Prime Custom Plastic Parts
The world’s leading supplier of metal and plastic parts.
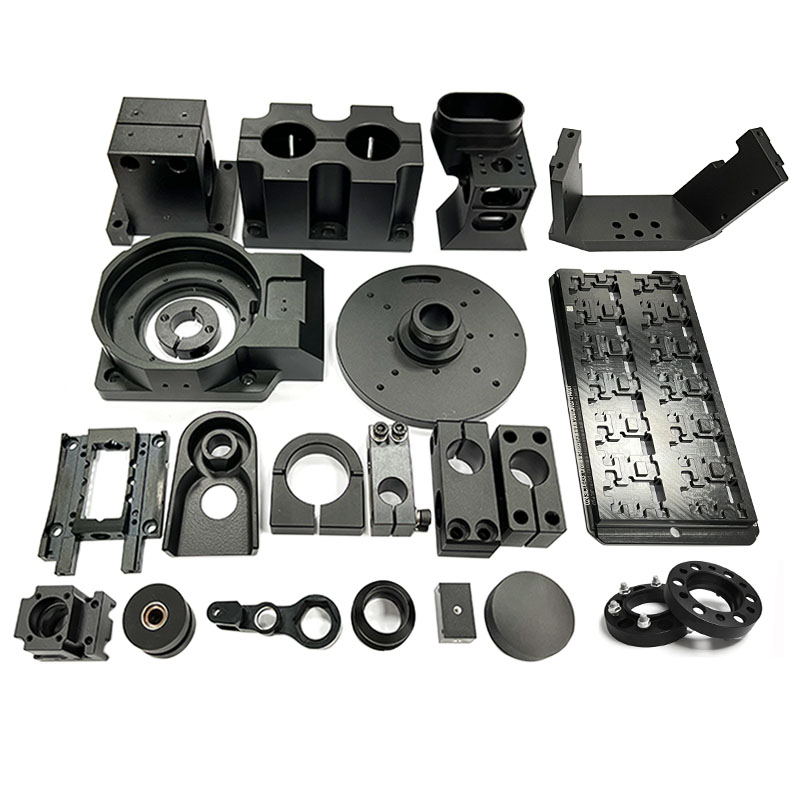
Custom made plastic parts
Custom metal-plastic parts are widely used in many industries, such as automotive, electronics, medical, home appliances, aerospace, industrial equipment and other fields. Due to the good combination of metal and plastic, customized metal-plastic parts play an important role in improving product performance, reducing weight and reducing cost. They can be used in a variety of demanding work environments.
Table Of Contents For This Page
Application fields of customized plastic parts
Here are some real-world examples of how Custom plastic Parts can be used in different industries (automotive, medical, electronics, etc.) and how Prime Custom Parts can address customer pain points.
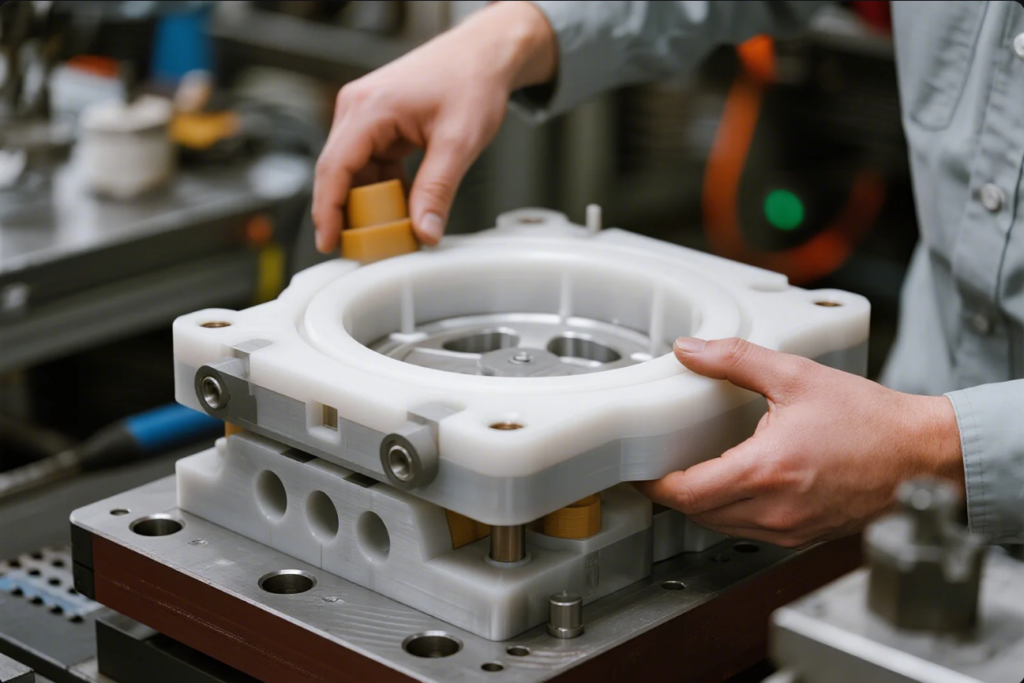
Automotive Industry: Lightweight, Durable Components for Modern Vehicles
A leading automotive manufacturer needed custom-engineered plastic housings for their new electric vehicle platform. Their challenge was to reduce overall vehicle weight while maintaining exceptional durability and heat resistance.
Prime Custom Parts Solution:
We worked closely with their engineering team to select advanced, high-strength polymers and optimized the injection molding process to deliver precision components with tight tolerances. The result: A 20% reduction in part weight, faster assembly times, and components that passed all OEM reliability tests.
Medical Devices: Precision and Biocompatibility in Life-Critical Equipment
A medical device company required complex, biocompatible plastic enclosures for portable diagnostic equipment. Their pain points included strict compliance standards (ISO 13485) and the need for rapid prototyping to accelerate product launch.
Prime Custom Parts Solution:
Our team recommended certified medical-grade plastics and leveraged rapid tooling for fast turnaround. We ensured all parts met cleanroom manufacturing standards and delivered prototypes within two weeks—helping the client bring their device to market ahead of schedule, with full regulatory compliance.
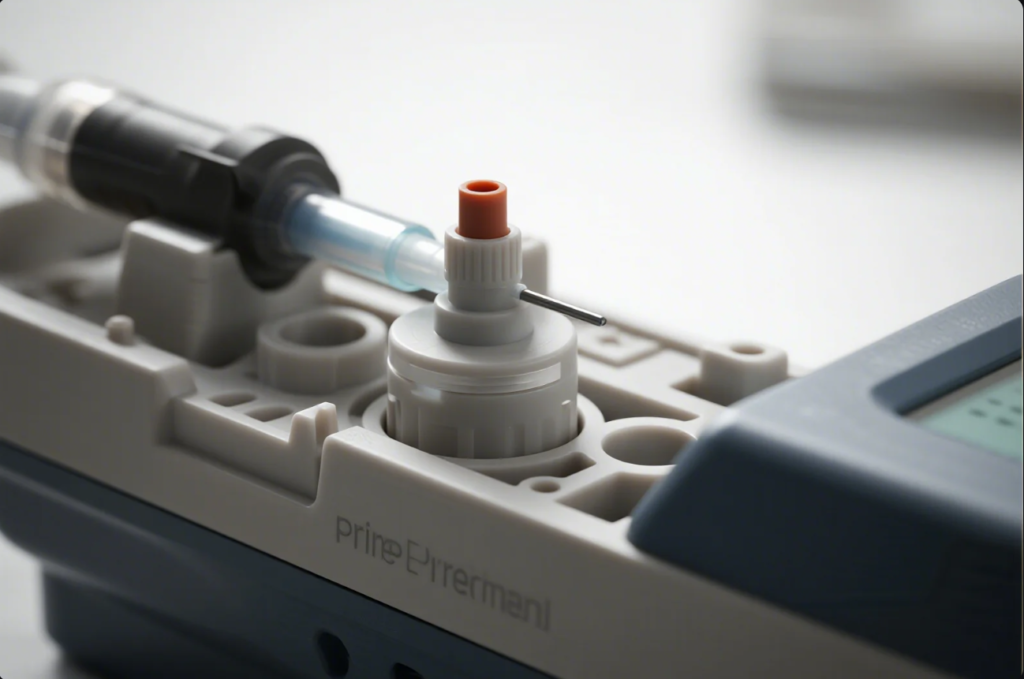
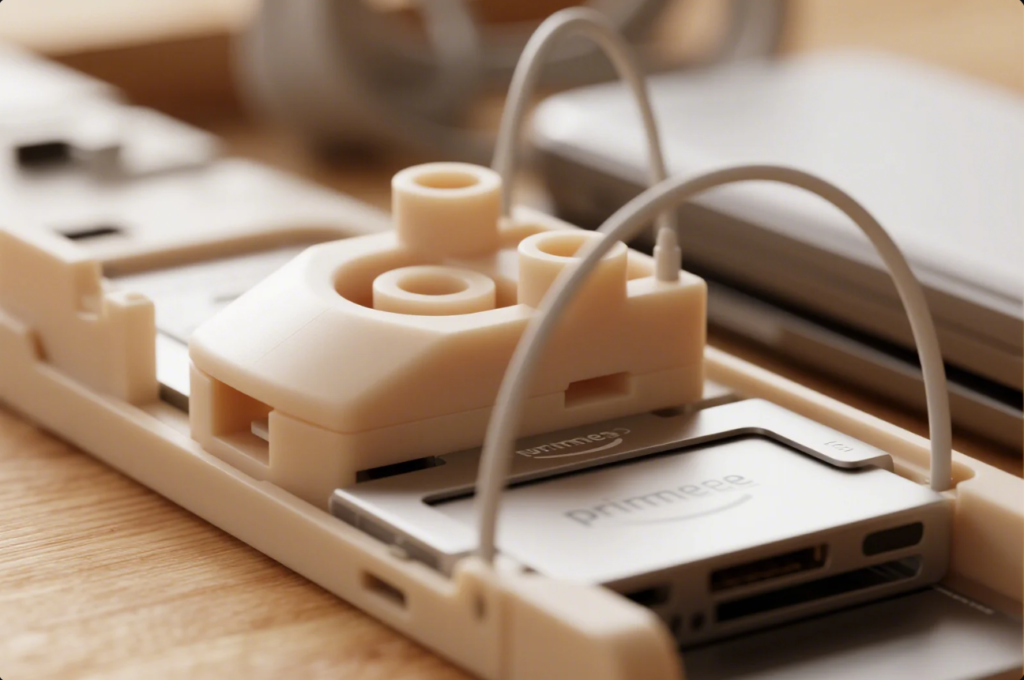
Electronics: High-Performance Plastics for Smart Devices
An electronics OEM was developing a new generation of smart sensors for industrial automation and needed custom plastic enclosures with ESD protection and superior finish. The main challenge: combining complex geometries with EMI shielding requirements.
Prime Custom Parts Solution:
We provided material consulting, recommending conductive plastics, and integrated over-molding technology for EMI shielding. Our precision CNC machining delivered flawless, ready-to-assemble parts that improved the product’s reliability and reduced field failure rates.
Manufacturing process of main plastic parts
Metal-plastic parts can be divided into several main types according to different processes, each process has different characteristics and application fields. The following are some common metal-plastic processes and their characteristics and applications:
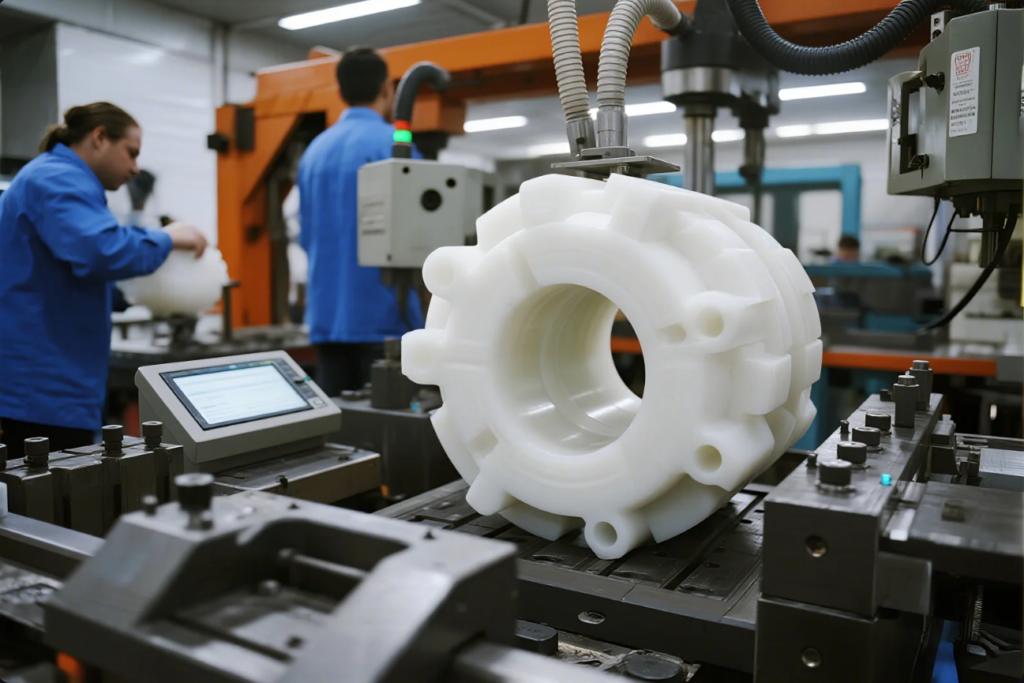
Injection Molding
Features:
Injection molding offers high efficiency, excellent consistency, and is ideal for producing complex, high-precision plastic parts in large volumes. It supports a wide range of materials and is widely used in automotive, electronics, medical, and consumer products. 询问 ChatGPT
Applications:
Injection molding is perfect for mass-producing complex plastic parts with consistent quality. It’s widely used in automotive, electronics, and medical device manufacturing.
Thermoforming
Technical Parameters:
Thermoforming typically uses plastic sheets heated to 100–200°C, then shaped over molds using vacuum or pressure, allowing for wall thicknesses from 0.25 mm to over 8 mm. It is compatible with a wide range of thermoplastics such as ABS, PET, and polycarbonate for both small and large parts.
Advantages:
Thermoforming offers fast prototyping and lower tooling costs compared to injection molding, making it ideal for moderate production runs. It enables the creation of lightweight, durable, and large-sized components with complex shapes and fine details.
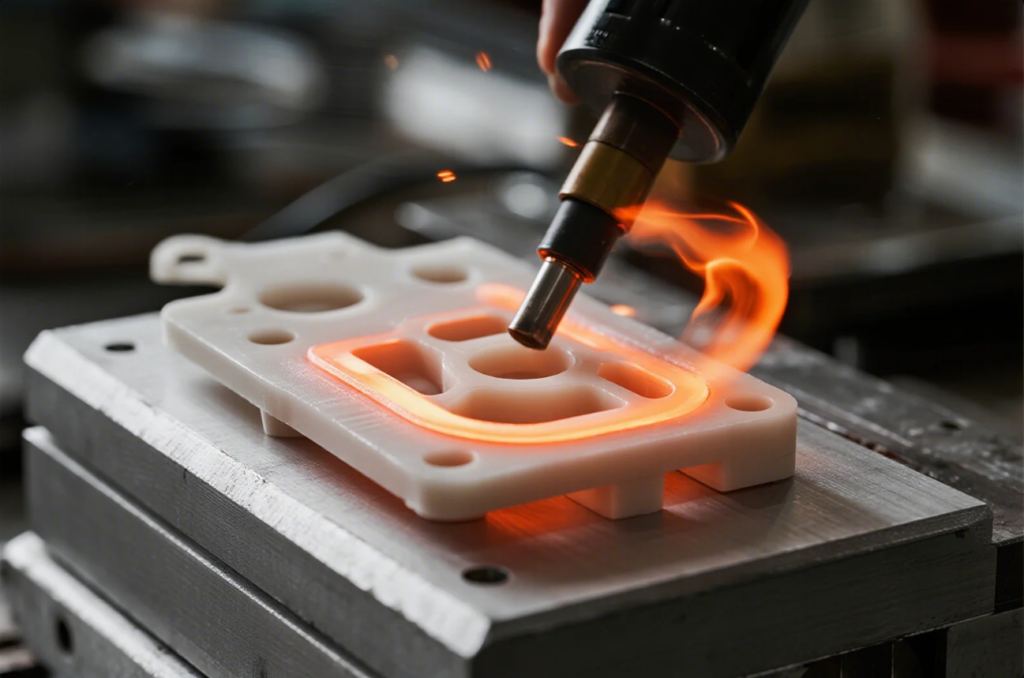
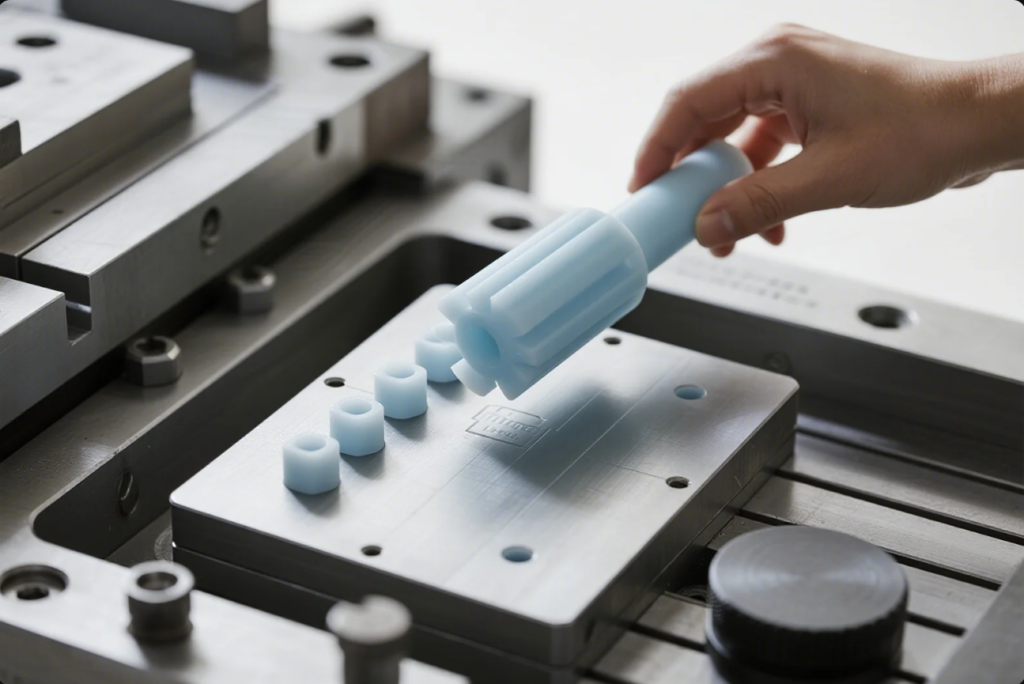
Extrusion Molding
Technical Parameters:
Extrusion molding applies high pressure to force heated plastic or metal material through a shaped die, enabling continuous production of profiles with complex cross-sections. The process supports a wide range of thermoplastics, thermosets, and aluminum alloys, with output rates and tolerances determined by material type and die design.
Advantages:
Extrusion molding delivers high efficiency, low material waste, and is ideal for producing long, uniform parts with consistent cross-sections. It offers great flexibility for customizing shapes and can integrate additional features such as grooves or internal cavities.
Metal Injection Molding (MIM)
Technical parameters:
Metal Injection Molding (MIM) combines Powder metallurgy and injection molding techniques and is suitable for complex three-dimensional shapes, high precision and mass production with typical tolerances up to ± 0.3% . The process can handle iron-based, titanium alloy, stainless steel and other metal materials, commonly used in the wall thickness of 0.5 mm, the density of more than 97% of precision parts manufacturing.
Scenario:
Metal Injection Molding (MIM) is widely used in the manufacture of high-precision small structural parts in automobile, medical equipment, electronic products and aerospace industries. It is especially suitable for producing metal parts with complex shape, large batch and high requirement for mechanical properties.
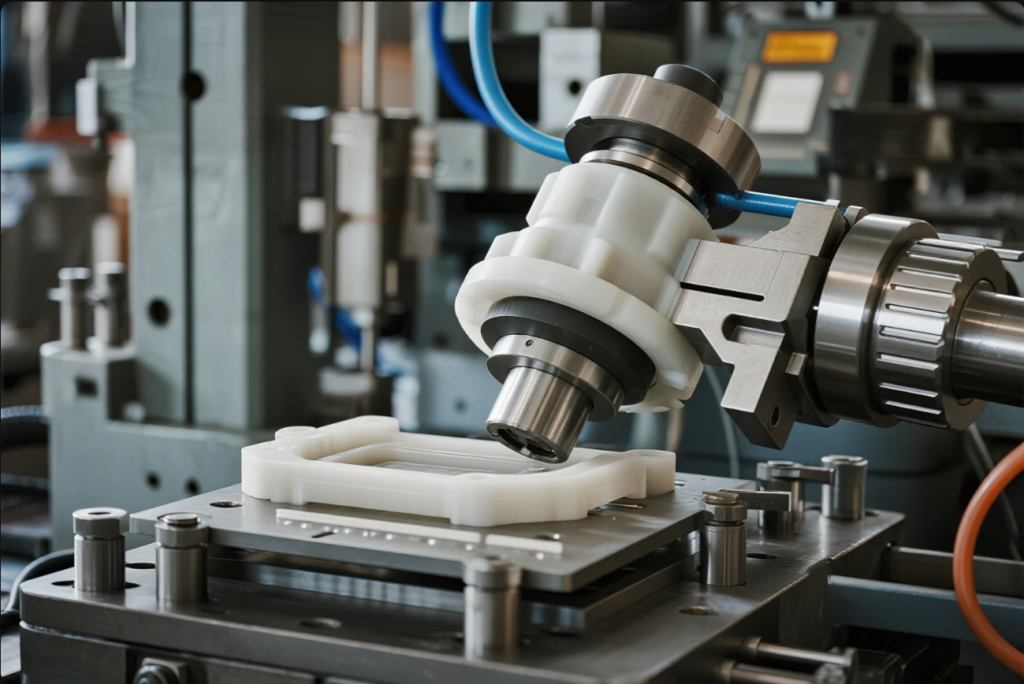
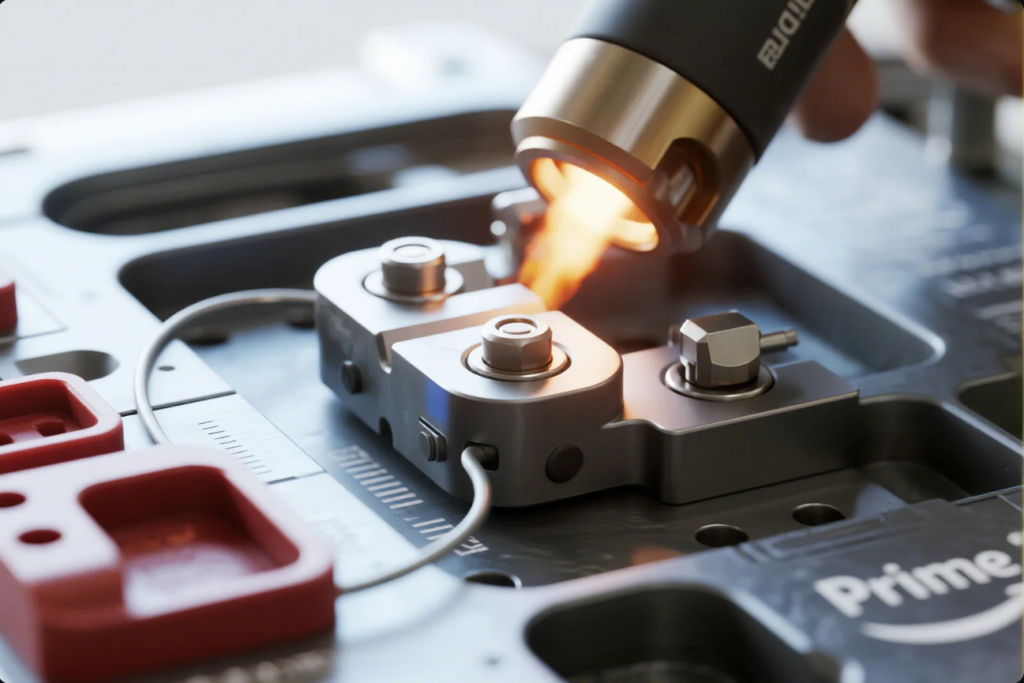
Thermal Riveting
Technical Parameters:
Hot riveting typically operates at temperatures ranging from 150°C to 350°C, using controlled pressure and dwell time to securely deform and fasten thermoplastic or metal rivets. The process offers high repeatability and is suitable for a variety of part geometries and joint strengths.
Application Scenarios:
Hot riveting is widely used in automotive components, electronic housings, and household appliances for creating strong, permanent joints without adhesives or screws. It is especially suitable for mass production environments requiring rapid, automated assembly of plastic and metal parts.
Ultrasonic Welding
Ultrasonic Welding Technical Parameters:
Ultrasonic welding operates at frequencies typically between 20 kHz and 40 kHz, using high-frequency vibrations to generate localized heat and bond thermoplastics or metals without the need for adhesives or additional heat sources. Key parameters include amplitude, welding time, pressure, and energy, which are precisely controlled to ensure strong, clean welds with minimal material deformation.
Ultrasonic Welding Application Scenarios:
It is widely used for joining plastic parts in the automotive, electronics, and medical device industries, such as bonding housings, filters, and electrical connectors. Ultrasonic welding is also ideal for applications requiring clean, particle-free joints and fast, repeatable production cycles.
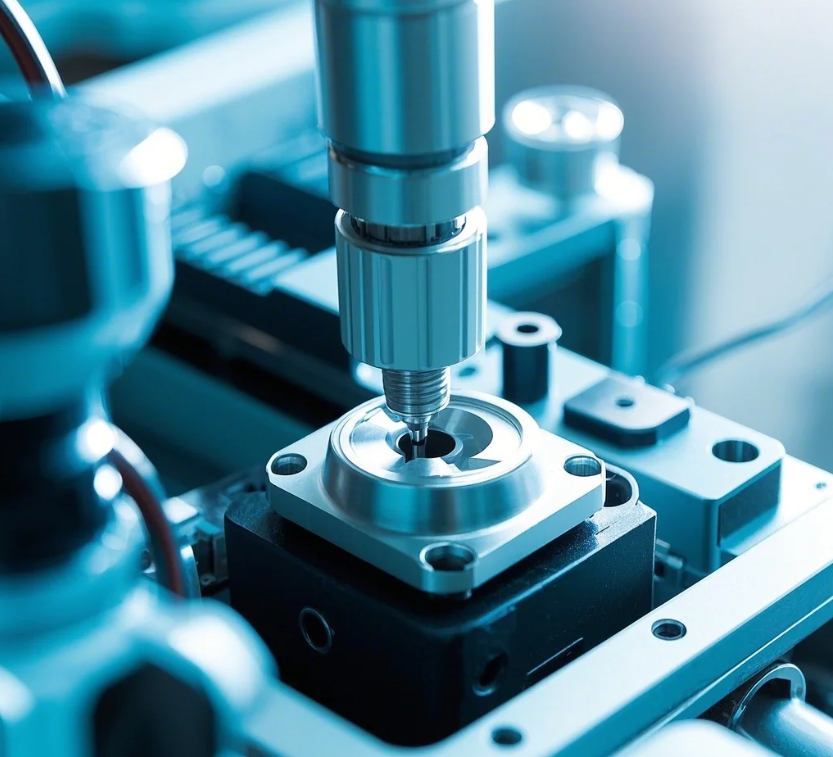
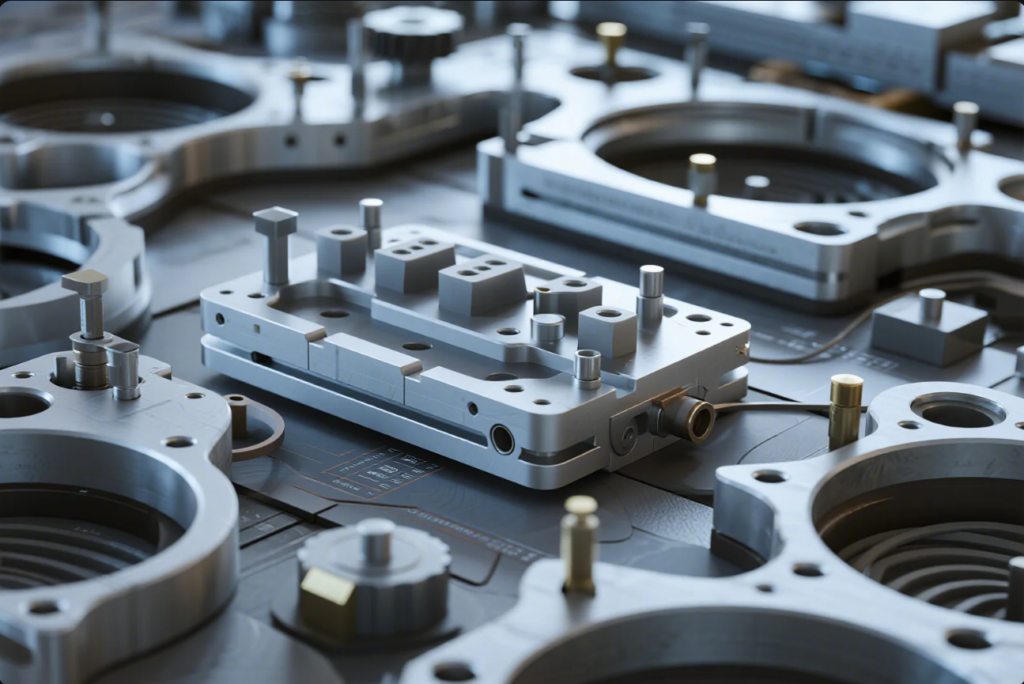
Compression Molding
Technical Parameters:
Compression molding involves placing preheated plastic material into a heated mold cavity, then applying pressure (typically 5–50 MPa) and temperature (usually 120–200°C) to shape and cure the part. Key parameters include mold temperature, compression pressure, dwell time, and material viscosity, all of which affect the part’s dimensional accuracy and mechanical properties.
Application Scenarios:
This process is commonly used for producing large, complex, or high-strength plastic components such as automotive bumpers, electrical housings, and appliance panels. It is especially suitable for thermosetting plastics and composite materials that require precise molding and superior structural integrity.
These metal-plastic processes have different characteristics and application fields. Selecting the appropriate process can not only meet the design requirements, but also effectively control the cost and improve the performance and quality of the products. In the actual production, according to the demand and industry standards to select the appropriate process is crucial.
The Process Flow & Duration Estimation
Please note that the final cost depends on the customized service you require, the specifications of the raw materials used, the relevant national laws, and the distance of transportation. Take the example of booking a tall container of products:
Step 1: Design and development
- Customer requirement analysis: According to customer requirement, designer and engineering team analyze and confirm the specification, function and material requirement of parts.
- 3D modeling and design optimization: Use CAD (computer-aided design software) to build 3D models of parts to ensure that the design meets engineering requirements and make necessary design optimizations.
- Sample confirmation and modification: After the design is completed, the prototype sample is usually made for verification to ensure that the design meets the actual use requirements. Make necessary adjustments based on feedback.
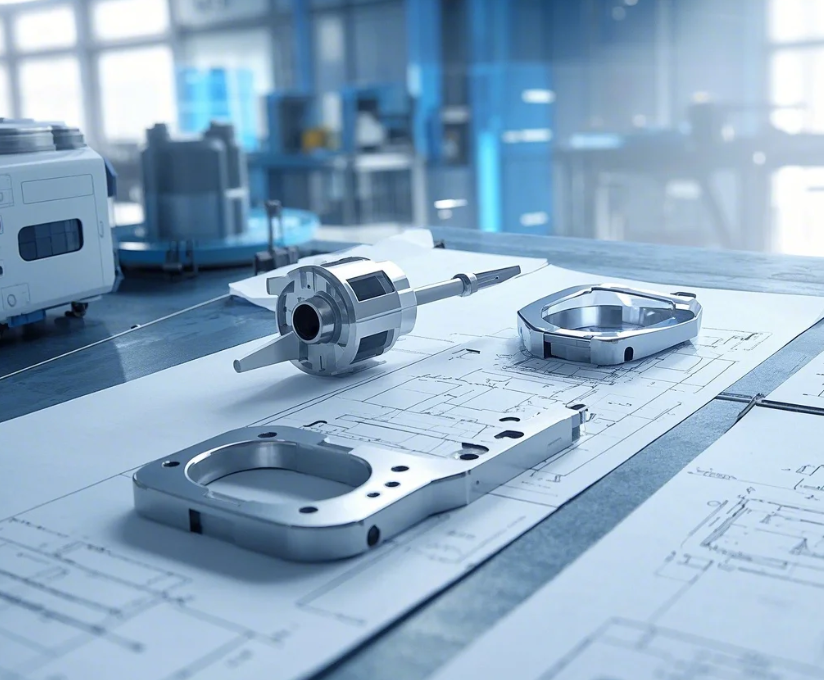
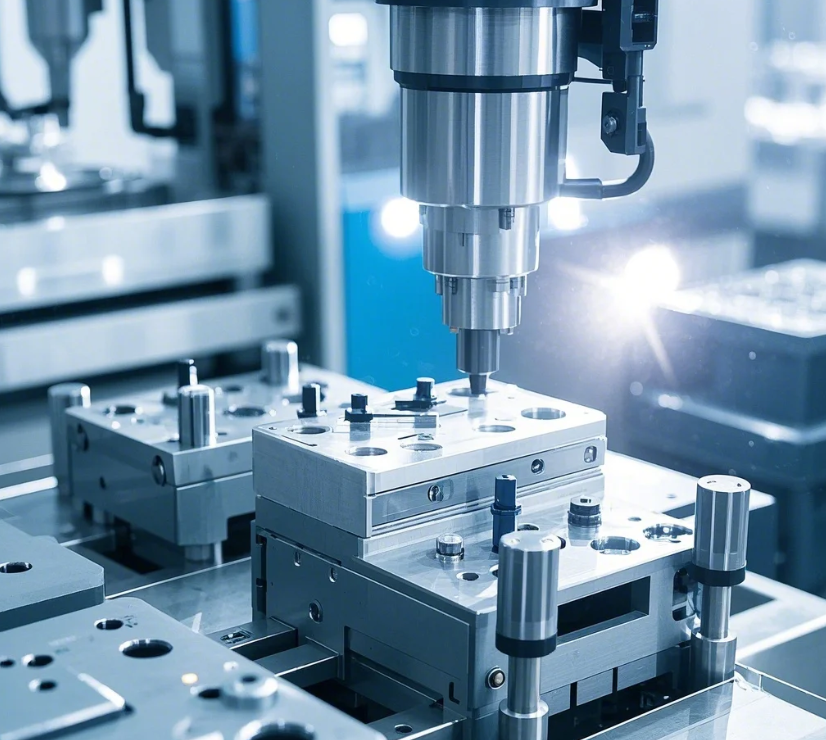
Step 2: Design and manufacture of die and mould
- Mold design: According to the complexity of the parts, design the appropriate mold. For metal-plastic composite parts, the combination of metal part and plastic part should be taken into account in mold design.
- Mold Manufacturing: Mold manufacturing is a key step in the production process, usually using high precision machining technology (such as CNC machining, Electrical discharge machining) to manufacture the mold.
- Die testing and optimization: After the completion of the manufacturing die testing, testing the working effect of the die, and according to the need to optimize the adjustment.
Step 3: Raw material preparation
- Material selection: According to the functional requirements of parts, select the appropriate metal materials, such as stainless steel, aluminum alloy or other alloy metal.
- Plastic material selection: Choose suitable plastic materials, such as ABS, polycarbonate (PC) , nylon, etc. , taking into account the heat resistance, corrosion resistance, strength and other needs.
- Material preparation and inspection: Purchase and inspect the quality of materials to ensure that they meet production standards and design requirements.
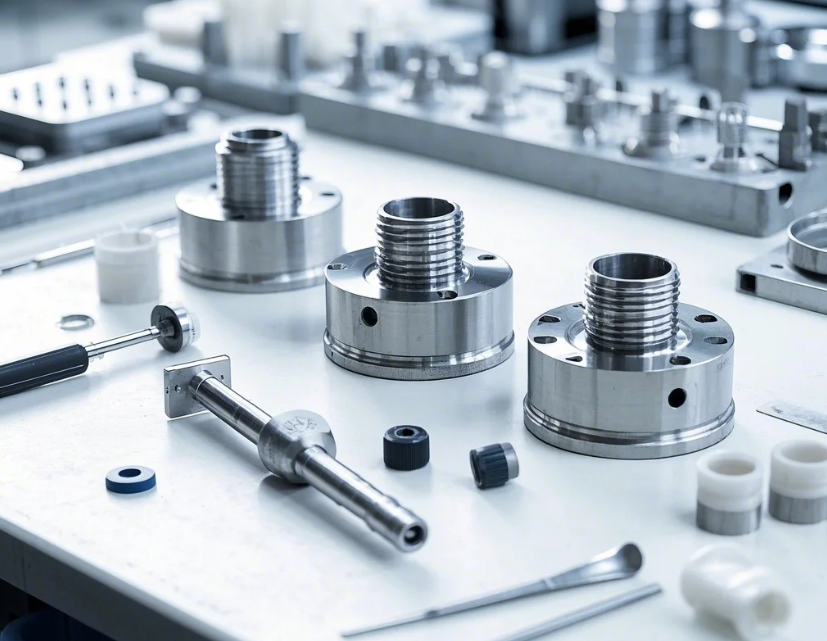
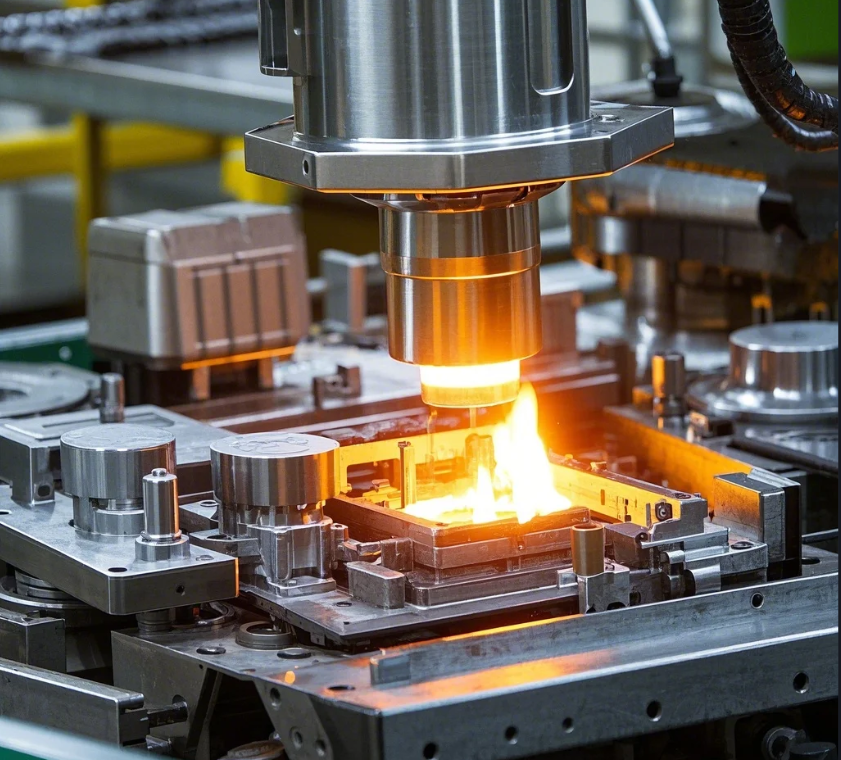
Step 4: Implementation of production process
- Metalworking: Metal parts are usually shaped by turning, milling, stamping or casting to ensure dimensional accuracy and surface quality.
- Plastic Processing: Plastic parts through injection molding, extrusion molding, hot pressing and other processes. The combination of metal and plastic can be achieved by compression molding, metal injection molding and other processes.
- Synthesis and assembly: Metal and plastic parts are connected, fixed or embedded in a specific process to form a complete metal-plastic composite part.
Step 5: Surface treatment:
- Metal surface treatment: According to the requirements of galvanized, spraying, painting, electroplating and other surface treatment, enhance metal corrosion resistance, oxidation resistance and aesthetics.
- Plastic Finish: Plastic parts may need to be painted, printed, or UV coated to improve appearance or durability.
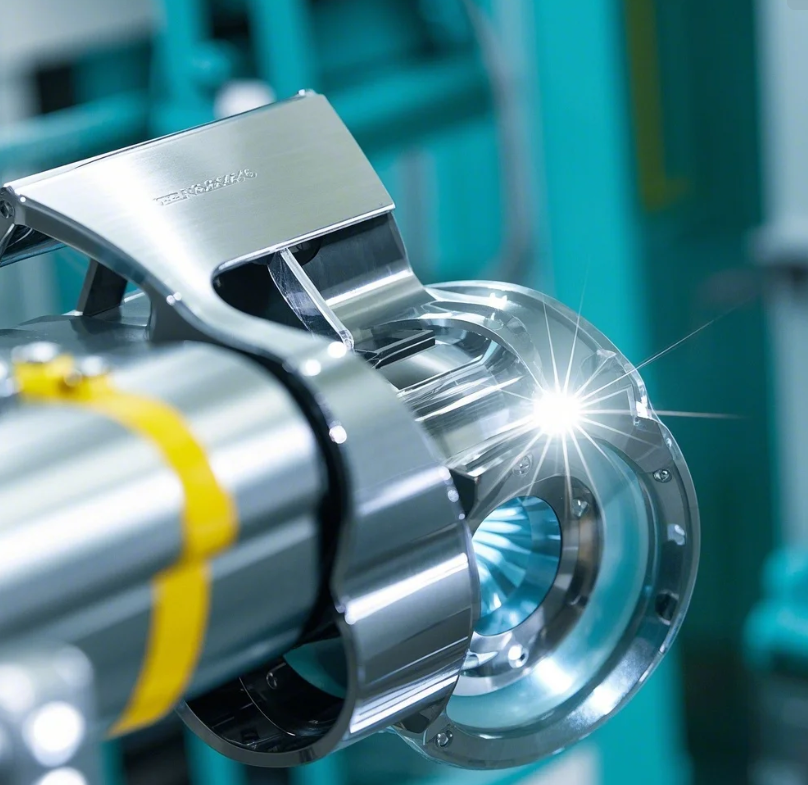
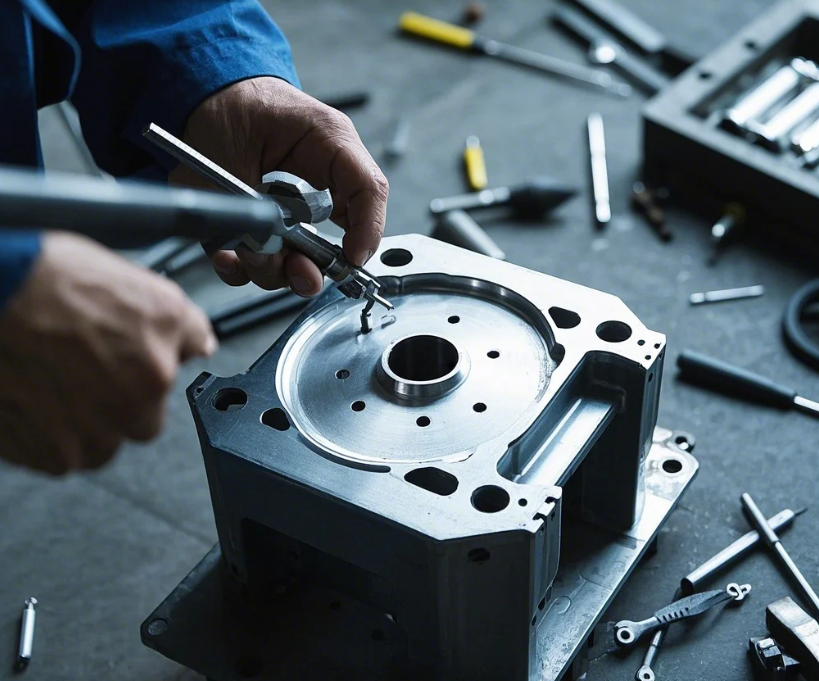
Step 6: Quality Control and inspection
- Dimensional inspection: use high-precision measuring tools (such as calipers, coordinate measuring machines, etc.) to inspect the dimensions and tolerances of the parts to ensure consistency with the design.
- Performance test: carry out strength, corrosion resistance, high temperature resistance and other performance tests to ensure that its performance in the actual working environment meets the requirements.
- Conformity inspection: perform final conformity inspection after all tests are completed to ensure that parts meet production standards and customer requirements.
Step 7: Packaging and delivery
- Parts packaging: According to the characteristics of the product, the use of appropriate packaging materials, such as shockproof packaging, plastic bags, cartons, etc. , to ensure that the parts are not damaged during transportation.
- Delivery and logistics: Arrange the appropriate transportation mode, ensure the delivery of products to customers on time, and provide the necessary transportation tracking services.
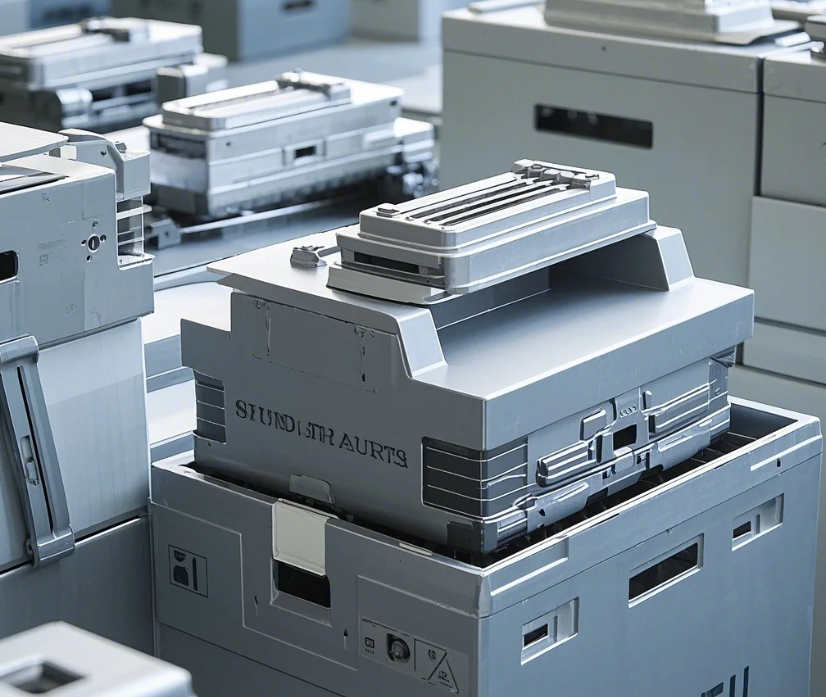
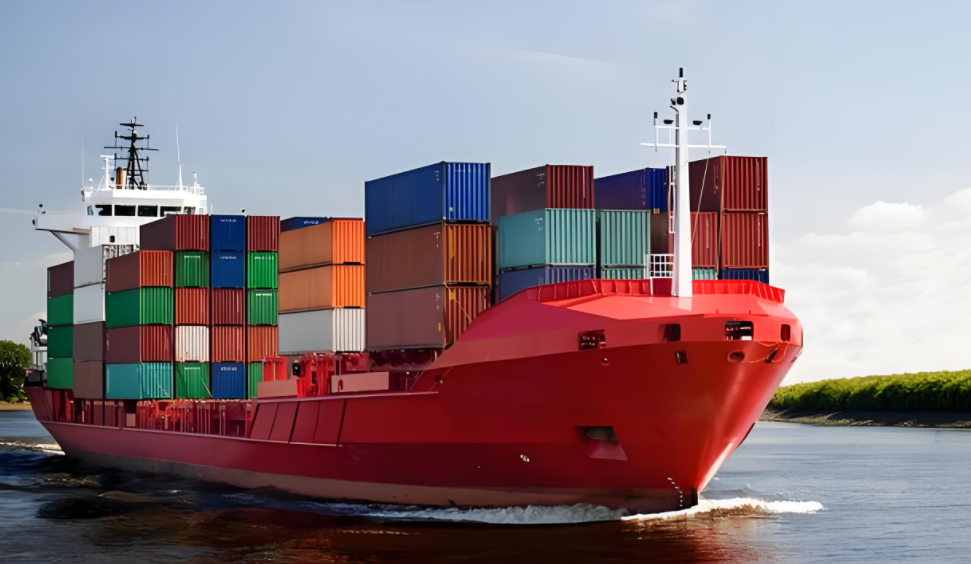
Step 8: Delivery of finished product
Upon completion of all inspection and post-processing, the castings will become the final product, ready to be delivered to the customer or used for assembly.
Ready to take your project to the next level?
Contact us today to discuss your manufacturing needs or request a free quote tailored to your specifications.
The Common Pitfalls When Purchasing
Please note that the final cost depends on the customized service you require, the specifications of the raw materials used, the relevant national laws, and the distance of transportation. Take the example of booking a tall container of products:
- Improper material selection: improper material selection may lead to plastic parts can not reach the strength, corrosion resistance and other performance requirements, affecting the service life.
- Poor design: premature design can lead to difficulties in the production of plastic parts, increased costs and delays in delivery.
- Unreliable suppliers: some unprofessional suppliers may not be strict in quality control, resulting in nonconforming products or untimely delivery.
Common materials for custom plastic parts
Metal fasteners generally use the following materials:
Metal materials
- Stainless steel: with good corrosion resistance, suitable for demanding high durability and corrosion resistance of the parts.
- Aluminum alloy: light and corrosion-resistant, commonly used in the requirements of lighter metal parts, especially in aviation, automotive fields.
- Copper Alloy: with excellent electrical and thermal conductivity, commonly used in electrical and electronic products of the metal part.
- Ferroalloy: such as cast iron, carbon steel, etc. , high strength, commonly used in high-strength components.
- Galvanized Steel: surface galvanized to increase corrosion resistance, widely used in the construction and automotive industries.
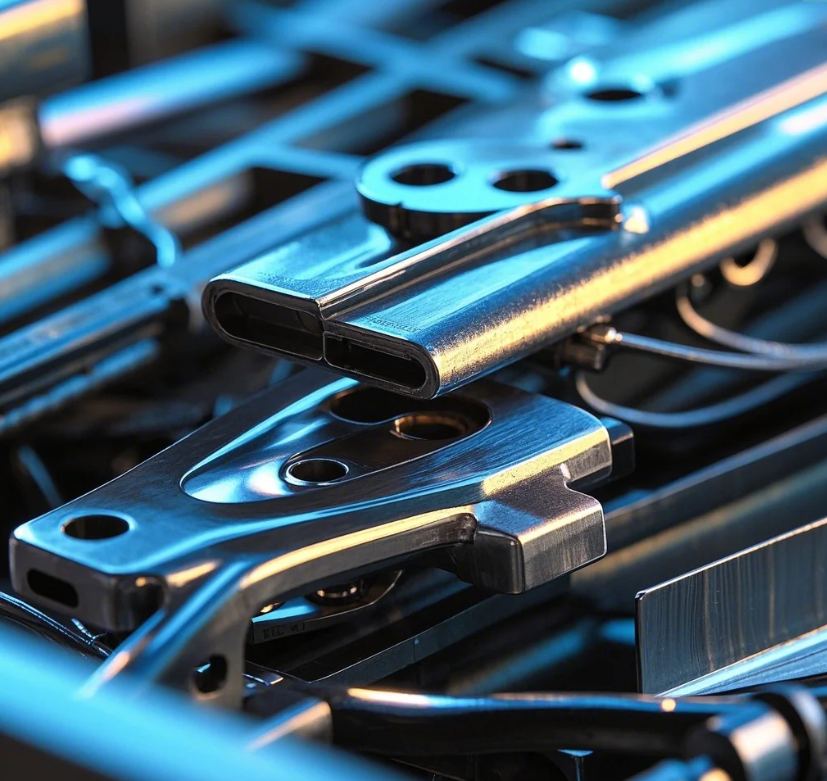
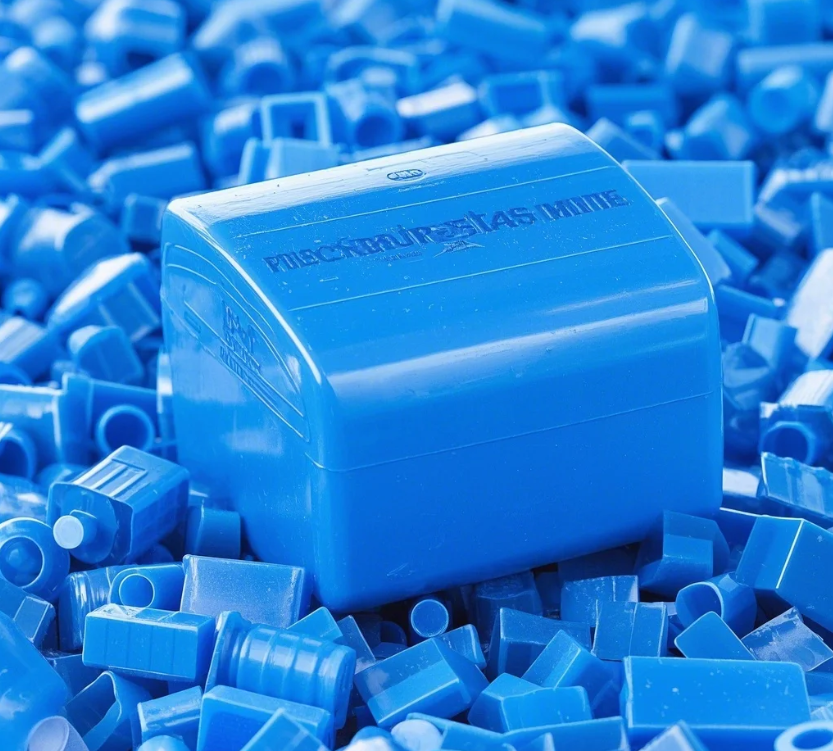
Plastic materials
- Polyethylene (PE) : widely used in low-cost products, has good chemical resistance.
- Polypropylene (PP) : tough and corrosion resistant, suitable for plastic parts in automobiles and home appliances.
- Polyvinyl chloride (PVC) : commonly used in pipes, window frames and other structural parts, good weather resistance.
- Polycarbonate (PC) : has good impact resistance and transparency, commonly used in electronic products shell.
- Nylon (PA) : high strength, wear resistance, widely used in mechanical parts.
Composite materials
Plastic composites: combine the advantages of metal and plastic. For example, metal-based plastic composites are used to enhance the strength and durability of plastic parts.
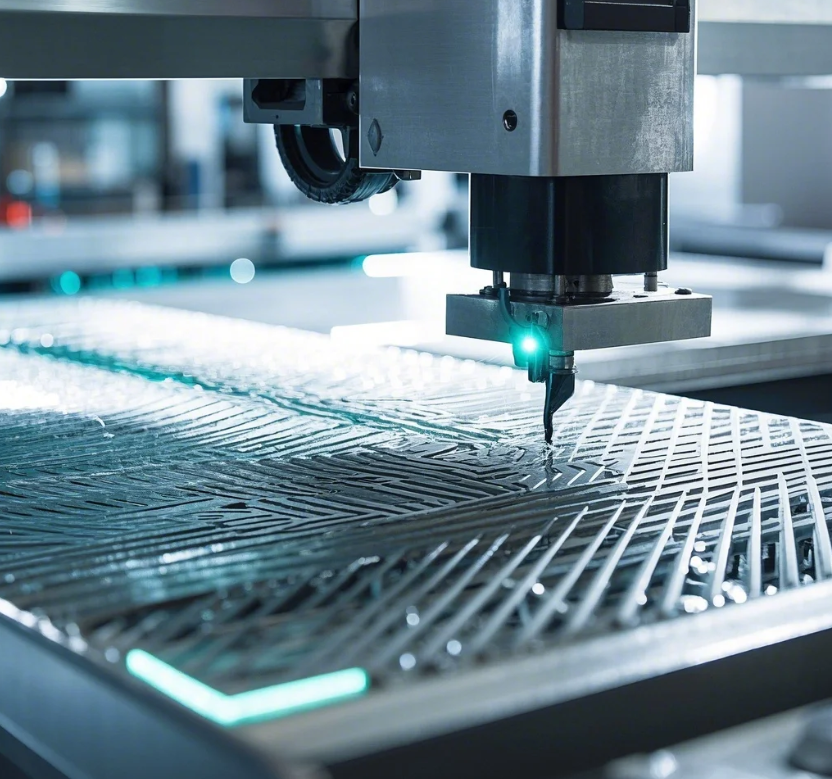
Not sure which material is right for your application?
Our engineering team is here to help. Contact the experts immediately!
Industry trends in custom plastic parts
The Future of Plastic Parts Manufacturing
The plastics manufacturing industry is rapidly embracing sustainable materials, such as bioplastics and recycled polymers, to reduce environmental impact and meet global eco-standards. At the same time, smart manufacturing and automation—powered by advanced robotics, IoT, and data analytics—are driving greater efficiency, precision, and flexibility across production lines.
By integrating these cutting-edge trends, our company is committed to delivering high-quality, environmentally responsible plastic components while leading the way in intelligent, automated manufacturing solutions for the future.
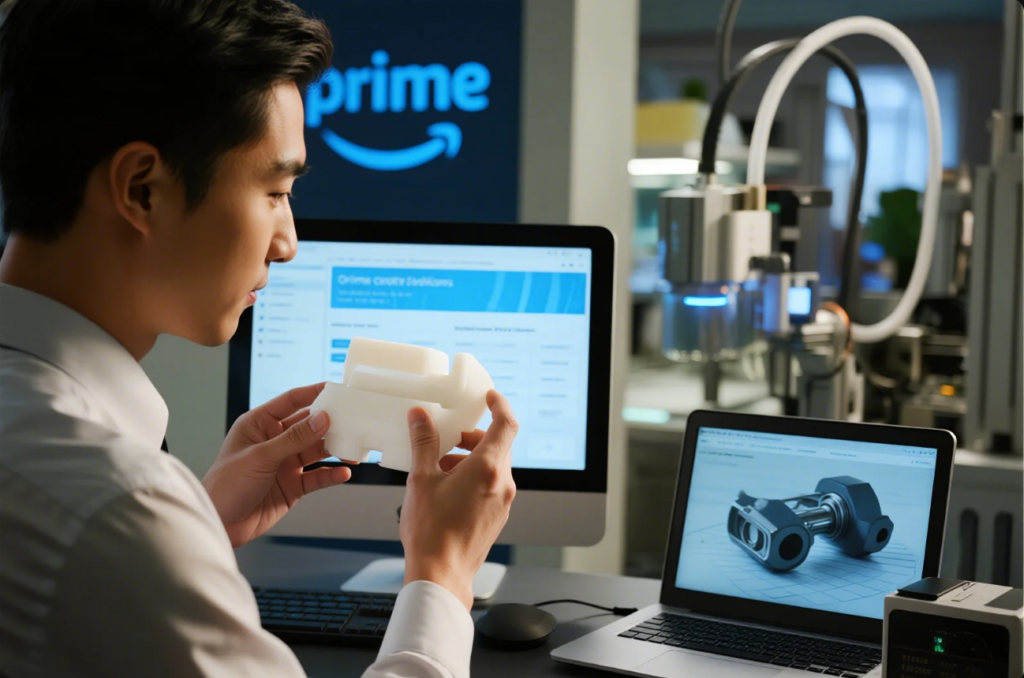
A Brief Self-Nomination, Why Choose Prime?
Choose Us, you will get reasonable prices, high quality, on time delivery of plastic parts solutions.
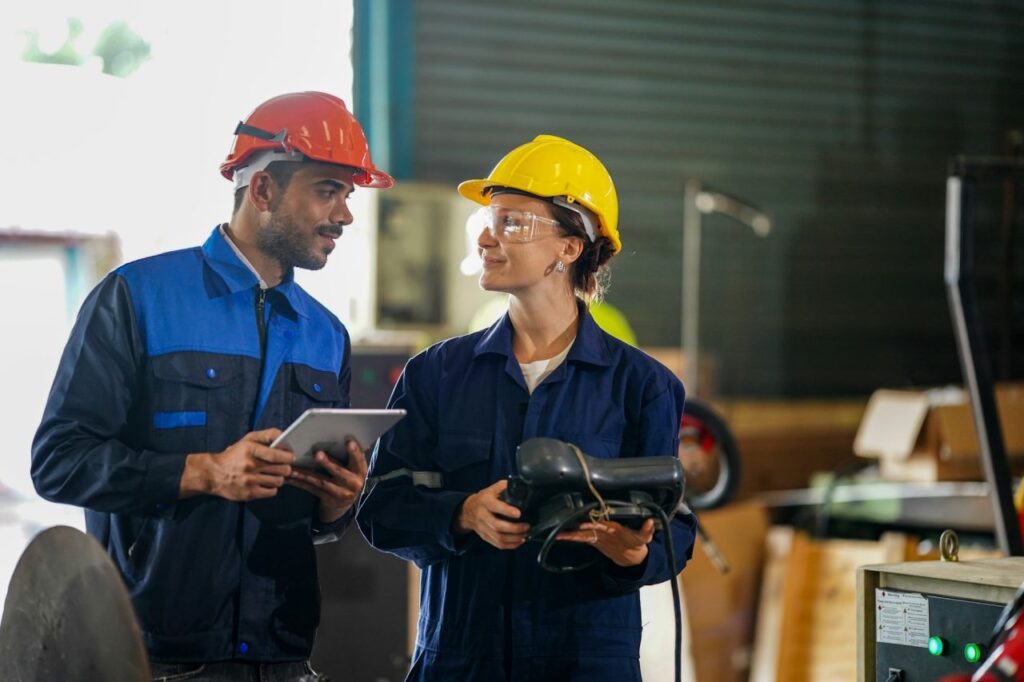
Experience: we have more than 30 years of plastic parts production experience, can provide high-quality custom metal plastic parts for the industry.
Professional team: Our engineering team is familiar with plastic parts technology and can provide accurate design and production services.
Quality assurance: We are ISO 9001 certified to ensure that each plastic part meets the highest quality standards.
Rapid Response: We are committed to providing fast sample production and production cycle, to ensure that your needs can be met in a timely manner.
Global Services: No matter where you are, we can provide you with quality services to ensure the smooth progress of your business.
Get in touch
Custom Hardware Parts Made Easy
Share detailed information about your needs, including drawings, reference images, and any specific ideas or specifications you have in mind.
Based on your requirements and design, we’ll provide a custom solution and send you a detailed quote within 24 hours.
Once you approve the design and quote, we’ll begin mass production and take care of the shipping, ensuring timely delivery.
Get a Free Quote
Reach out to us for a free quote and expert advice on your custom hardware needs. At Prime, we’ll provide the right solution for your project, ensuring quality and precision every step of the way.