welding parts
The world's leading supplier of metal welding parts.
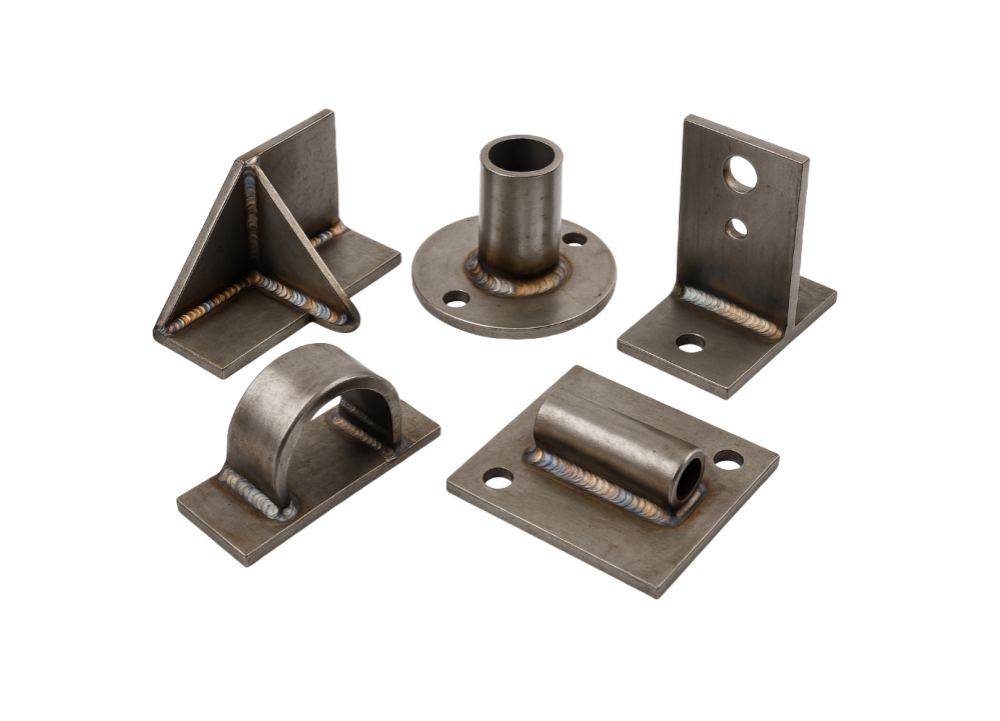
Custom Weldment of metal
Our custom welded metal parts are designed to meet the needs of different industries, using advanced welding technology to ensure that each product has superior quality and precise performance. Whether in the automotive, mechanical, energy, or construction industries, our metal welders provide robust, durable joining solutions.
Table Of Contents For This Page
At Prime, we provide you with professional service and high-quality products.
Application fields of custom welded metal parts
Custom welded metal parts are used in a wide range of industries, from automotive and home appliances to aerospace, energy and construction. They play a vital role in the requirements of strong structure, durability and high precision. Whether it is automotive frames, mechanical equipment, or electrical facilities, metal welding parts have provided the basis for modern industrial support.
General Hot Selling Products
Customized metal weldments can be divided into several main types according to the processing technology, each process has its unique characteristics and application fields. The following are some common types of metal weldments grouped by process and their characteristics and areas of application:
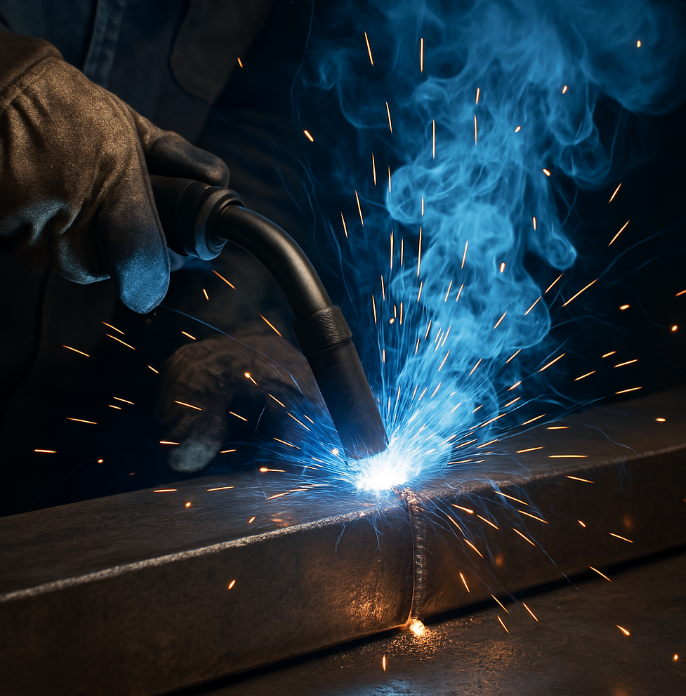
ARC Welding
Features:
- ARC welding is the process by which the arc heats the metal, causing it to melt and join.
- Fast welding speed, wide range of applications, suitable for most metal materials (such as steel, aluminum, etc.) .
- The utility model can be used for welding large thickness metal, and the welded joint has high strength.
Applications:
- Construction industry: steel structure, bridge, building frame, etc. .
- Automotive industry: Automotive chassis, body structure, engine brackets and so on.
- Shipbuilding: hull construction, cabins, etc. .
- Machinery and equipment: large mechanical frame and supporting parts.
TIG Welding
Features:
- Argon arc welding uses inert gas to shield the welding area to ensure that the metal is not oxidized.
- High welding quality, smooth weld, small heat affected zone, suitable for fine welding of thin metal materials.
- Welding process control precision, suitable for precision parts manufacturing.
Applications:
- Aerospace: aircraft structure, engine parts.
- Automotive industry: high-precision body welding, engine parts.
- Precision Instruments: electronic equipment shell, precision instrument bracket.
- Medical Equipment: medical instruments, surgical instruments, etc. .
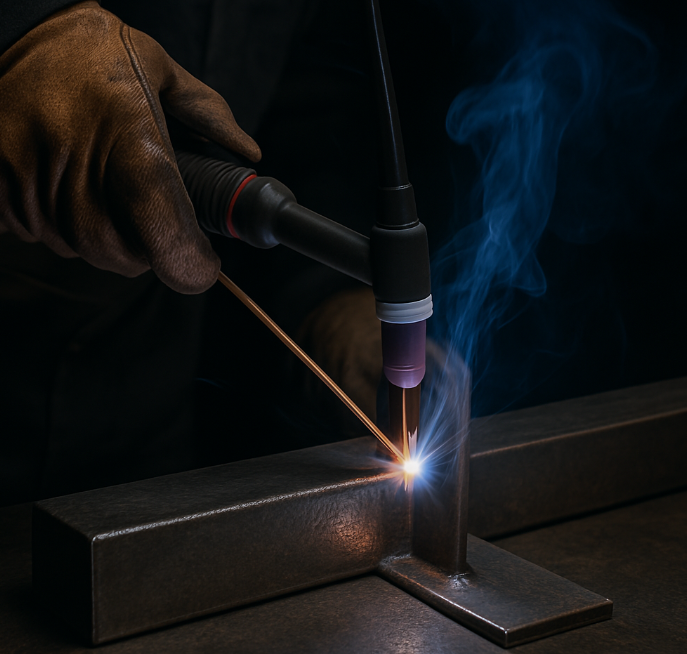
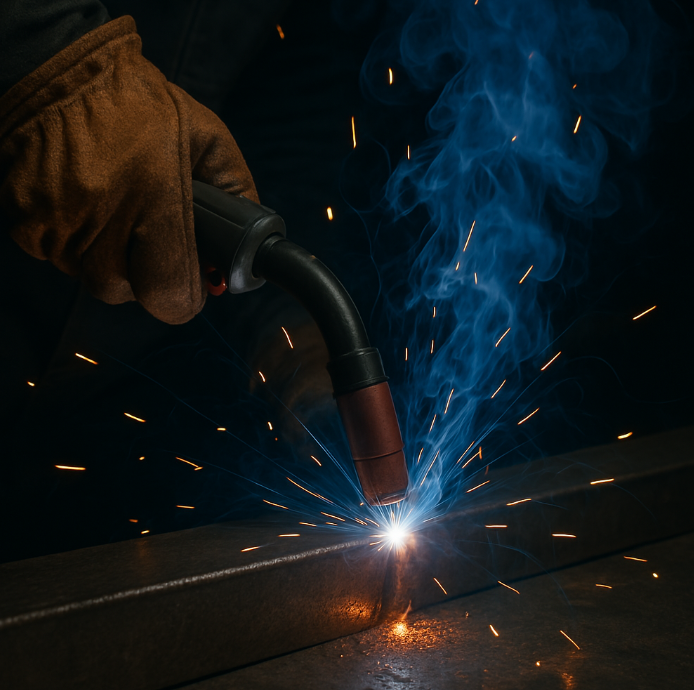
MIG Welding
Features:
- MIG welding uses an arc to heat the wire and substrate, while shielding gases such as argon and carbon dioxide are used to avoid oxidation.
- Fast welding speed, easy operation, good welding quality, suitable for medium and thick plate materials.
- High strength welded joints for high efficiency mass production.
Applications:
- Automobile Manufacturing: welding of automobile body and chassis.
- Shipbuilding: Hull Construction and large welded parts.
- Heavy Machinery: excavators, cranes and other heavy machinery frame.
- Furniture Manufacturing: metal furniture, decorations, etc. .
Laser Welding
Features:
- Laser welding uses a high-power laser beam to focus on the metal surface, quickly heating the metal and melting it to form a welded joint.
- Welding precision is extremely high, heat affected zone is very small, welding speed is fast.
- Suitable for precision, thin material welding, welding seam clean, smooth.
Applications:
- Electronics industry: mobile phone case, computer accessories, LED lamps and so on.
- Automotive industry: body precision welding, sensors and other small parts.
- Medical industry: high-precision medical instruments, endoscopes, etc. .
- Photovoltaic industry: solar cell modules, photovoltaic panels.
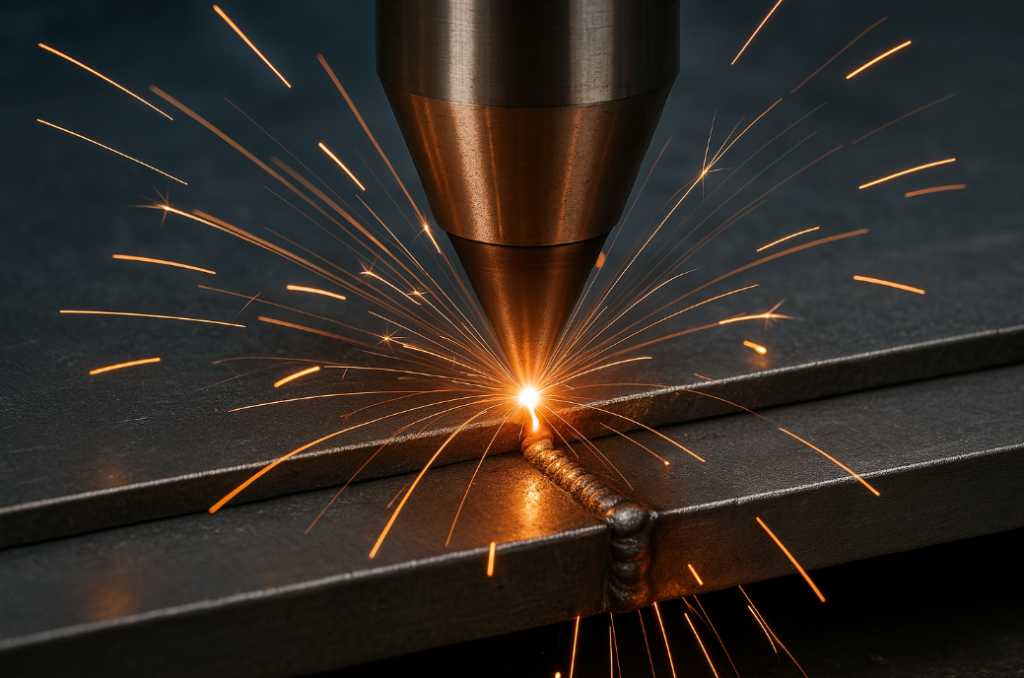
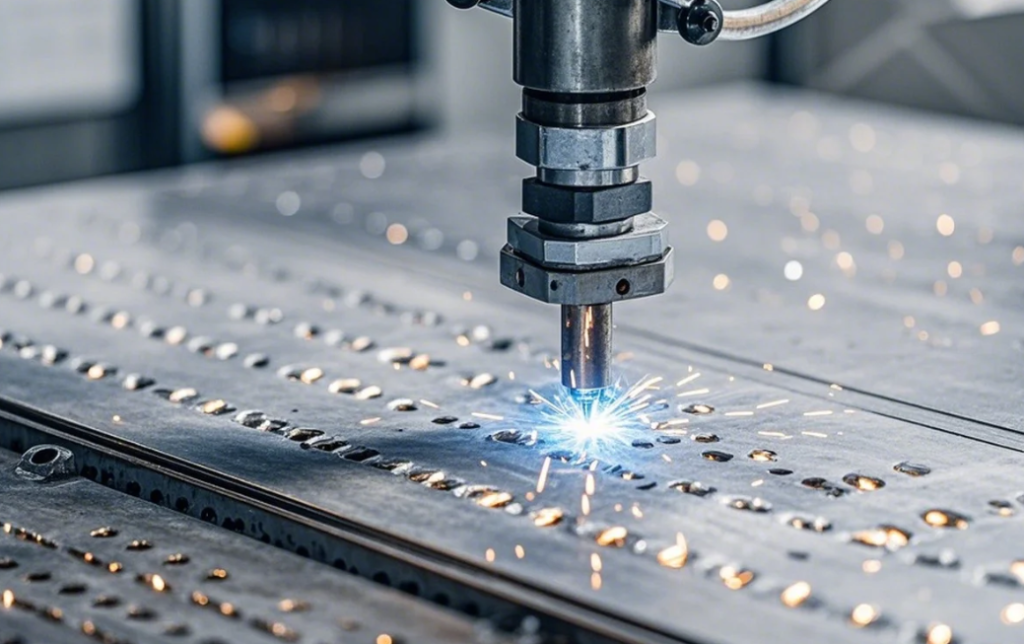
Spot Welding
Features:
- Spot welding is a local welding process, mainly through the electrode pressure and current, so that the local heating of metal to molten state, the formation of welding points.
- Welding speed is very fast, suitable for mass, rapid mass production.
- Less heat input, suitable for welding thin plate materials.
Applications:
- Automotive industry: spot welding body connection, such as doors, roof and bottom, etc. .
- Home appliance industry: Spot Welding Connection of electric appliance shell.
- Electronics: small batteries, electronic component connections, etc. .
Gas Tungsten Arc Welding (GTAW)
Features:
- Similar to conventional TIG welding, it employs a non-consumable tungsten electrode, utilizes argon gas as a shielding gas during welding, and provides precise welding control.
- High welding strength and smooth weld seams make it suitable for the production of precision components.
- Due to its high precision, it is commonly used in the welding of high-value-added products.
Applications:
- Aerospace: welding of aircraft engine parts.
- Nuclear Industry: Welding of nuclear reactor components.
- High-end mechanical manufacturing: welding of high-precision mechanical components.
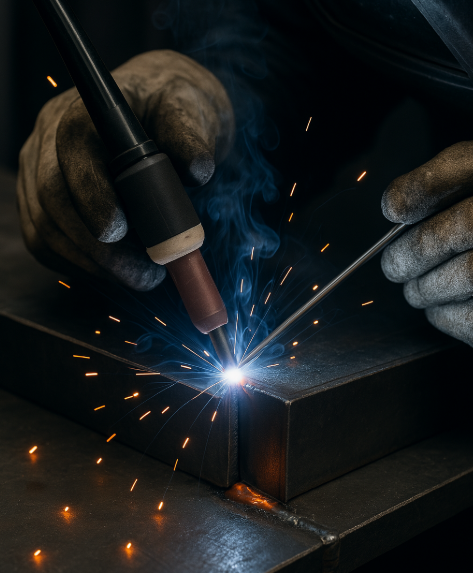
In Summary
Different welding processes have different advantages and application fields in production. Selecting the appropriate welding process can meet the different needs of various industries for the strength, accuracy and production efficiency of welded parts. Whether it is arc welding, argon arc welding, MIG welding, or laser welding, each process has its unique advantages. Depending on the material properties, the workpiece size, and the environment in which it is used, provide tailor-made solutions.
The Process Flow & Duration Estimation
The production process of metal welding parts requires precise process control and high-level technology to ensure that the welding parts meet quality standards and meet the special requirements of customers. The following are the main steps in the production of metal weldments:
Step 1: Design and drawing validation
Before production, the engineer will provide the design plan and technical drawing of the welding parts according to the customer’s requirements and design requirements. Design drawings including welding size, shape, material requirements, as well as welding process selection. Ensure that the design conforms to the feasibility of production, and after customer confirmation to the next step.
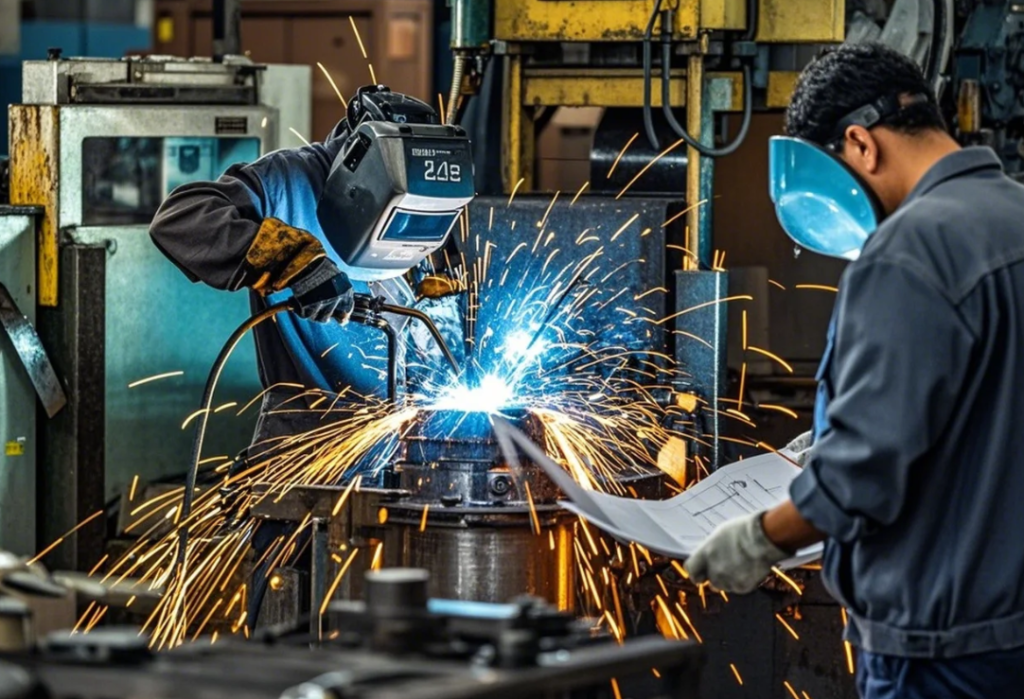
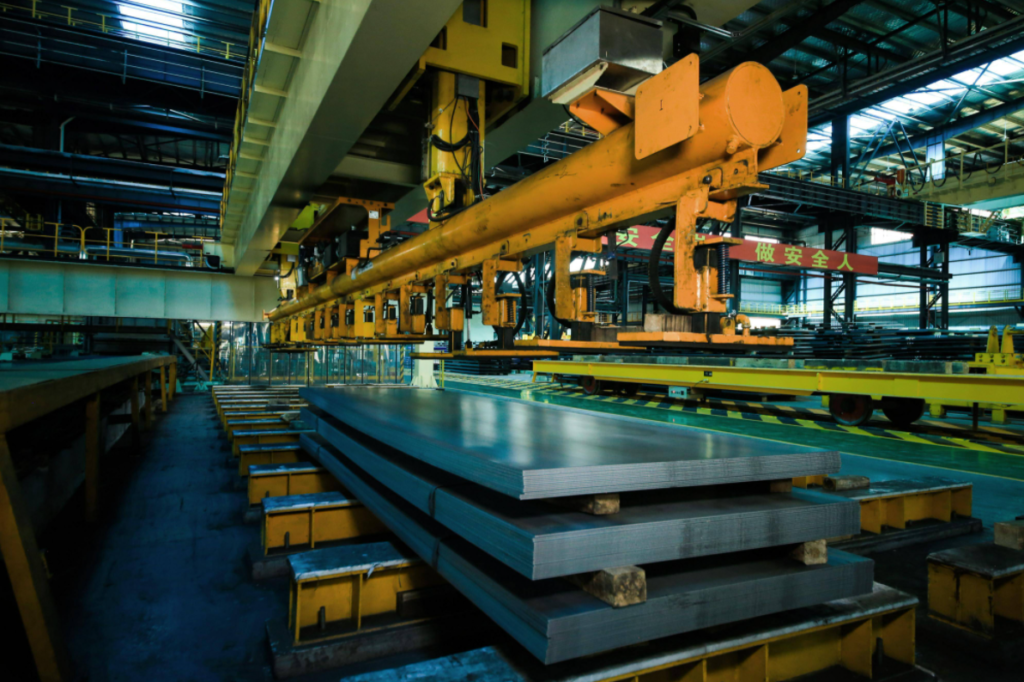
Step 2: Preparation of materials
According to the design drawings and process requirements, select the appropriate metal materials (such as steel, aluminum, stainless steel, etc.) . In this step, the material is pre-inspected to ensure that its quality meets welding requirements. In addition, the selected materials also need to be cleaned to remove surface dirt, grease, oxides, etc. , to ensure the smooth progress of welding.
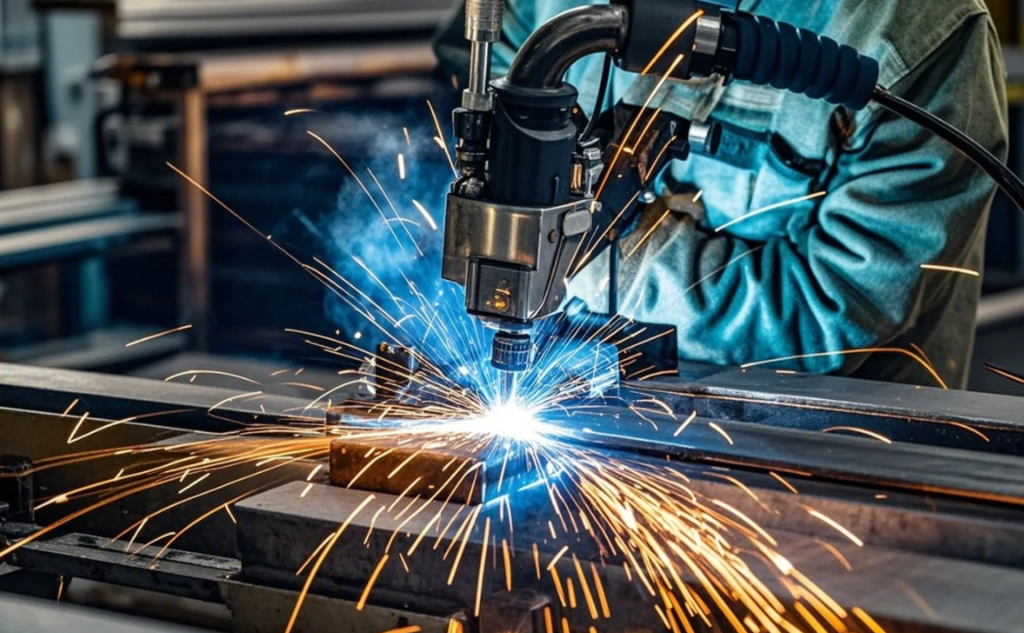
Step 3: Cutting and machining of workpieces
The metal material is cut to a shape and size suitable for welding according to the design dimensions. Common cutting methods include laser cutting, plasma cutting, shearing, etc. . After cutting the metal parts usually need further processing, such as grinding, deburring, etc. , to ensure the accurate size of the workpiece and good welding contact surface.
Step 4: Prepare for welding
Before welding, the welding area needs to be inspected and prepared. First of all, check the fit of the welding workpiece, to ensure that the fitting accuracy of the joint part to meet the requirements. Then, according to the selected welding process (such as arc welding, argon arc welding, MIG welding, etc.) , prepare the appropriate welding materials and shielding gas. Make sure the equipment is debugged and the welding environment is in accordance with the safety standard.
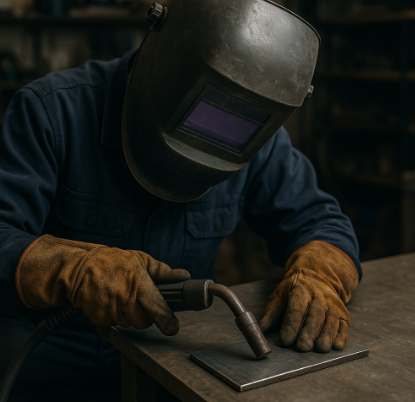
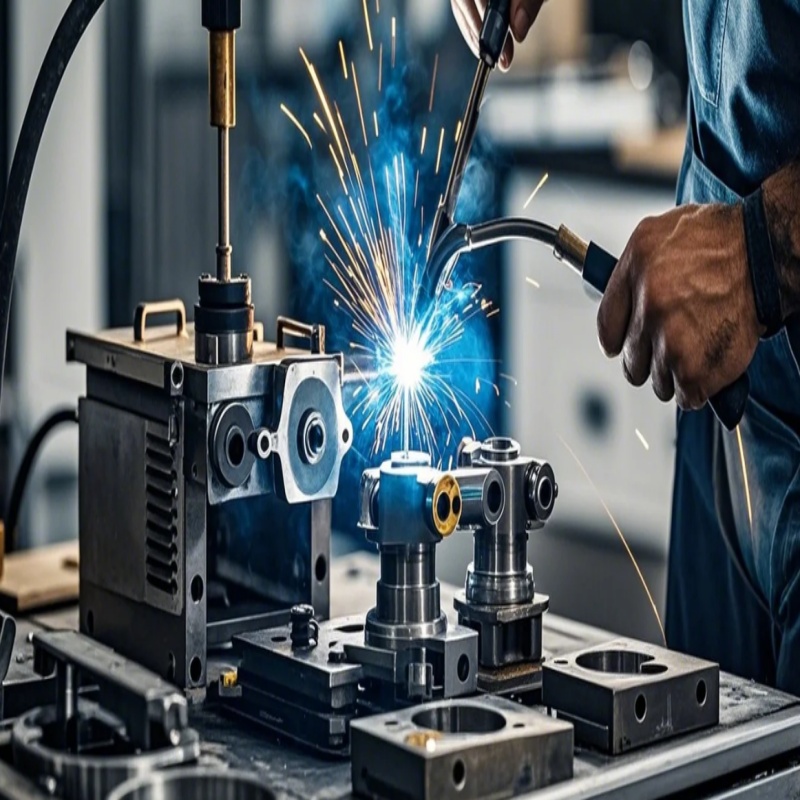
Step 5: Welding operation
Cleaning and deburring: after the casting is removed, there may be excess metal or burrs on the surface, which need to be cleaned by grinding, sandblasting, etc. .
Welding Process Control: to ensure that the welding heat input, molten pool size, welding speed, etc. in line with technological requirements.
Welding Monitoring and adjustment: real-time monitoring of welding in the welding process, if there is a problem can be adjusted at any time process parameters.
Step 6: Post treatment of welding
After the welding is completed, the welded joint needs to be post-treated to remove the residues and oxides generated during the welding process to ensure the strength and appearance of the welded parts. Common post-processing methods include:
- Weld cleaning: use brush, sandpaper and other tools to clean the weld slag around the weld.
- Deoxidation: the use of chemical or mechanical methods to remove oxides in the welding area to prevent corrosion.
- Heat treatment: some welded metal parts may need heat treatment, such as annealing, normalizing, etc. , to eliminate stress and improve strength.
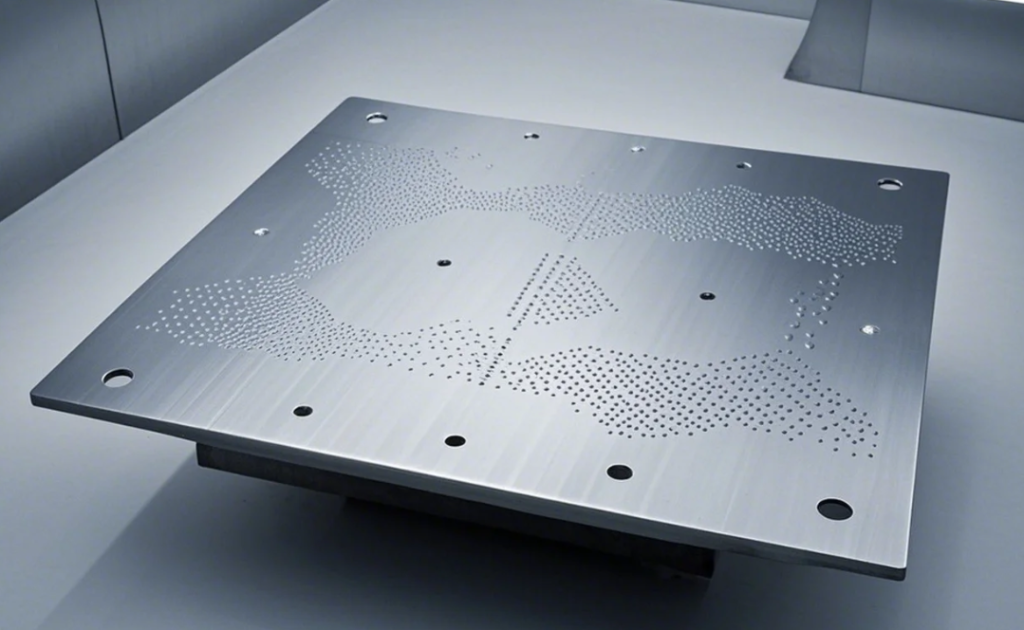
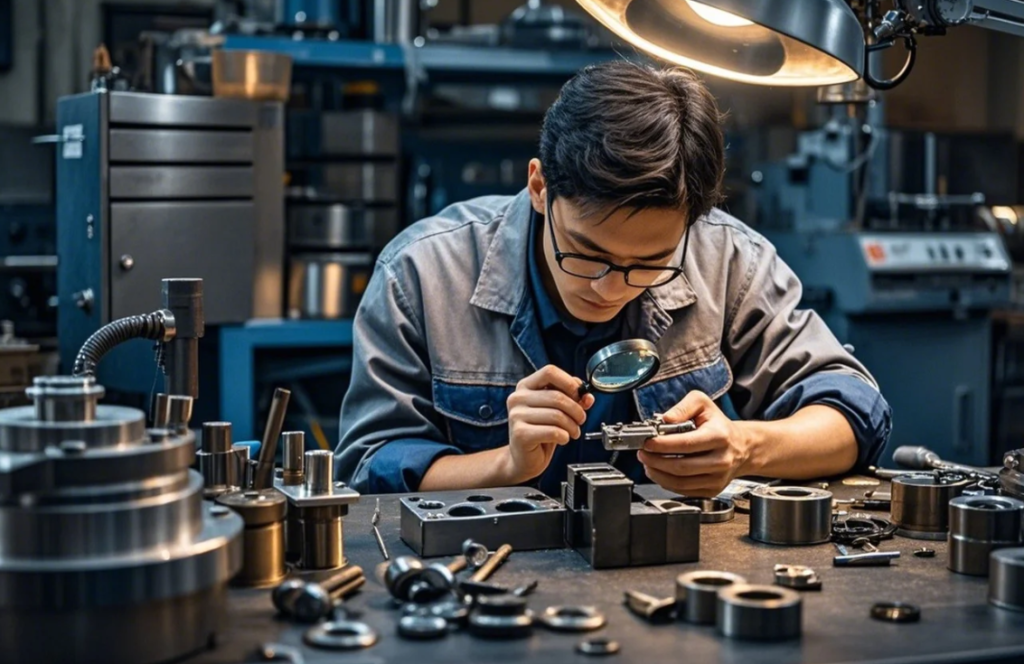
Step 7: Quality inspection
After welding, the metal parts need to go through strict quality inspection to ensure that each product is in accordance with the design standards. The testing items include:
- Dimensional inspection: ensure that the dimensions and shape of the weldment are in accordance with the design drawings.
- Weld inspection: through visual inspection, ultrasonic testing, X-ray inspection and other methods to detect the existence of weld porosity, cracks, lack of penetration and other defects.
- Strength test: tensile, bending and other physical properties of welded parts are tested to ensure that its strength and bearing capacity meet the requirements.
Step 8: Packaging and shipping
After quality inspection of qualified welding parts into the final packaging link. According to the customer’s requirements and product characteristics, select the appropriate packaging, to prevent damage during transportation. Packaged products will be shipped according to the order arrangement to ensure timely delivery to customers.
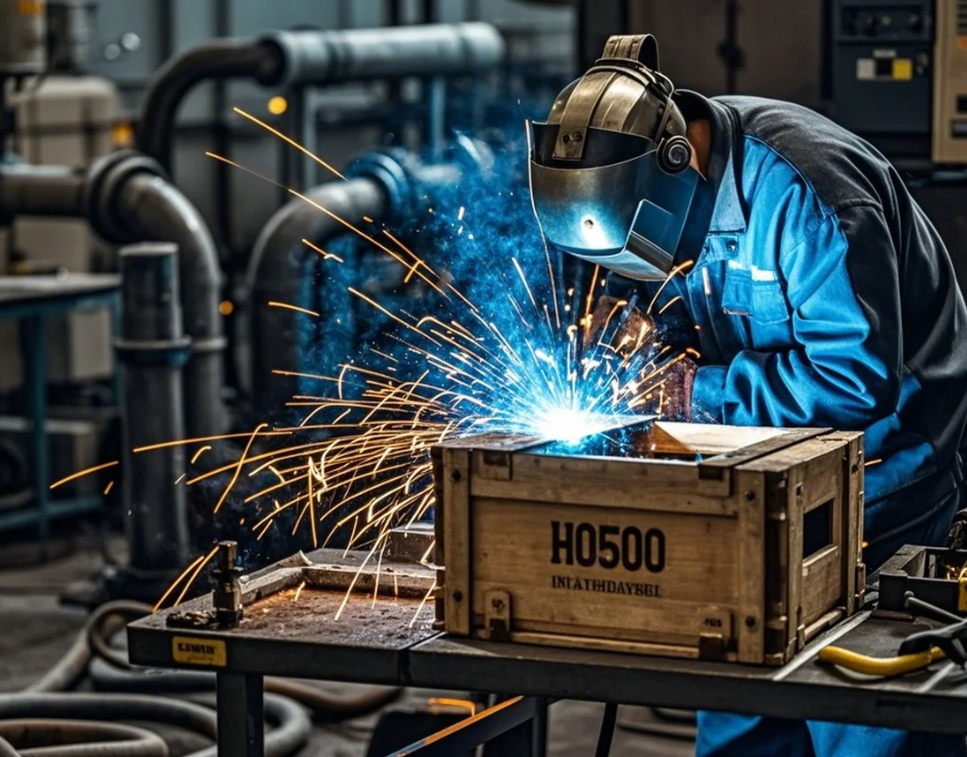
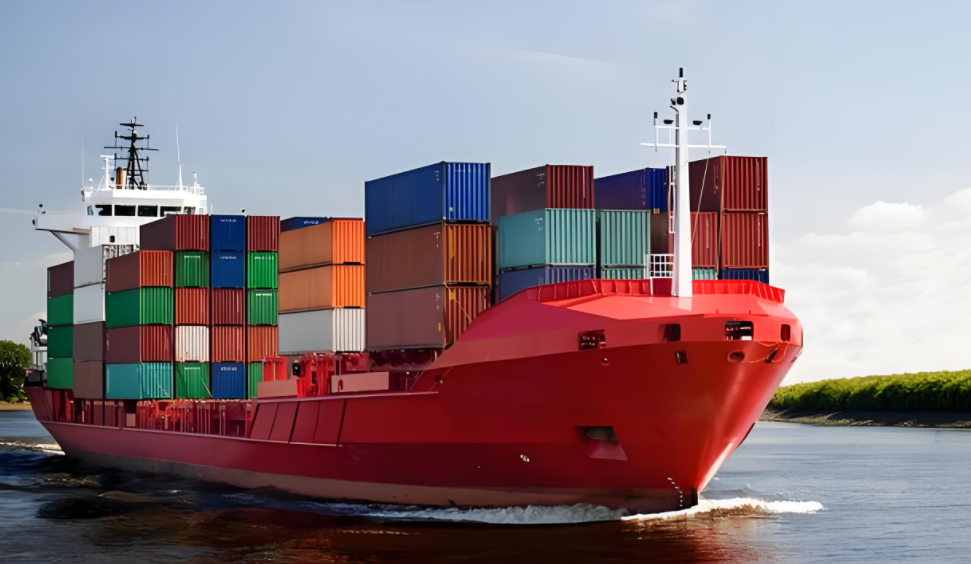
Step 9: Delivery of finished product:
Upon completion of all inspection and post-processing, the castings will become the final product, ready to be delivered to the customer or used for assembly.
Want to know how to compress lead times?
In order to shorten the production and delivery cycle, we suggest that you tell us your needs in detail, and we will adjust the strategy flexibly according to your requirements to ensure your production and help you succeed!
The Common Pitfalls When Purchasing
Please note that the final cost depends on the customized service you require, the specifications of the raw materials used, the relevant national laws, and the distance of transportation. Take the example of booking a tall container of products:
- Improper material selection: improper material selection may lead to metal welded parts can not reach the strength, corrosion resistance and other performance requirements, affecting the service life.
- Poor design: immature design can lead to difficulties in the production of welded metal parts, increased costs, and delays in delivery.
- Supplier is not reliable: some unprofessional suppliers may not be strict in quality control, resulting in substandard products or delivery is not timely.
Raw materials for metal welding parts
The raw materials for metal weldments usually include the following types:
Steel:
- Carbon Steel: most commonly used for welding, with good weldability and adaptability, applicable to the manufacture of various structural parts.
- Alloy Steel: by alloying elements to enhance the strength of steel, corrosion resistance and high temperature resistance, commonly used in high strength requirements of welding parts.
- Stainless Steel: has excellent corrosion resistance and heat resistance, often used in the requirements of strong corrosion resistance of the environment, such as chemical equipment, food processing and other fields.
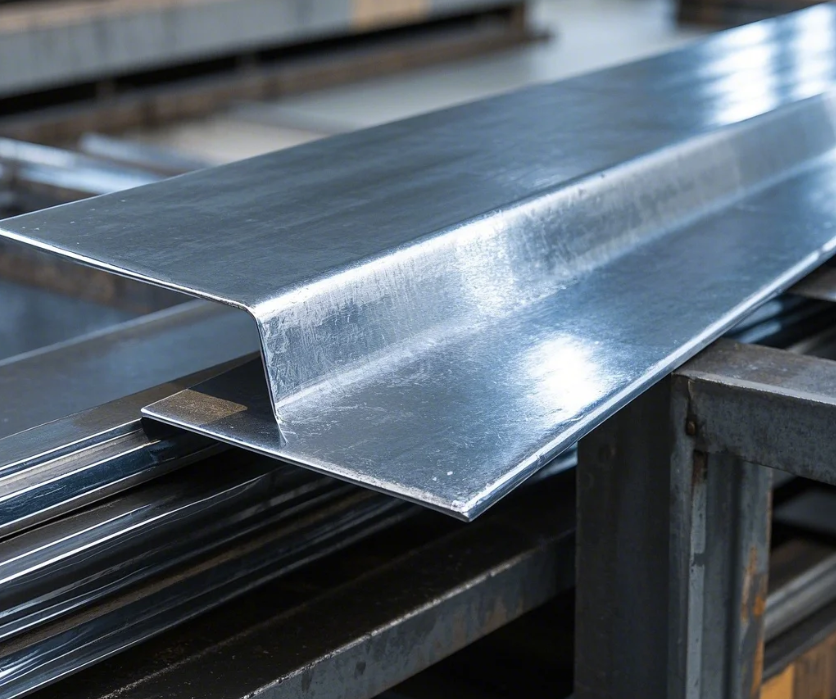
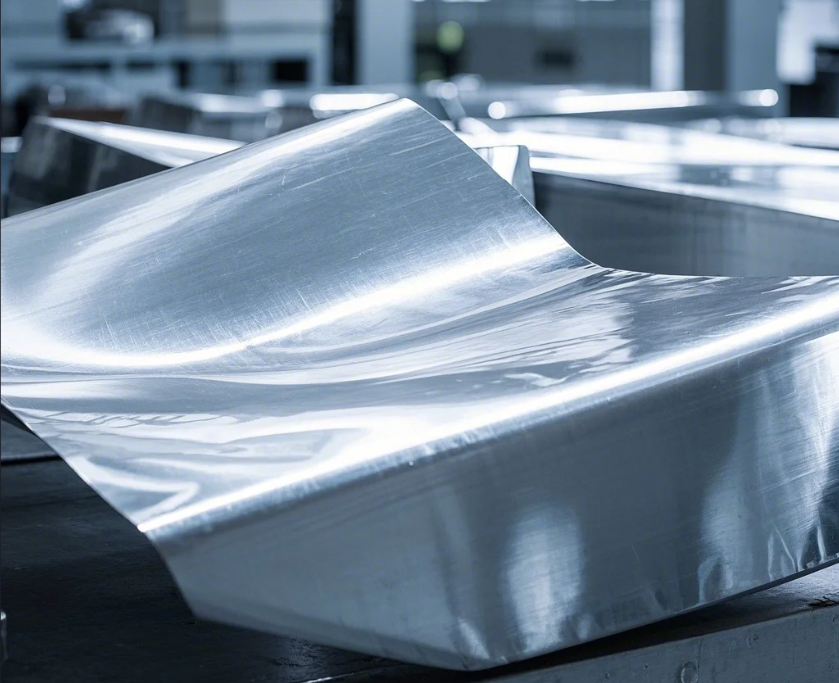
Aluminum:
Aluminum and its alloys are very popular in welding because they are light and have a good strength/weight ratio. Commonly used in aerospace, automotive and marine applications.
Copper alloy:
Copper and its alloys are less commonly used in welding, but they are ideal for applications that require good electrical conductivity or corrosion resistance, such as electrical equipment or marine applications.
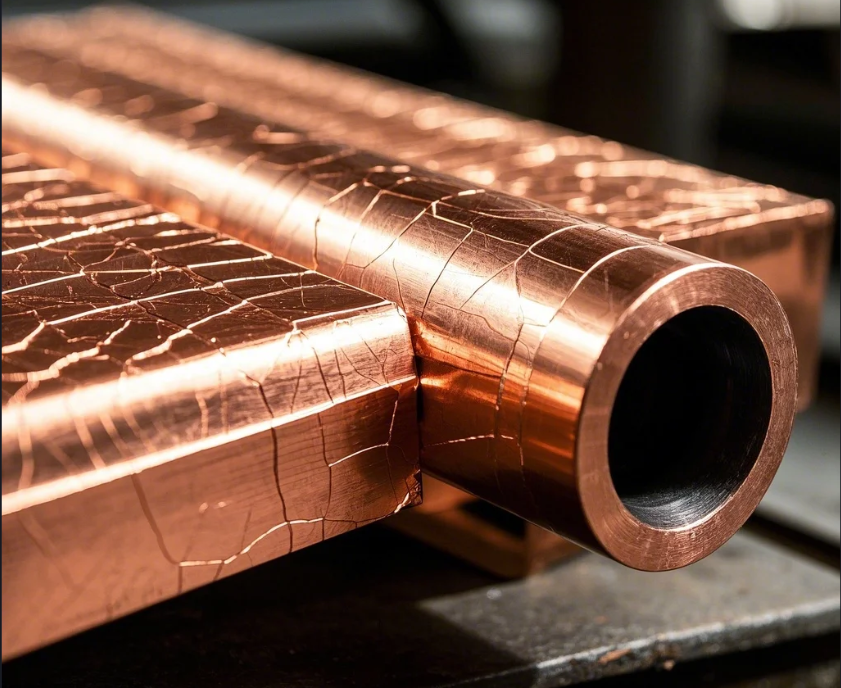
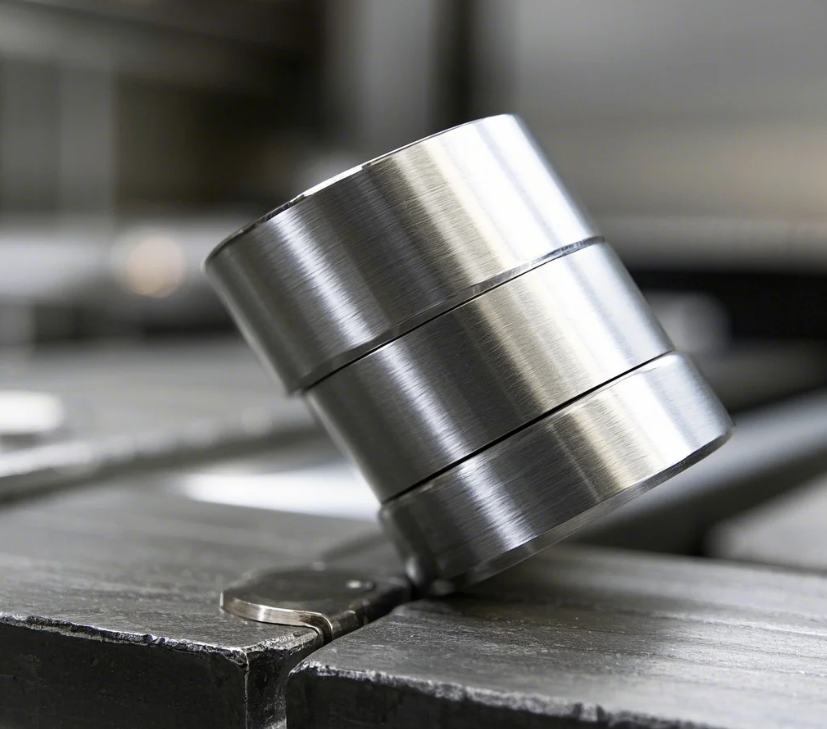
Nickel alloy:
Used in high temperature and corrosive environment, especially in oil, natural gas, chemical industry and other fields, with high corrosion resistance and thermal cracking resistance.
Titanium:
Titanium and its alloys are widely used in aerospace, military and chemical equipment because of their very strong corrosion resistance and high temperature resistance.
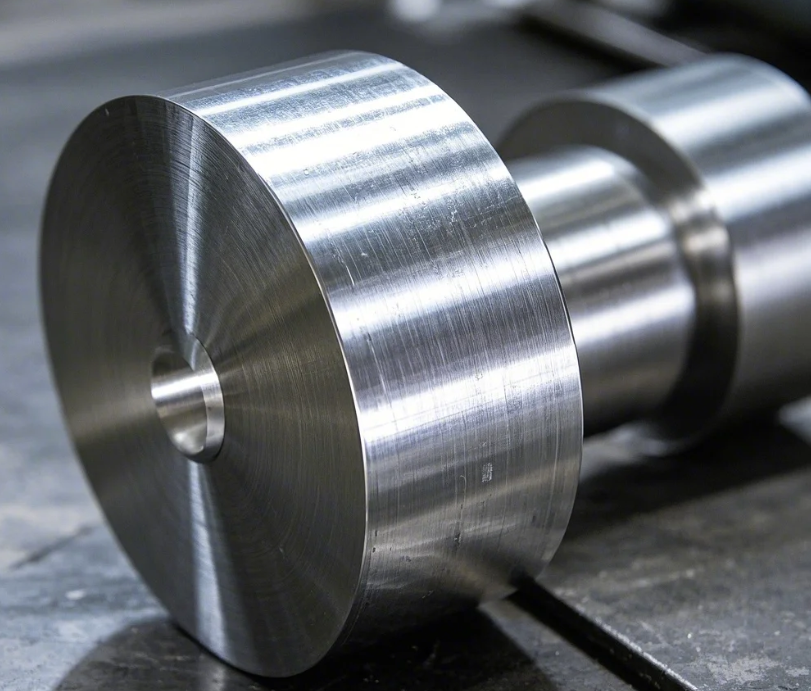
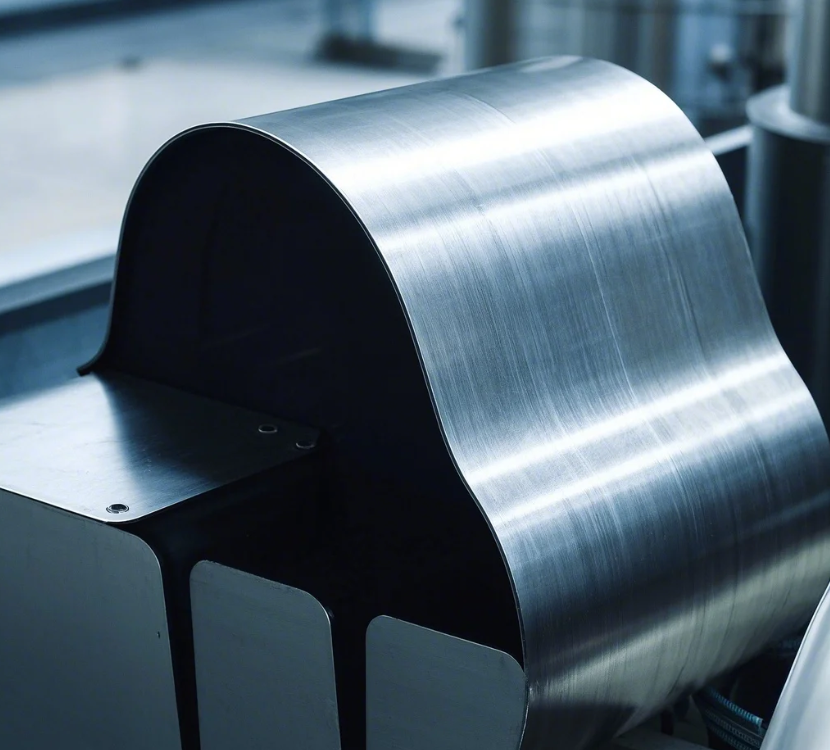
Plastic coating metal:
Certain metallic materials are treated with plastic coatings to increase corrosion resistance or provide other properties. These materials can also be used for welding in certain applications.
The choice of welding consumables usually depends on the service environment, strength requirements, corrosion resistance requirements, and cost budget of the weldment.
A Brief Self-Nomination, Why Choose Prime?
Choose Us, you will get cost-effective, high-quality, on-time delivery of metal weldment solutions.
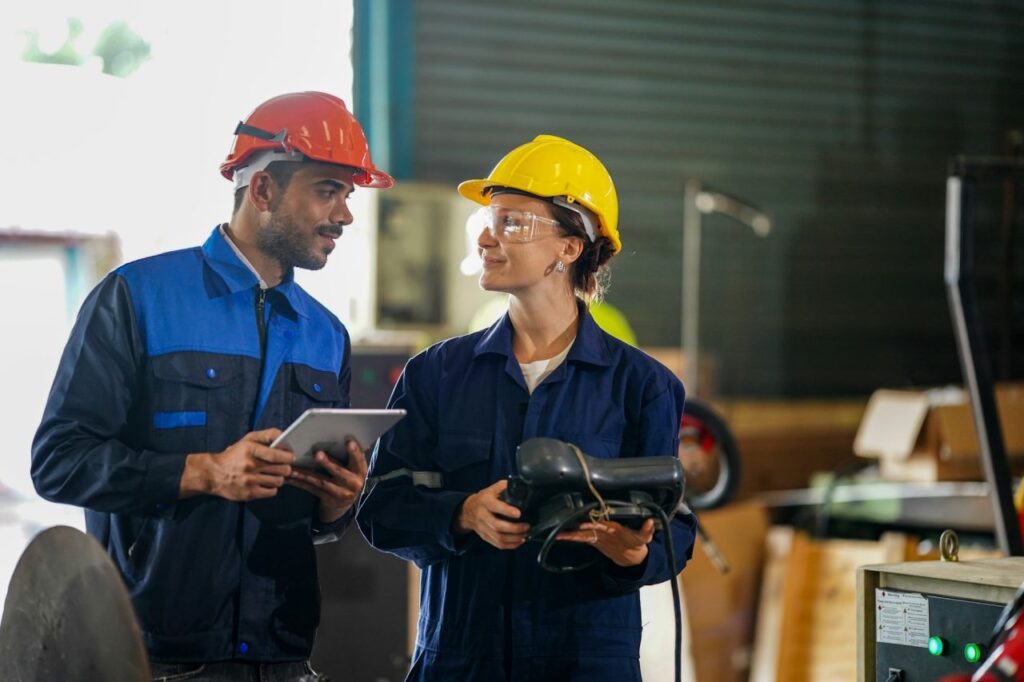
Experience: we have more than 30 years of metal welded parts production experience, can provide high-quality custom metal welded parts for the industry.
Professional team: Our Engineering team is familiar with metal welded parts technology, can provide precise design and production services.
Quality assurance: WE ARE ISO 9001 certified to ensure that every metal welded part meets the highest standards of quality.
Rapid Response: We are committed to providing fast sample production and production cycle, to ensure that your needs can be met in a timely manner.
Global Services: No Matter where you are, we can provide you with quality services to ensure the smooth progress of your business.
Get in touch
Custom Hardware Parts Made Easy
Share detailed information about your needs, including drawings, reference images, and any specific ideas or specifications you have in mind.
Based on your requirements and design, we’ll provide a custom solution and send you a detailed quote within 24 hours.
Once you approve the design and quote, we’ll begin mass production and take care of the shipping, ensuring timely delivery.
Get a Free Quote
Reach out to us for a free quote and expert advice on your custom hardware needs. At Prime, we’ll provide the right solution for your project, ensuring quality and precision every step of the way.