Stamping and drawing parts
The world's leading supplier of metal stamping and drawing parts.
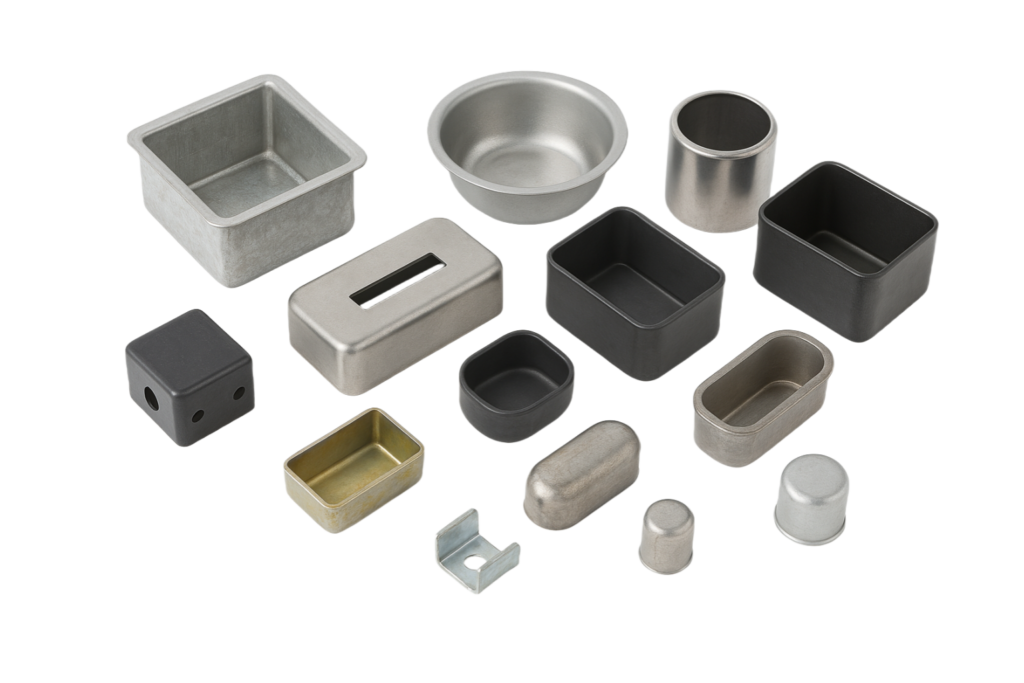
Customized metal stamping and drawing parts.
Metal stamping parts are widely used in a number of industries to provide efficient and accurate solutions. Through customized design, we can produce metal stamping parts for specific purposes according to customer needs, helping industrial production and product upgrading.
Table Of Contents For This Page
At Prime, we provide you with professional service and high-quality products.
Application fields of customized metal stamping parts
Customized metal stamping parts are widely used in automobile, household appliances, electronics, machinery, construction, aerospace, medical equipment and many other industries, it has the characteristics of high precision, high strength and strong customizability. It provides excellent structural support and performance guarantee, and plays a vital role in the fields of body, shell, components and brackets, to meet the industry’s strict requirements for product quality, durability and efficient production.
General Hot Selling Products
Metal stamping and drawing parts can be divided into several main types according to different processes, each process has different characteristics and application fields. The following introduces several common stamping and drawing parts processes and their characteristics and applications:
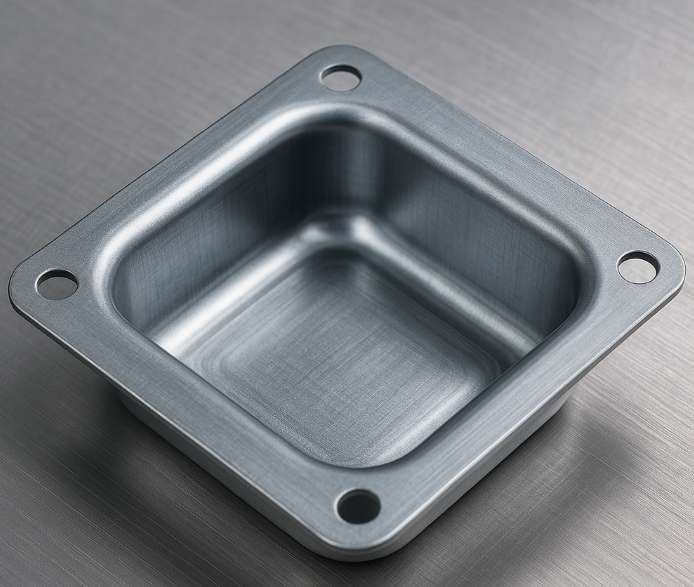
Deep drawing process
Features:
Deep drawing process is the metal sheet through the stamping die to form a larger depth of concave parts. Deep drawing parts usually have complex shape, large depth, smooth surface and high precision.
Applications:
Deep drawing process is widely used in the production of complex parts, such as automobile shell, home appliance shell, aerospace parts, etc. . Due to its high accuracy and strength requirements, it is suitable for high quality, mass production parts.
Drawing process
Features:
Drawing process is the process of drawing a sheet metal into a desired shape by means of a stamping die. It is often used in thinner materials to produce parts of different shapes, such as cylinders, squares, or other complex shapes.
Applications:
The process is widely used in automotive, home appliances, electronics and other industries, such as the production of automotive fuel tanks, home appliances shell, etc. . It is suitable for mass production and has high precision requirements.
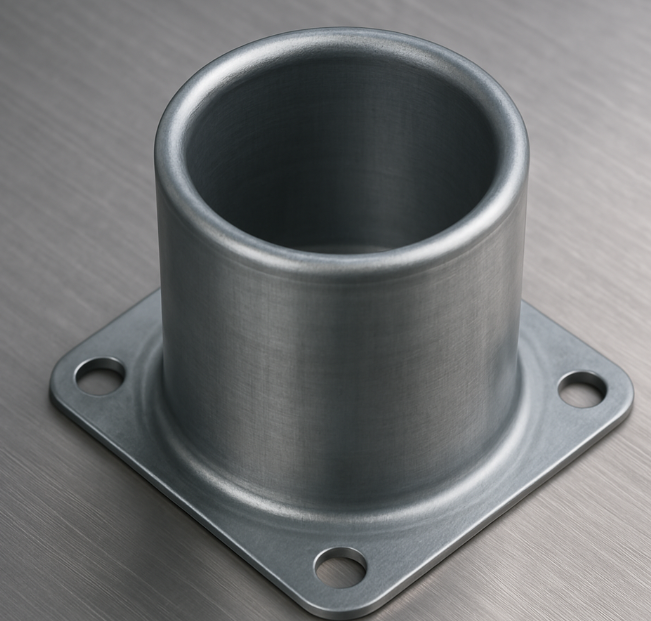
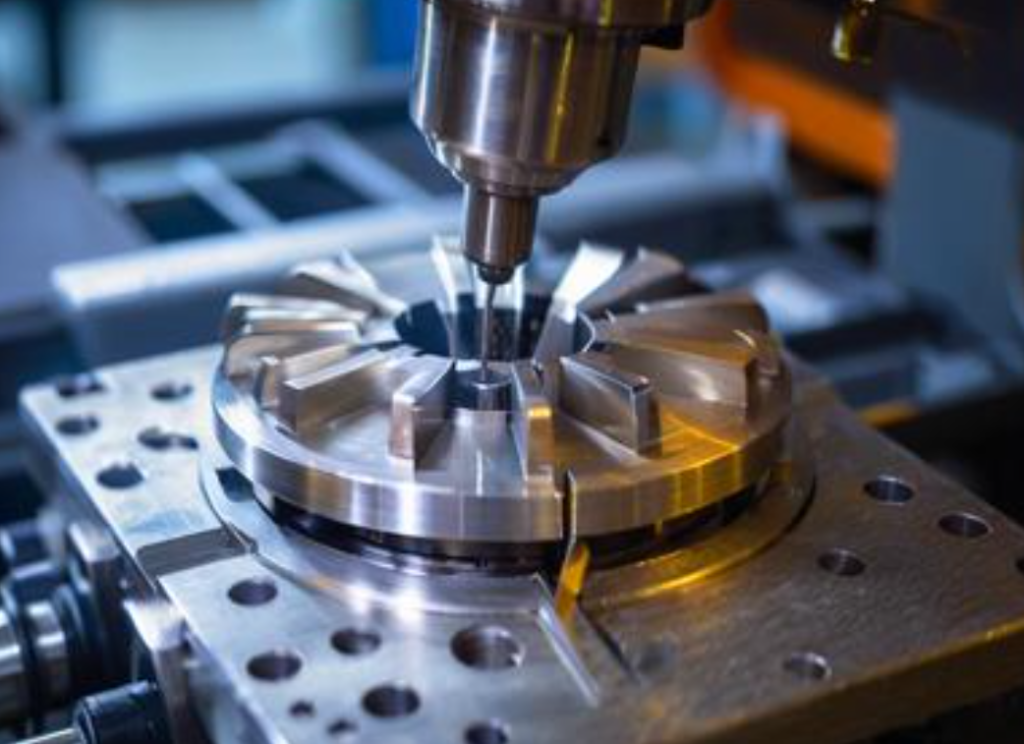
Punching process
Features:
Punching process is through the stamping die will be perforated metal plate, for the manufacture of parts with holes. A plurality of hole positions can be processed at one time, thus saving time and cost.
Application:
Commonly used in the manufacture of filters, audio mesh cover, electrical equipment shell and other components with holes, widely used in electronic products, mechanical equipment and construction industry.
Bending process
Features:
Bending process through the die will be bent into the required angle sheet metal, suitable for the production of parts with a specific bending shape. The process can ensure the high precision and consistency of the product.
Application:
The bending process is widely used in the manufacture of automotive parts, home appliance brackets, electronic equipment frames, etc. . It is especially suitable for the production of parts with complex shapes and precise dimensions.
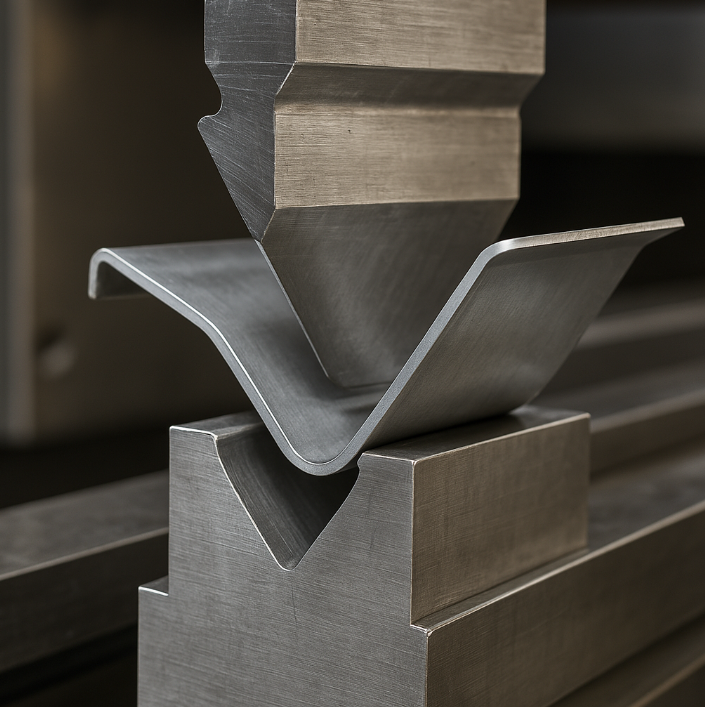
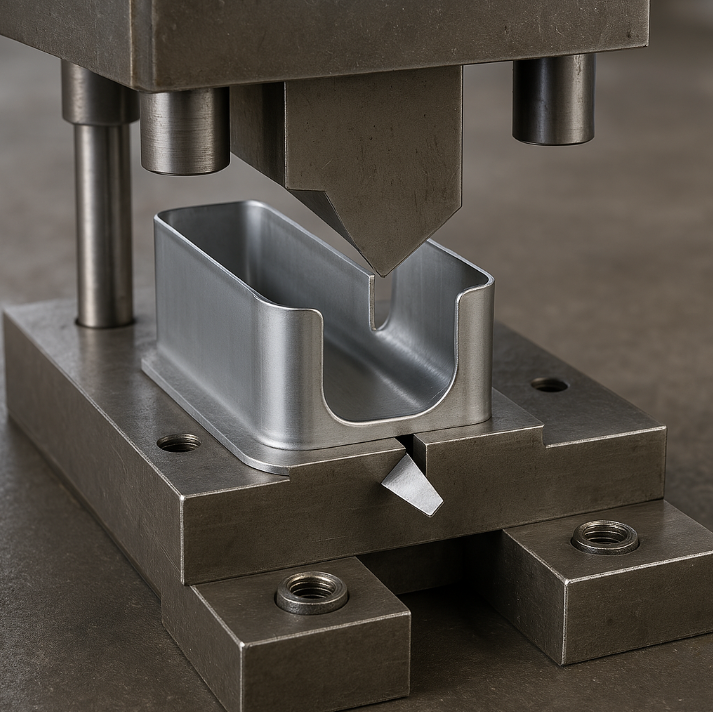
Shearing process
Features:
The shearing process uses a die to cut the sheet metal into the desired shape, making it ideal for simple 2D shaped parts. The process is efficient, low cost and suitable for mass production.
Applications:
Widely used in automotive, home appliances, electronics and other industries, for the manufacture of body panels, brackets, parts and so on.
Rolling process
Features:
The process of calendering a sheet of metal to a specified thickness or shape by continuous die pressure. The process is usually used to produce metal parts in larger sizes and can be mass production.
Applications:
Widely used in construction, mechanical equipment, steel structure and other industries, for the manufacture of steel plates, rails, support structures.
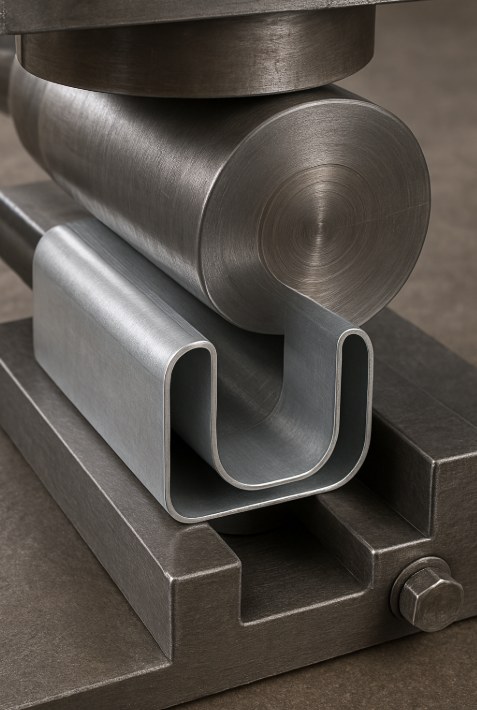
In Summary
The above several kinds of common stamping drawing parts process each has different characteristics and advantages, to meet the production needs of different products. In selecting the appropriate process, need to be based on product structure complexity, production quantity and quality requirements to determine.
The Process Flow & Duration Estimation
The production of metal stamping parts consists of a series of precise steps, each of which is designed to ensure the quality and accuracy of the final product. The following is the standard production process for metal stamping and drawing parts:
Step 1: Design and drawing
Before production, the engineer according to customer needs and technical requirements for detailed design, make accurate drawings. This step ensures that the size, shape, and construction of the product meet the requirements.
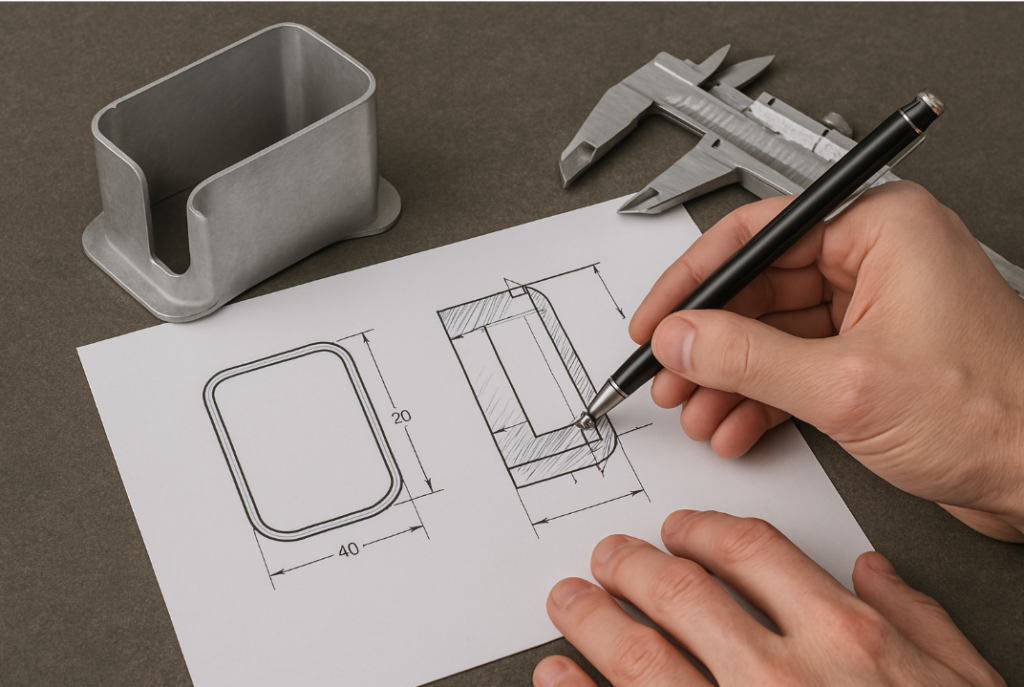
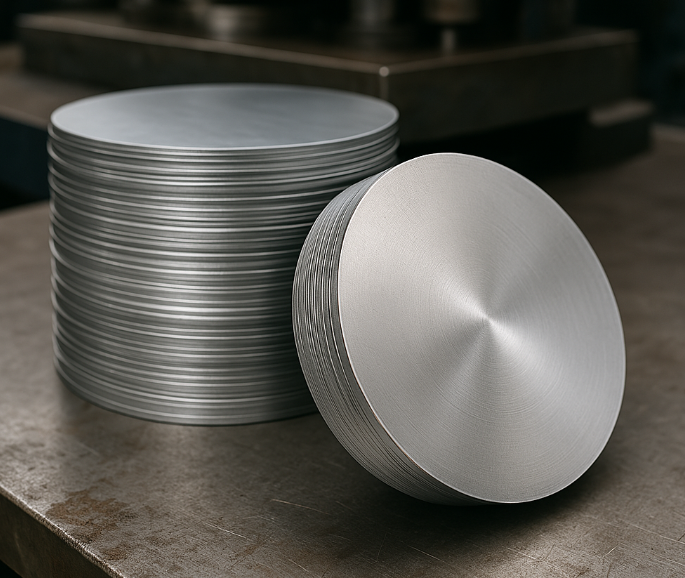
Step 2: Material Preparation
According to the requirements of the design drawings, select the appropriate metal materials. Common materials are steel, stainless steel, aluminum and so on. During this step, the material is cut and cleaned to ensure that its surface is free of contamination and complies with production standards.
Step 3: Mold making
Die is the most critical tool in stamping process. According to the design drawings, the tooling engineer makes and adjusts the tooling to ensure the accuracy of the molding process. The quality of the die directly affects the precision and surface quality of the drawing part.
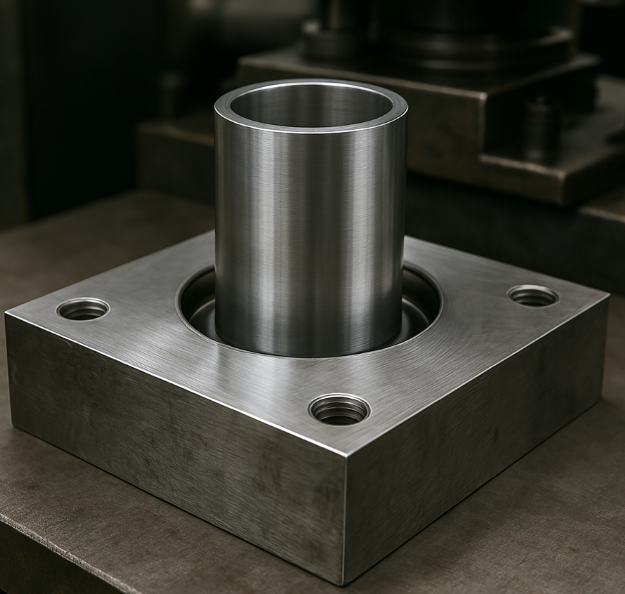
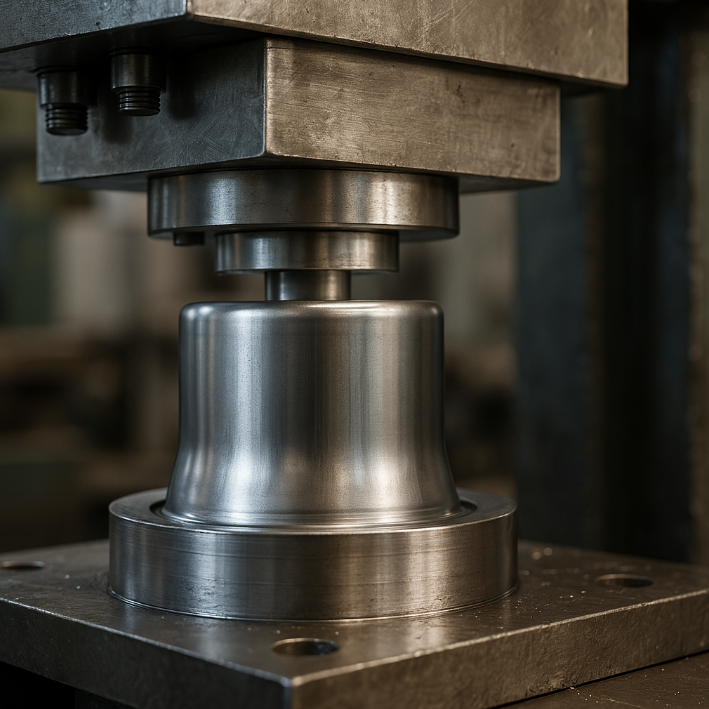
Step 4: Stamping and stretching
Stamping drawing is the use of stamping machine to exert pressure on the metal plate, through the die metal material stretching, deformation, and ultimately form the required shape. In this process, the material is plastically deformed and precisely shaped into a variety of complex shapes.
Step 5: Deburring and trimming
Stretched metal parts may have burrs or other defects that affect their appearance and performance. Therefore, at this stage, the finished product is deburred, sanded, and trimmed to ensure that the surface is smooth and up to standard.
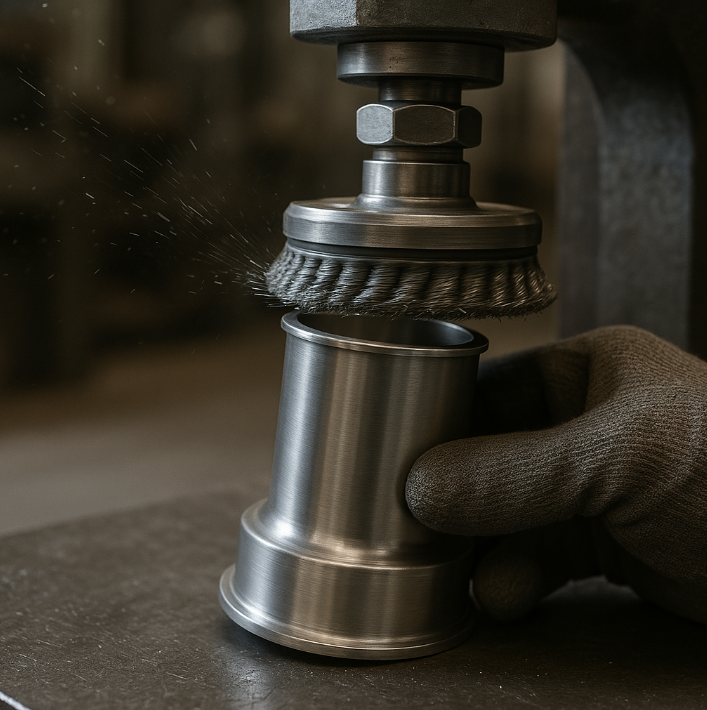
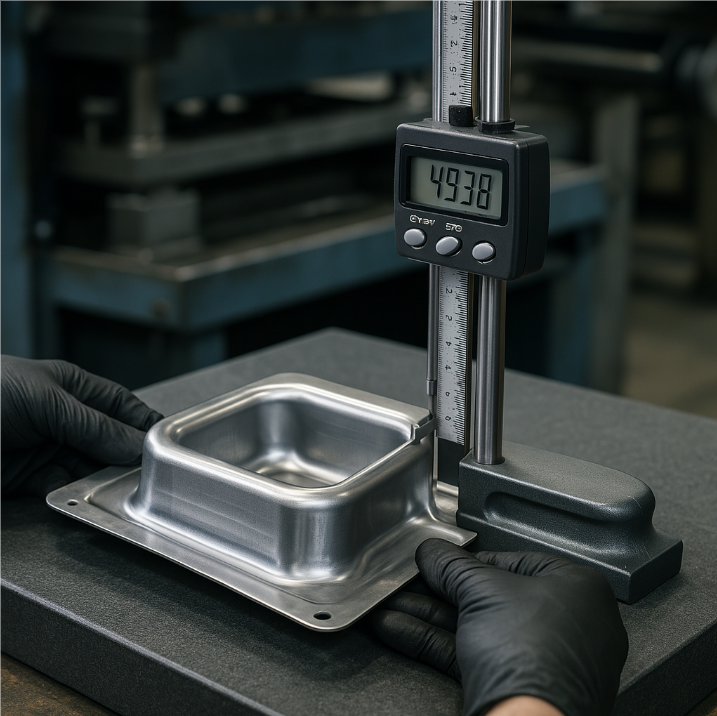
Step 6: Quality testing
Each batch of drawn parts must be subjected to strict quality inspection. Testing includes dimension inspection, hardness test, surface treatment quality, etc. , to ensure that each product is in line with the design requirements.
Step 7: Surface treatment
According to customer requirements, metal stamping parts may require coating, painting, electroplating and other surface treatment to improve corrosion resistance, appearance and wear resistance. This step ensures that the product has higher use value.
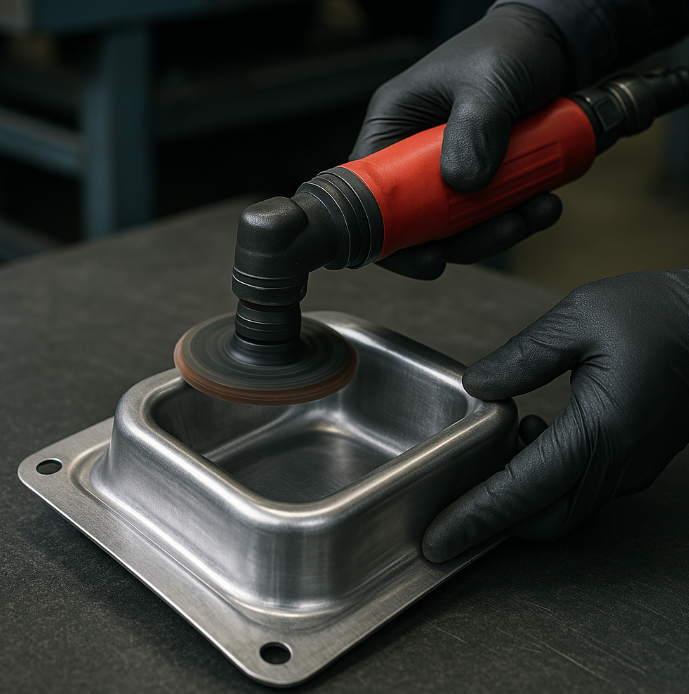
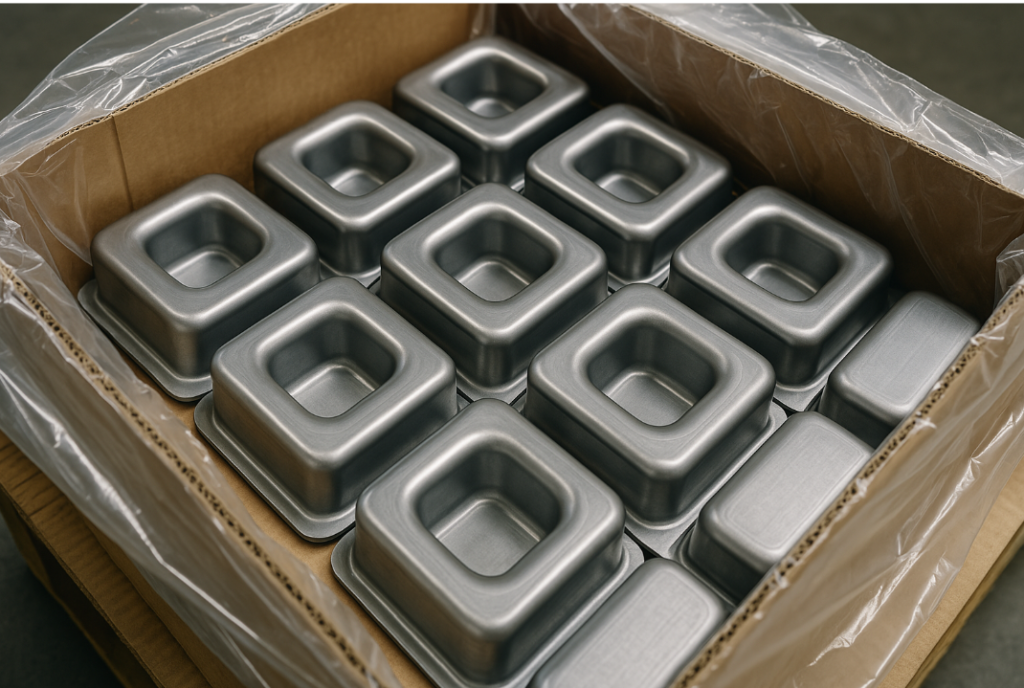
Step 8: Packaging and shipping
After the final inspection and treatment of metal stamping parts will be packaged according to customer requirements. The packaging will be customized to meet shipping requirements and product characteristics to ensure that the product is not damaged during transportation.
Step 9: Delivery of finished product
Upon completion of all inspection and post-processing, the castings will become the final product, ready to be delivered to the customer or used for assembly.
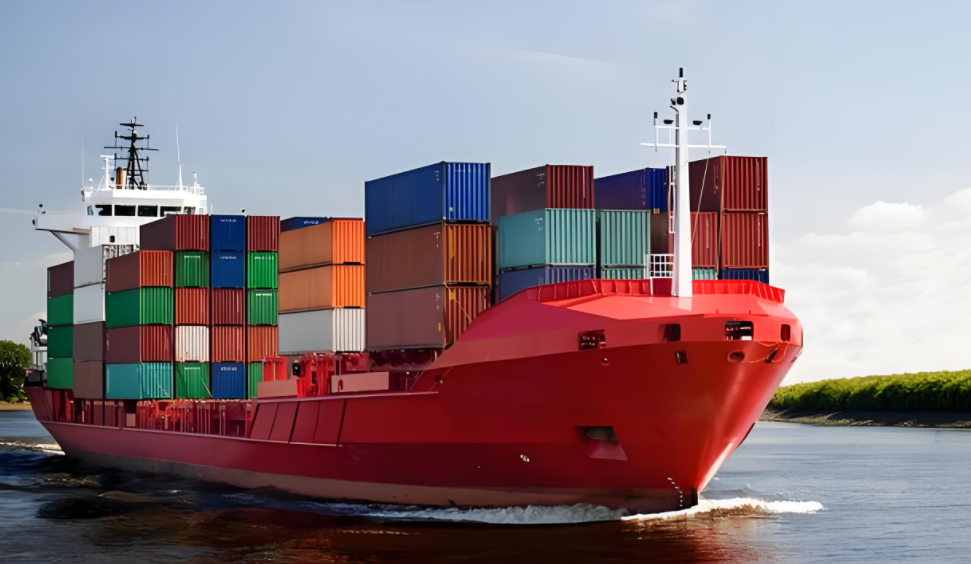
Want to know how to compress lead times?
In order to shorten the production and delivery cycle, we suggest that you tell us your needs in detail, and we will adjust the strategy flexibly according to your requirements to ensure your production and help you succeed!
The Common Pitfalls When Purchasing
Please note that the final cost depends on the customized service you require, the specifications of the raw materials used, the relevant national laws, and the distance of transportation. Take the example of booking a tall container of products:
- Improper material selection: Improper material selection may lead to stamping parts can not reach the strength, corrosion resistance and other performance requirements, affecting the service life.
- Poor design: Immature design will lead to stamping parts production difficulties, increased costs, delivery delays.
- Supplier is not reliable: Some unprofessional suppliers may not be strict in quality control, resulting in substandard products or delivery is not timely.
Raw materials for metal stamping and drawing parts
Metal stamping parts of the raw materials mainly include the following:
Cold-rolled steel plates
Cold-rolled steel sheets are often used to make thin-walled drawn parts with good workability and Surface finish. Common specifications include SPCC, SPCD, SPCE, and so on.
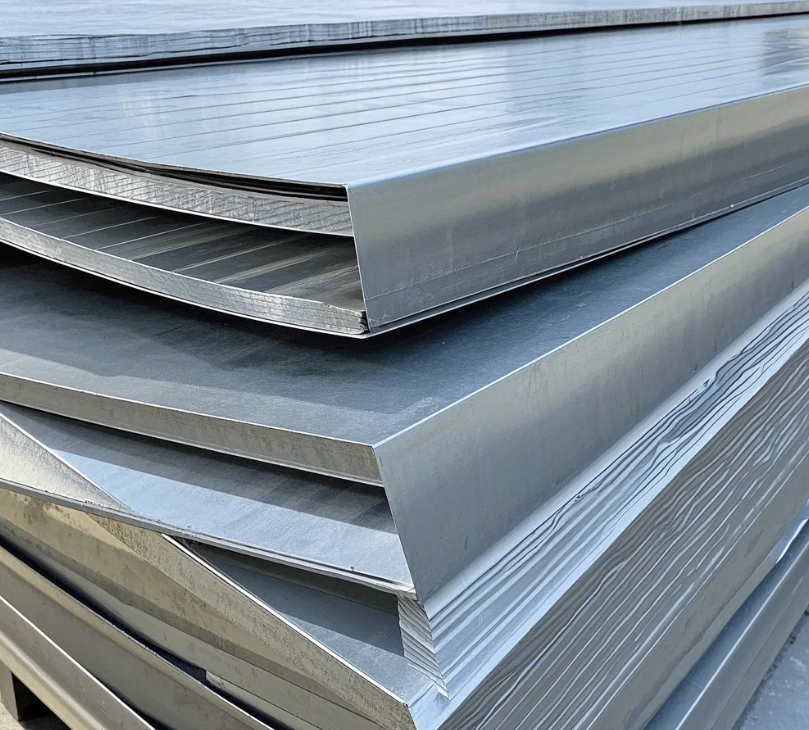
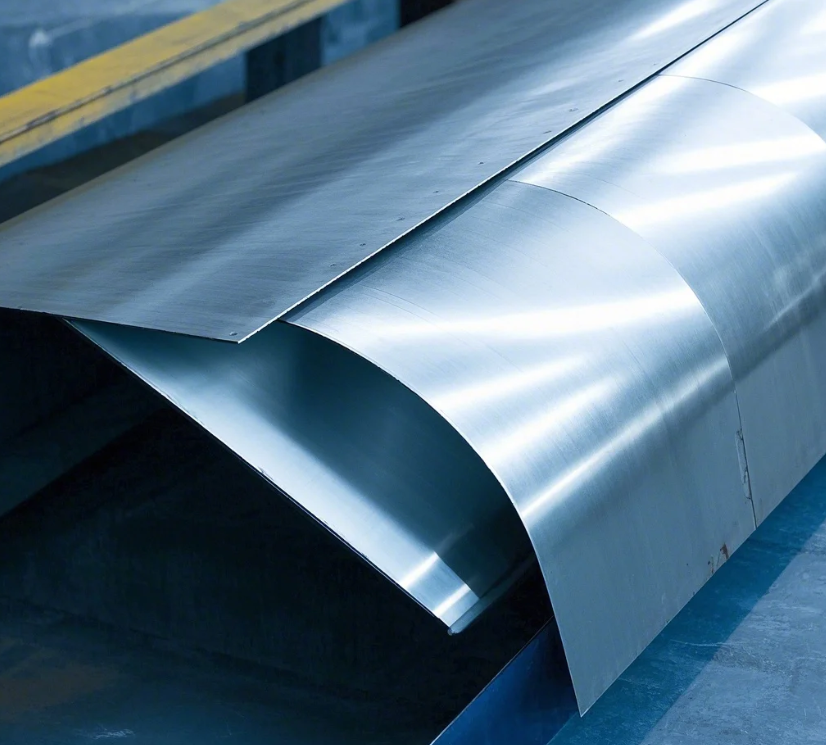
Hot rolled steel plate
Hot-rolled steel plates are usually used for thicker drawn parts with higher strength and toughness. Common specifications are Q235, Q345 and so on.
Stainless steel
Stainless steel drawing parts have excellent corrosion resistance, suitable for all kinds of anti-corrosion environment. Commonly used materials include 304,316,430 stainless steel.
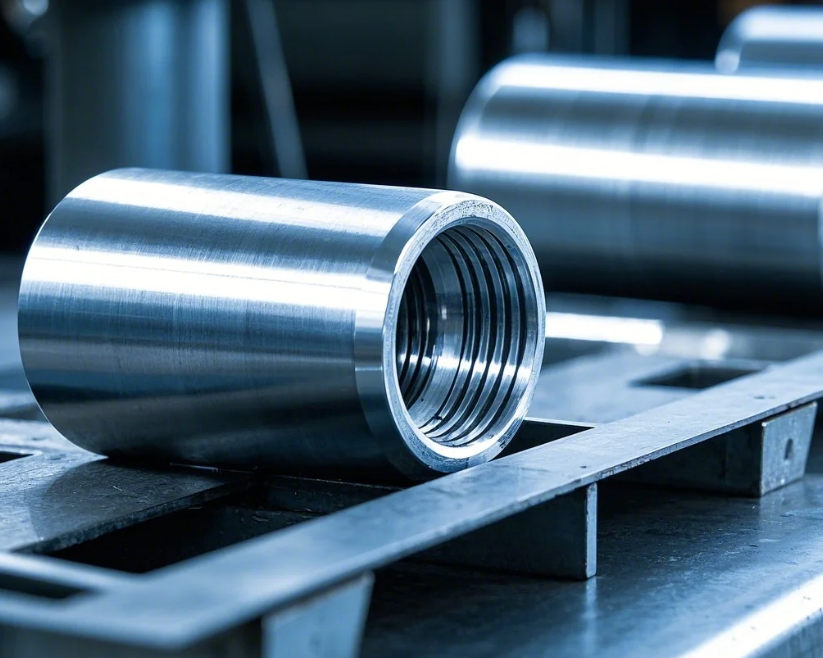
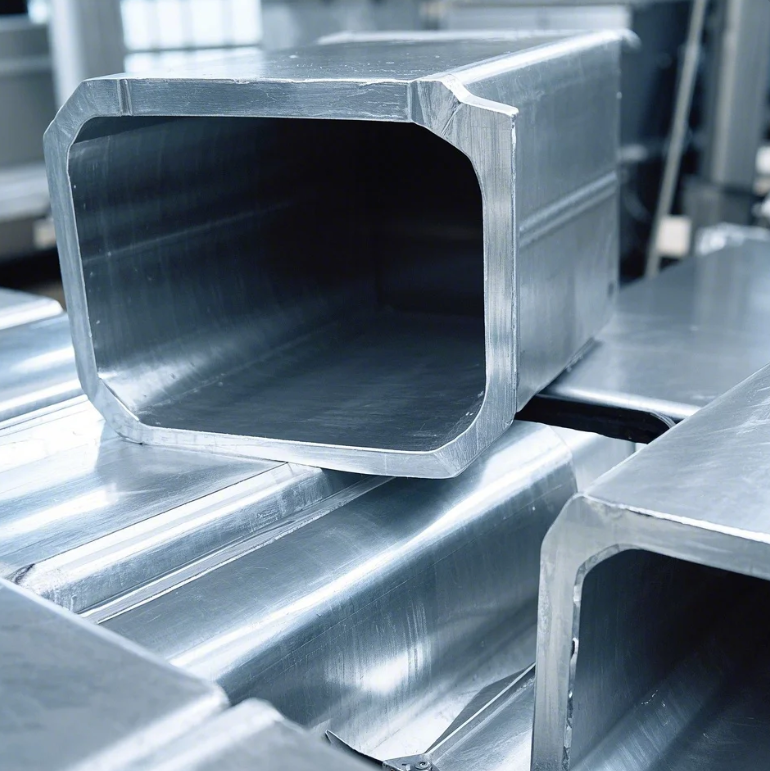
Aluminum
Aluminum alloy drawing parts are widely used in aviation, automobile and electronic products because of their light weight, corrosion resistance and easy processing. Common aluminum alloys include 6061,5052, etc. .
Copper alloy
Copper alloy drawing parts have good electrical conductivity and thermal conductivity, and are often used in electronics, automobile and other industries. Common copper alloys are brass, bronze, etc. .
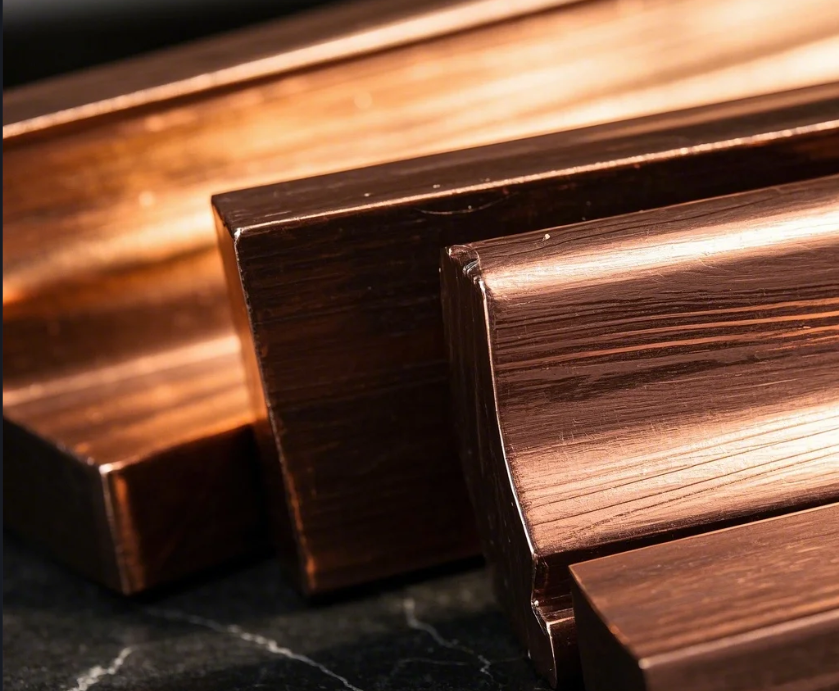
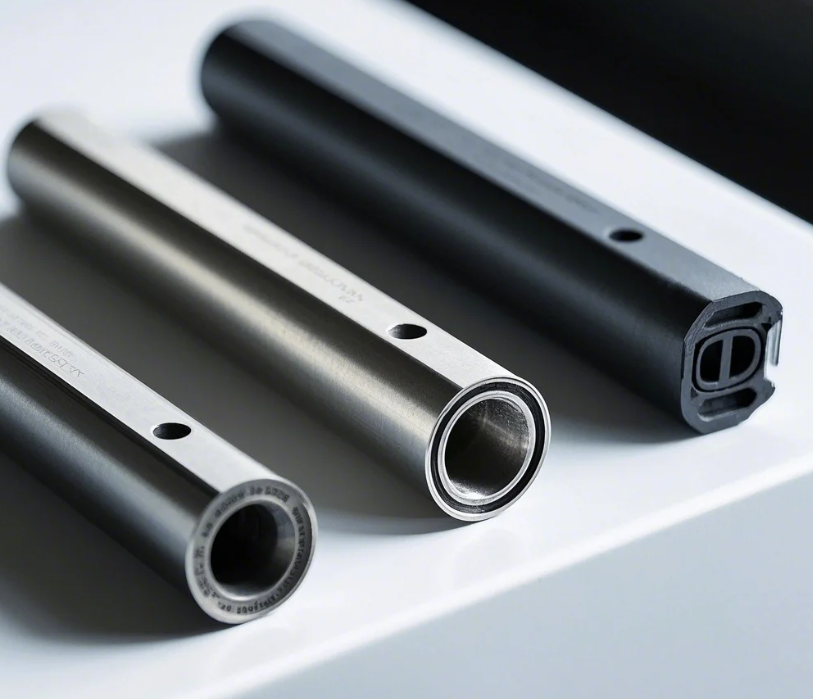
Plastics and composites
Plastic or composite stretch parts provide superior corrosion resistance and light weight in certain applications. Common plastic materials are ABS, PVC and so on.
It is very important to select suitable raw materials for the performance and application of metal stamping parts.
A Brief Self-Nomination, Why Choose Prime?
Choose Us, you will get cost-effective, high-quality, on-time delivery of metal stamping drawing parts solutions.
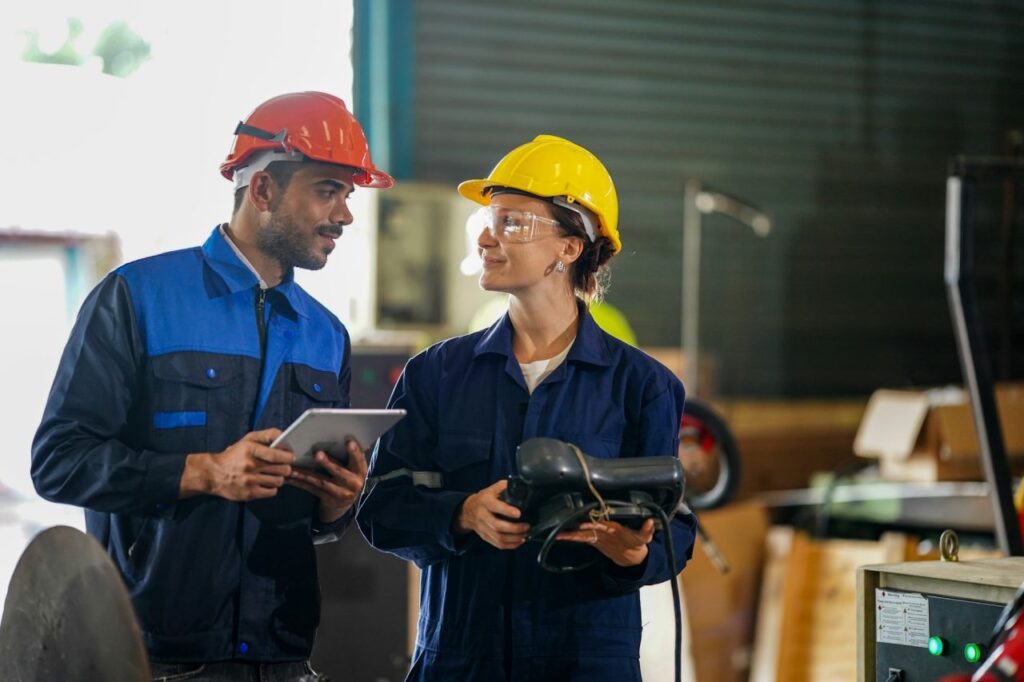
Experience: We have more than 30 years of metal stamping and drawing parts production experience, can provide the industry with high-quality customized metal stamping and drawing parts.
Professional team: Our Engineering team is familiar with metal stamping drawing parts production technology, can provide precise design and production services.
Quality assurance: We are ISO 9001 certified to ensure that every metal stamping and drawing part meets the highest standards of quality.
Rapid Response: We are committed to providing fast sample production and production cycle, to ensure that your needs can be met in a timely manner.
Global Services: No matter where you are, we can provide you with quality services to ensure the smooth progress of your business.
Get in touch
Custom Hardware Parts Made Easy
Share detailed information about your needs, including drawings, reference images, and any specific ideas or specifications you have in mind.
Based on your requirements and design, we’ll provide a custom solution and send you a detailed quote within 24 hours.
Once you approve the design and quote, we’ll begin mass production and take care of the shipping, ensuring timely delivery.
Get a Free Quote
Reach out to us for a free quote and expert advice on your custom hardware needs. At Prime, we’ll provide the right solution for your project, ensuring quality and precision every step of the way.