improved, the cost can be reduced, and the demand for castings in different fields can be met.
The Process Flow & Duration Estimation
Please note that the final cost depends on the customized service you require, the specifications of the raw materials used, the relevant national laws, and the distance of transportation. Take the example of booking a tall container of products:
Step 1: Design and mould manufacturing
Design products: First of all, according to the needs of the product, casting design. The shape, size, weight and material of the casting should be considered in the design.
Making mold: Mold is an essential tool in the casting process. Make metal or sand mold according to product design. The mold must be able to withstand the heat of the molten metal and reproduce the exact shape of the casting.
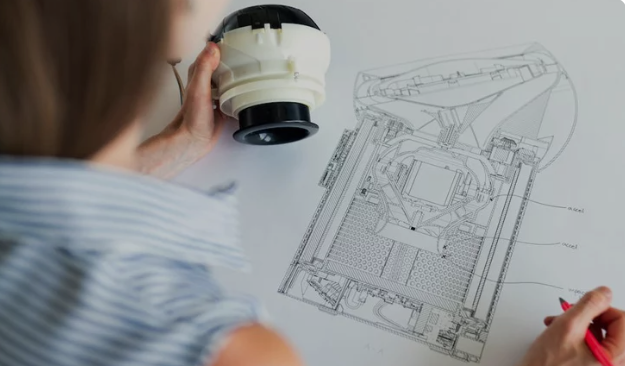
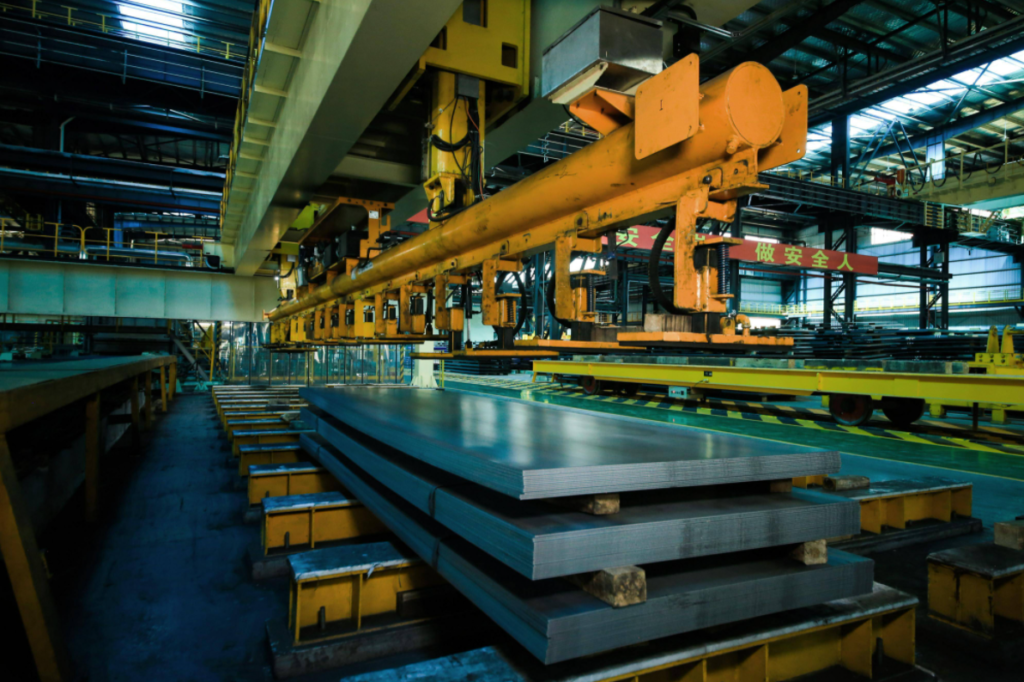
Step 2: Preparation of raw materials
Selection of materials: According to the use of the product needs to select the appropriate casting materials, such as cast iron, aluminum alloy, steel and so on.
Smelt metal: Selected metal materials are heated to a molten state by means of an electric or induction furnace, etc. .
Step 3: Pouring
Pouring molten metal: Pouring molten metal into a mold to fill the cavity in the mold. In this process, the need to maintain the appropriate temperature and pouring speed, to avoid the formation of metal cooling too fast or bubbles.
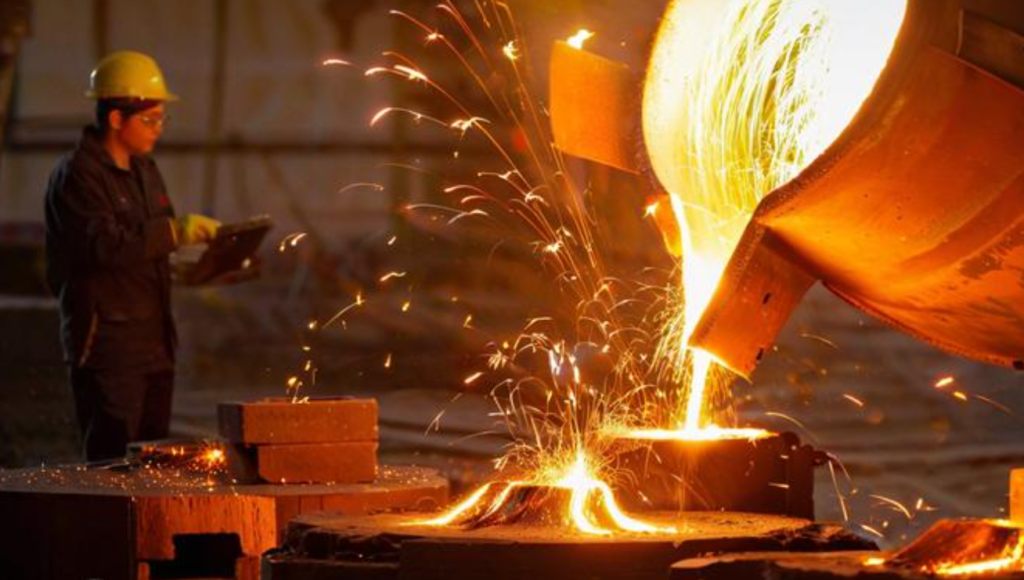
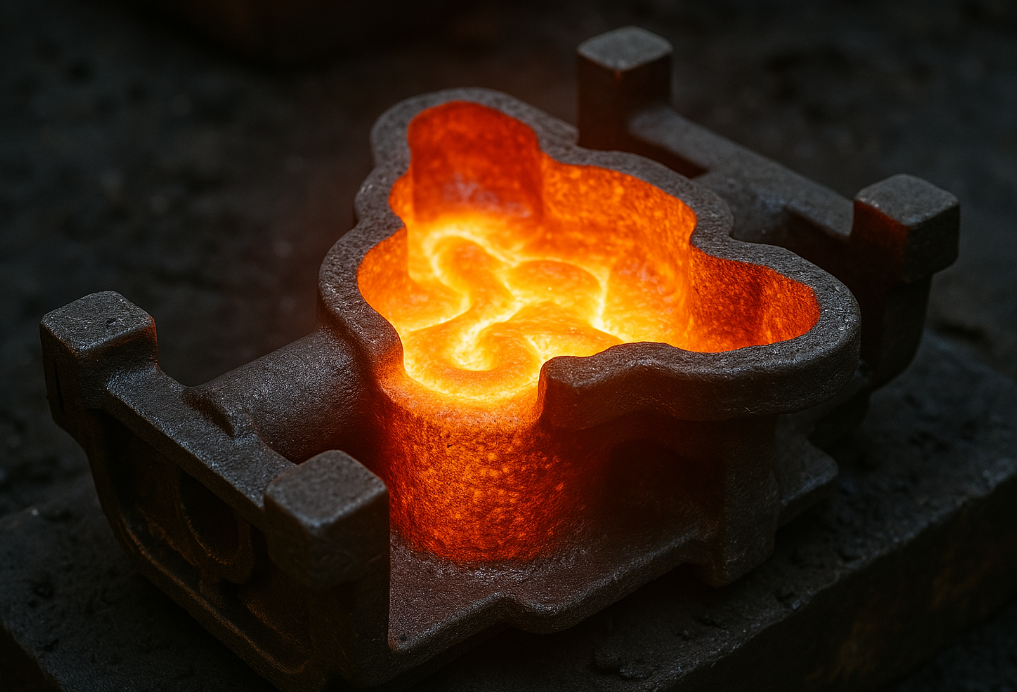
Step 4: Cooling and solidification
Cooling: After pouring, the casting cools and solidifies in the mold. Depending on the size of the casting, the cooling process may take from a few hours to a few days.
Solidification process control: During the cooling process, the crystallization mode of the alloy is controlled to ensure the mechanical properties of the castings.
Step 5: Demoulding and cleaning
Demoulding: The cooled casting needs to be removed from the mold. For sand castings, the mold may be broken and the casting removed, for metal mold castings, mechanical equipment may be required to extract the casting.
Cleaning and deburring: After the casting is removed, there may be excess metal or burrs on the surface, which need to be cleaned by grinding, sandblasting, etc. .
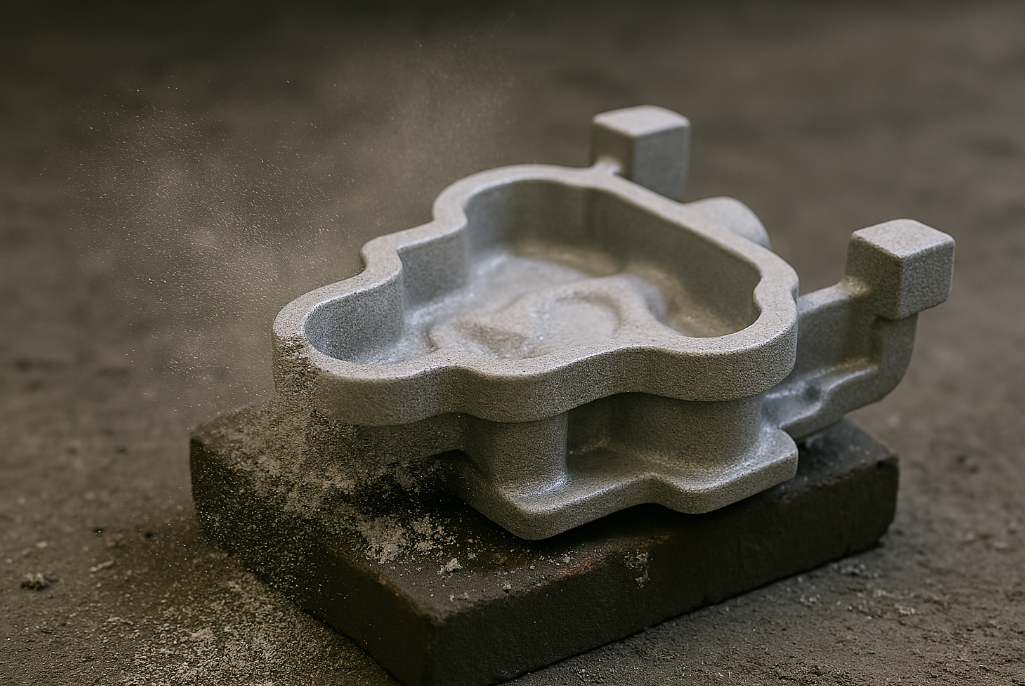
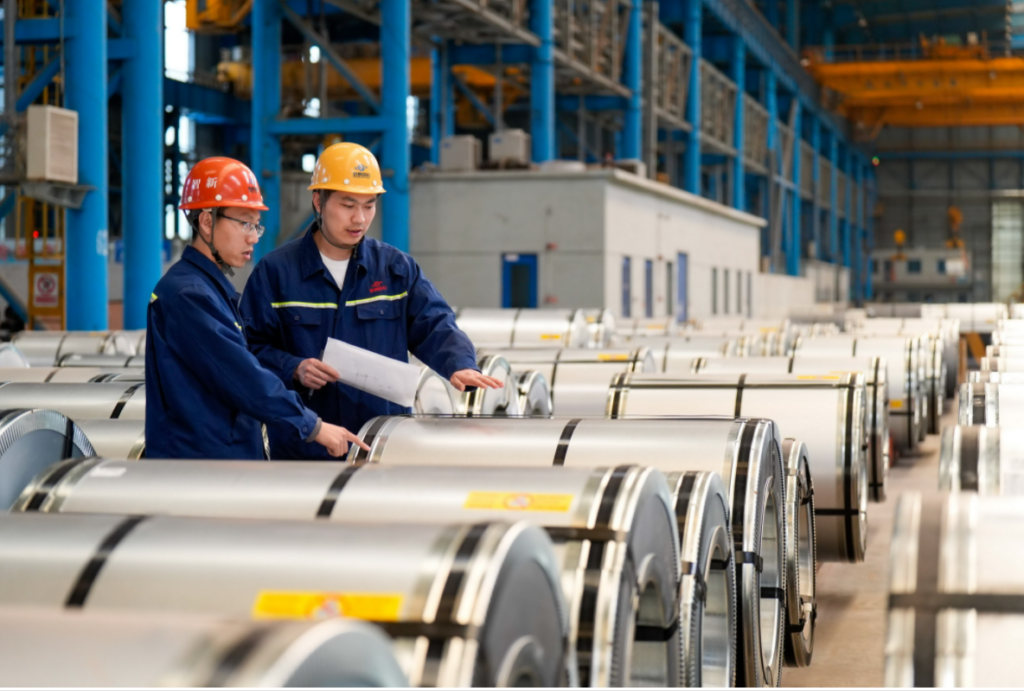
Step 6: Inspection and post-processing
Dimension and quality inspection: Inspect the dimension, surface quality and other properties of castings to ensure that they meet the design requirements.
Post-treatment: The casting may also require heat treatment, spraying, or other processing to improve its mechanical properties or surface finish, as required.
Step 7: Delivery of finished product
Finally, after all the processing and inspection of qualified stampings will be packaged to ensure that the transport process is not damaged. Then according to customer requirements on time delivery.
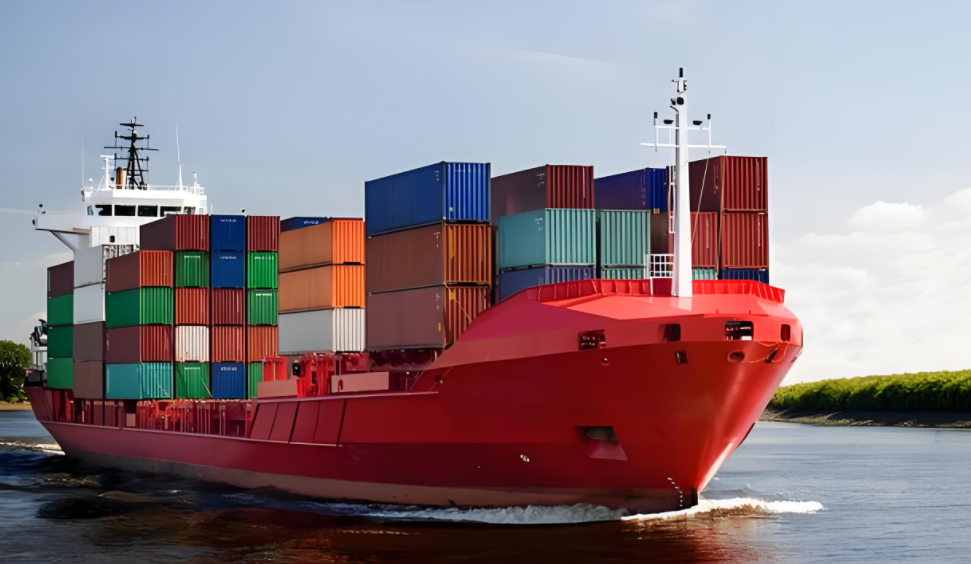
Want to know how to compress lead times?
In order to shorten the production and delivery cycle, we suggest that you tell us your needs in detail, and we will adjust the strategy flexibly according to your requirements to ensure your production and help you succeed!
The Common Pitfalls When Purchasing
Purchasing process, a little careless may fall into the temptation of low prices, quality risks or hidden terms and other common traps.
- Improper selection of materials: Improper selection of materials may lead to castings do not meet the strength, corrosion resistance and other performance requirements, affecting the service life.
- Poor design: Inexperienced design can lead to casting difficulties, increased costs, and delays in delivery.
- Supplier is not reliable: Some unprofessional suppliers may not be strict in quality control, resulting in substandard products or delivery is not timely.
Materials used in casting
It all depends on the type of casting you’re going to do, but these are the materials you’ll most often use when using these casting methods:
Cast iron
Mainly used for the manufacture of wear-resistant, high compressive strength components. Cast iron consists of iron, carbon, silicon, etc. . It is usually used to make machine parts, engine parts, etc. .
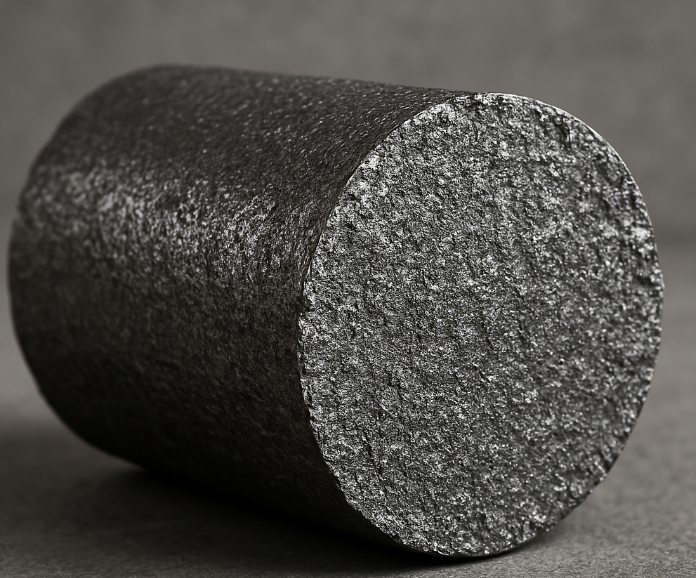
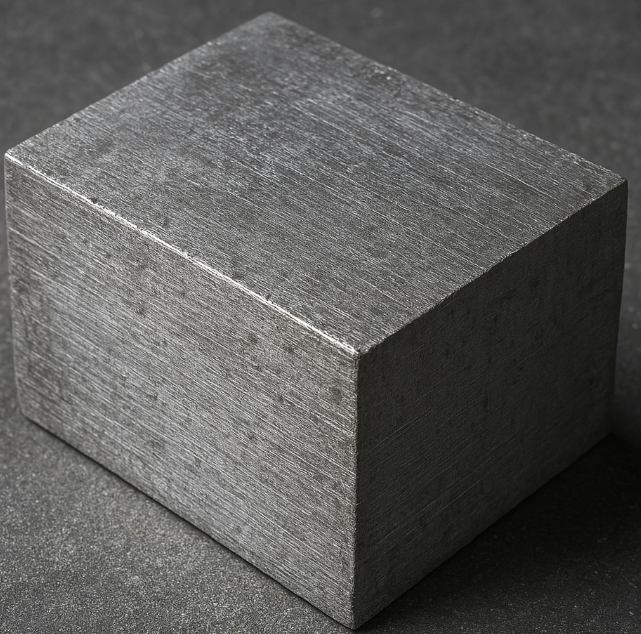
Steel
Suitable for castings with high strength requirement. Steel castings are commonly used in high-impact, high-pressure environments such as construction, shipbuilding, and automotive industries.
Aluminum alloy
Aluminum alloy castings have the advantages of light weight, high strength and corrosion resistance, and are often used in aerospace, automobile manufacturing and other fields.
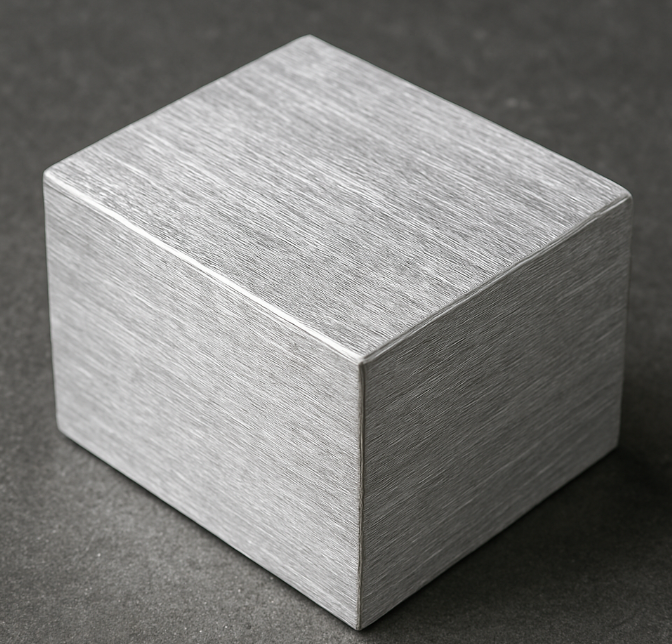
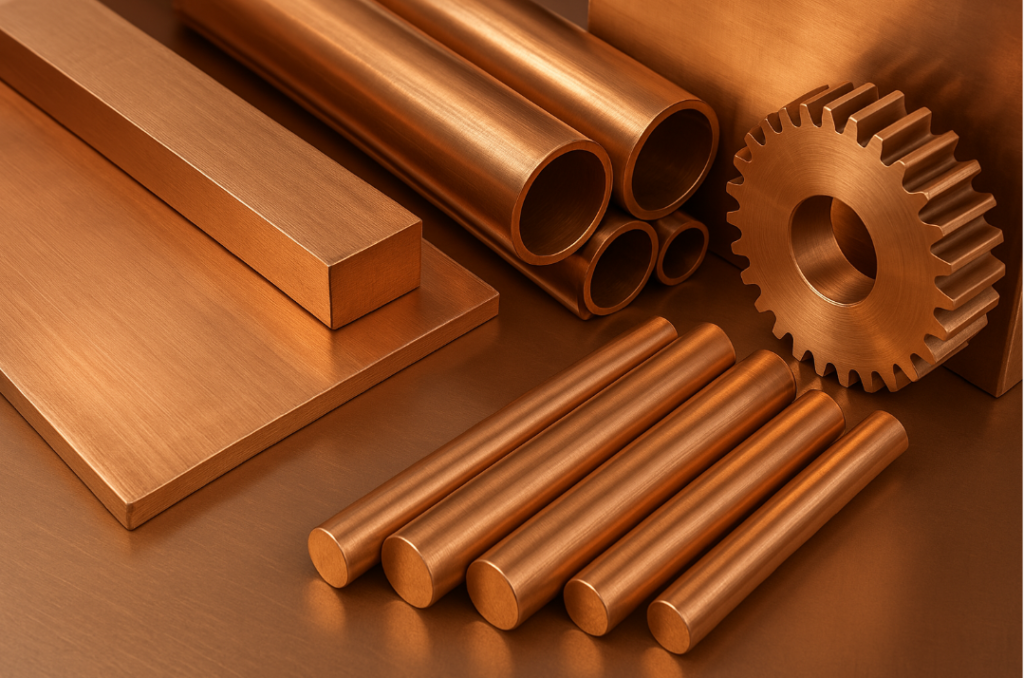
Copper and copper alloys
Copper castings have excellent conductivity and corrosion resistance, suitable for electrical components, precision machinery and decorative casting.
Zinc alloy
Zinc alloy casting materials are suitable for manufacturing precision low pressure castings, often used in automobile, electronics, home appliances and other fields.
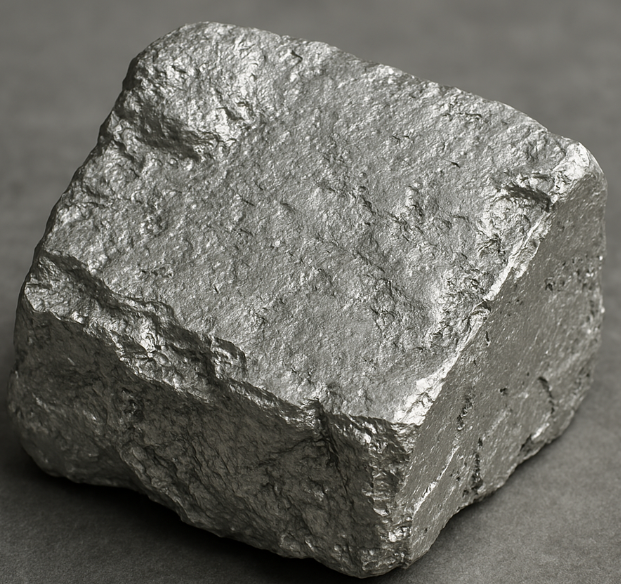
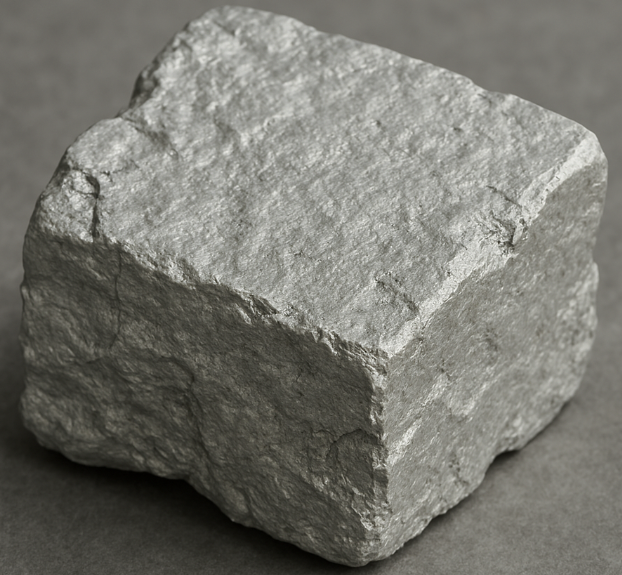
Magnesium alloy
Magnesium alloys are light in weight and high in strength. They are commonly used in aerospace, automotive and electronic equipment to reduce the weight of components.
Sand mould for ceramics
For precision casting, suitable for casting complex shape of small batch production, widely used in aviation, medical, electronics and other fields.
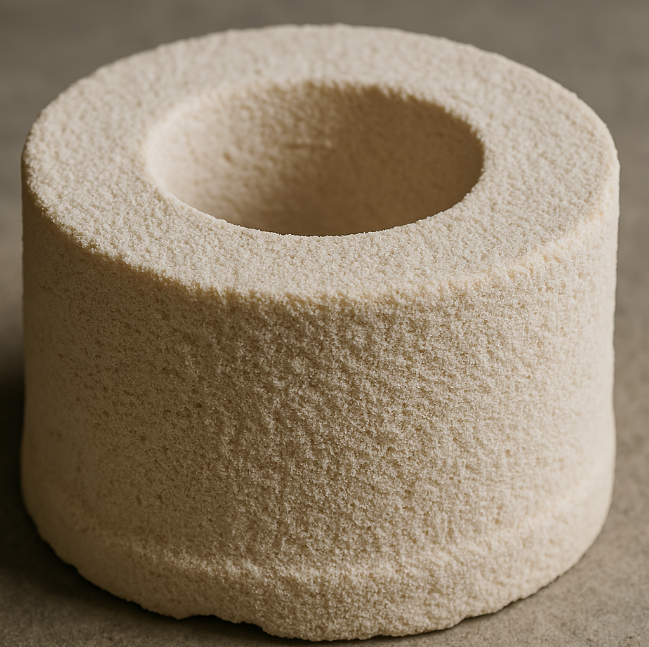
According to the characteristics and application requirements of different casting materials, selecting the appropriate alloy and treatment process can achieve the desired properties.
A Brief Self-Nomination, Why Choose Prime?
Choose Us, you will be cost-effective, high-quality, on-time delivery of metal casting solutions.
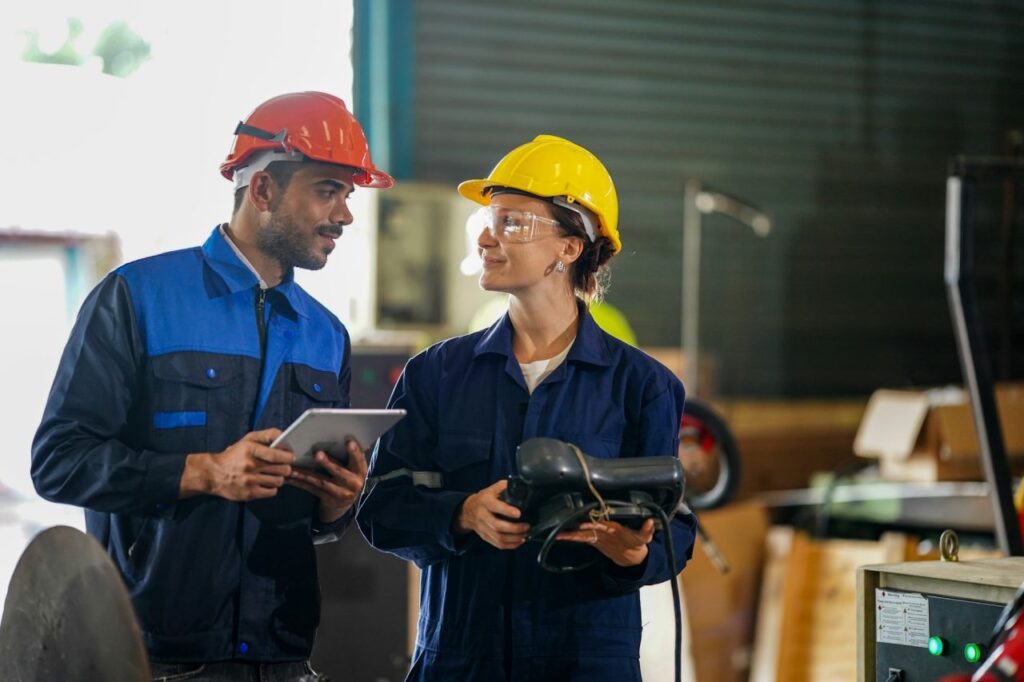
Rich experience: We have more than 30 years of casting production experience, can provide a variety of industries with high-quality custom metal castings.
Professional team: Our team of Engineers is well versed in the casting process and is able to provide precise design and production services.
High quality assurance: WE are ISO 9001 certified to ensure that every casting meets the highest quality standards.
Rapid Response: We are committed to providing fast sample production and production cycle, to ensure that your needs can be met in a timely manner.
Global Services: No Matter where you are, we can provide you with quality services to ensure the smooth progress of your business.
Get in touch
Custom Hardware Parts Made Easy
Share detailed information about your needs, including drawings, reference images, and any specific ideas or specifications you have in mind.
Based on your requirements and design, we’ll provide a custom solution and send you a detailed quote within 24 hours.
Once you approve the design and quote, we’ll begin mass production and take care of the shipping, ensuring timely delivery.
Get a Free Quote
Reach out to us for a free quote and expert advice on your custom hardware needs. At Prime, we’ll provide the right solution for your project, ensuring quality and precision every step of the way.