Metal forgings
The world's leading supplier of metal forging parts.
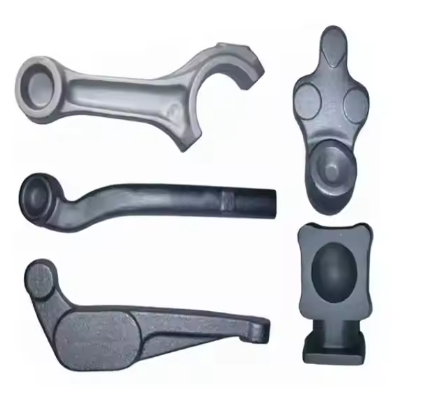
Custom forged parts of metal
As a professional metal forging supplier, we are committed to providing high quality, customized metal forging solutions to our customers around the world. With many years of industry experience and advanced production technology, our forgings are widely used in aerospace, automotive manufacturing, energy, machinery and equipment and other fields. We provide free forging, die forging, rolling forging and precision forging and other processes to meet the different needs of various customers. Whether small-scale customization or mass production, we can ensure high-precision, high-intensity products, and provide customers with quality after-sales service. Choose Us, you will get efficient, reliable metal forging products, help your business success.
Table Of Contents For This Page
At Prime, we provide you with professional service and high-quality products.
Application fields of customized metal castings
Customized metal forgings are widely used in aerospace, automotive manufacturing, machinery and equipment, energy, construction, military and other industries. Because of its superior mechanical properties, corrosion resistance and good workability, metal forgings are particularly important in applications with high strength, high temperature resistance and compression resistance. They can withstand extreme working conditions and ensure efficient and safe operation of the equipment.
General Hot Selling Products
Customized metal forgings can be divided into several main types according to the processing technology, each process has its unique characteristics and applications. The following are some of the common types of metal forging parts grouped by process and their characteristics and areas of application:
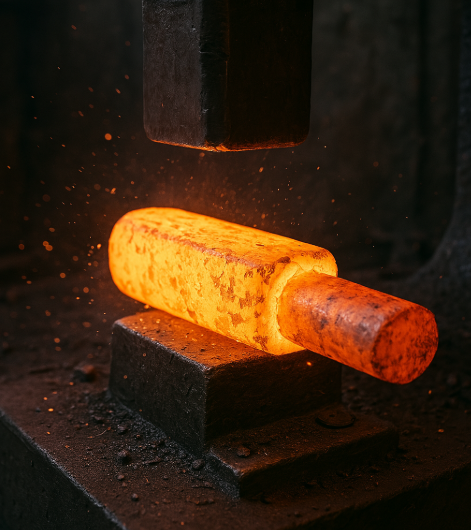
Free forging
Features:
Free forging is through mechanical forging hammer or hydraulic press and other tools, the metal billet heating to the appropriate temperature, through the beating, pressing and other ways to change the shape of the metal. This process does not depend on the die, the shape of the workpiece is relatively simple and the size is large.
Applications:
Free forging is widely used in heavy machinery, metallurgical equipment, pressure vessels, ships, mining machinery and other fields. Commonly used in the manufacture of large-size forgings, such as shafts, rings, discs and so on.
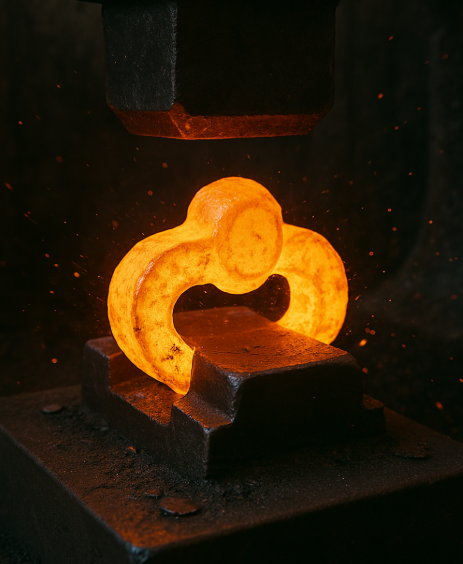
Die forging
Features:
Die forging is the metal billet heating, into the mold through the press or hydraulic press for compression molding. Die forging can produce forgings with high precision and uniform size, and can handle parts with complex shape.
Applications:
Die forging is widely used in aerospace, automotive, electronics, engineering machinery and other high-precision requirements of the field. Especially suitable for the production of gears, bearings, automotive engine parts, aerospace parts.

Rolling forging
Features:
Rolling forging is through rolling tool on the metal billet for rotary forging, so that it gradually formed in the rotation of the required shape. This process can effectively improve the microstructure and properties of metal materials, and increase the strength and durability of parts.
Applications:
Roll forging is mainly used for shafts, gears, transmission parts and other parts that require high strength and long life. It is widely used in automobile, aerospace, railway and other industries.
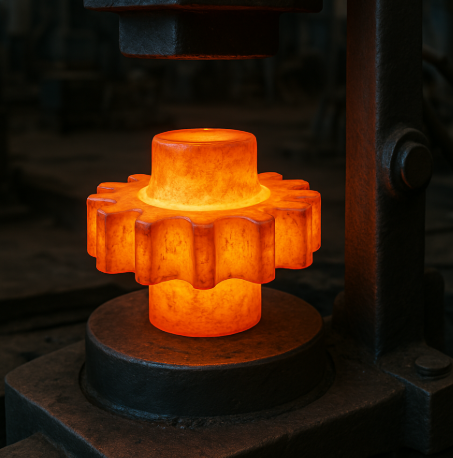
Precision forging
Features:
Precision forging is to improve the dimensional accuracy, surface quality and internal structure of products through more precise control on the basis of conventional forging process. Precision forgings often need no or a small amount of subsequent processing.
Applications:
Precision forging is mainly used in high-end markets with strict requirements on size and shape, such as aerospace, precision machinery, medical equipment and other industries. Commonly used in the manufacture of small complex parts, such as engine parts, instrument accessories, etc. .
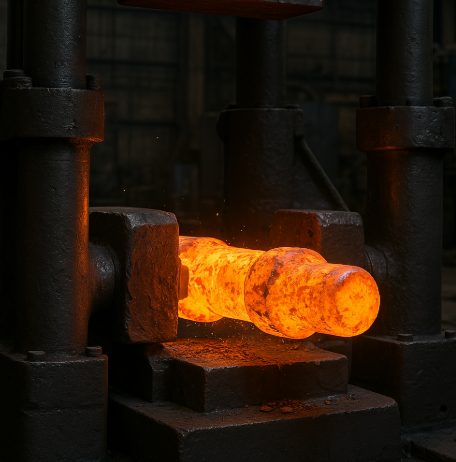
Open die forging
Features:
Open die forging is the use of open-die forging process, usually applied to simpler shapes. Compared with the closed die forging, the die cost is lower, and the process is suitable for small batch production.
Applications:
Suitable for forgings with larger size or irregular shape, such as construction machinery, mining equipment, building materials, etc. .
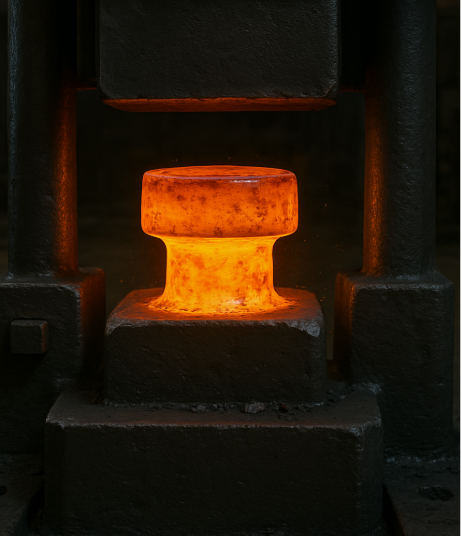
Closed die forging
Features:
Closed-die forging is to put the heated metal blank into the precision die, and the metal is filled into the whole die cavity by the pressure of the hydraulic press or the press to obtain the high-precision forging. This process is suitable for mass production high precision parts.
Applications:
Closed die forging is often used in automobile, aerospace, railway, petrochemical and other industries. Suitable for high-precision, high-strength requirements of parts, such as gears, shafts, flanges and so on.
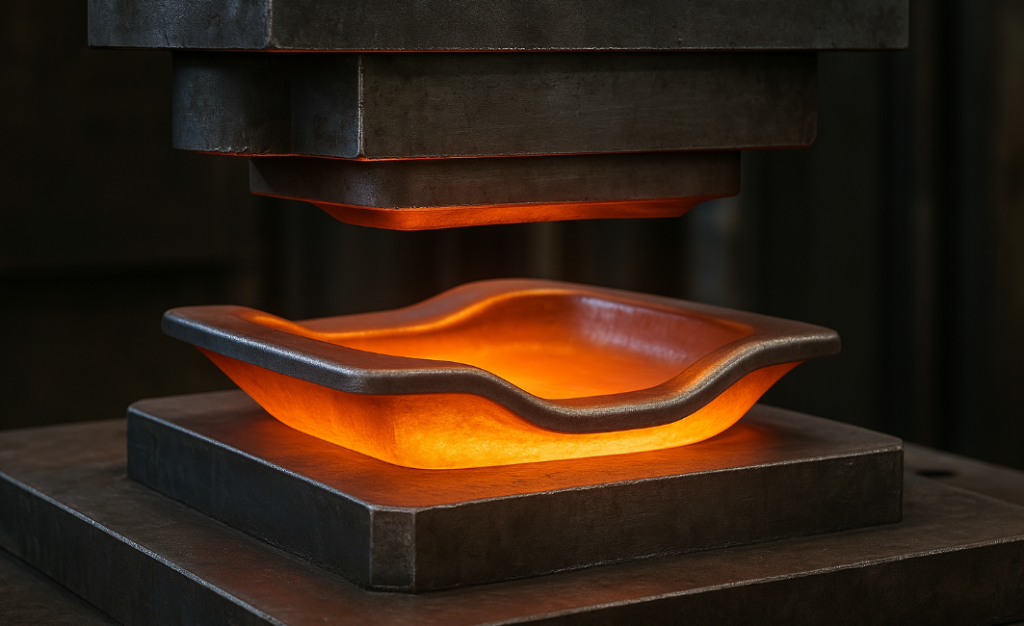
Superplastic forging
Features:
Superplastic forging uses the superplastic characteristics of metal at a specific temperature and strain rate to carry out forming process. This process can produce extremely complex shapes, and the internal structure of the parts is more uniform.
Applications:
Mainly used in aerospace field, especially for complex parts with high requirements such as aero-engine, Turbine Blade, etc. .
In Summary
Different metal forging processes are widely used in different industries and application fields because of their characteristics and adaptability. Selecting the appropriate forging process can improve the production efficiency, reduce the cost, and ensure the mechanical properties and quality of the parts.
The Process Flow & Duration Estimation
The production process of metal forging parts is accurate and efficient, ensuring that each part can meet the strict requirements of customers. Our manufacturing process consists of the following key steps:
Step 1:Material selection
Select the appropriate metal raw materials, usually steel, aluminum alloy, copper alloy, etc. according to customer requirements and product performance requirements, select different metal materials.
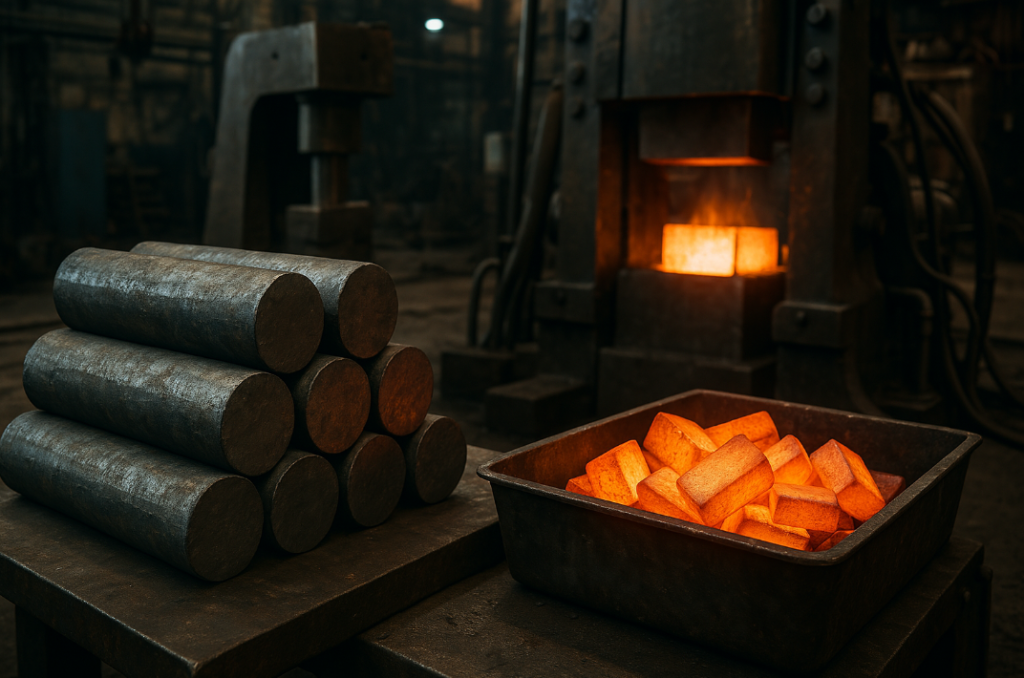
Step 2:Heat up
The metal raw material is heated to a suitable temperature so that it has enough plasticity for subsequent forging. Different materials are heated at different temperatures, usually between 600 °C and 1200 °C.
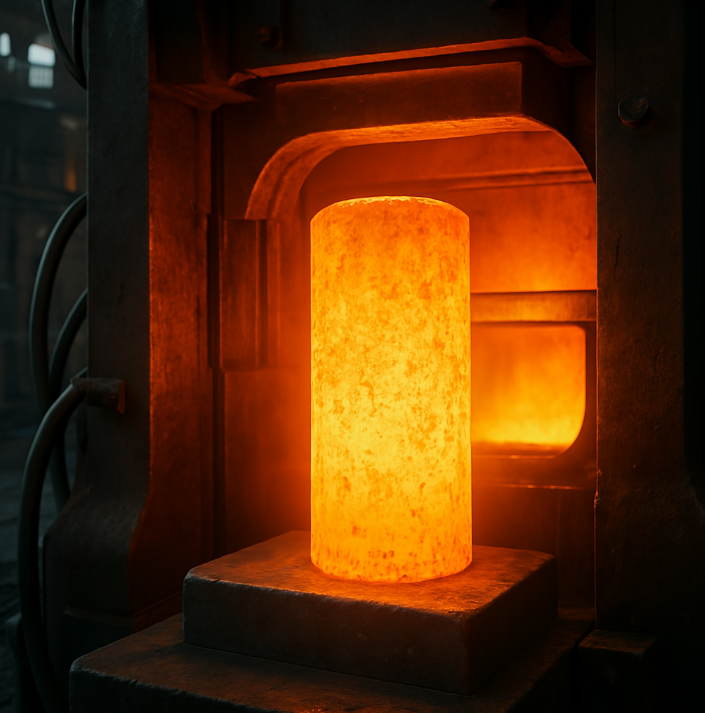
Step 3: Forging
The heated metal is placed in a forging die and shaped by mechanical force or pressure. Common forging methods include:
Free forging: shaping of metal blanks by direct action of a hammer or press.
Die forging: metal into a closed mold, the use of the shape of the mold on the metal pressure for shaping.
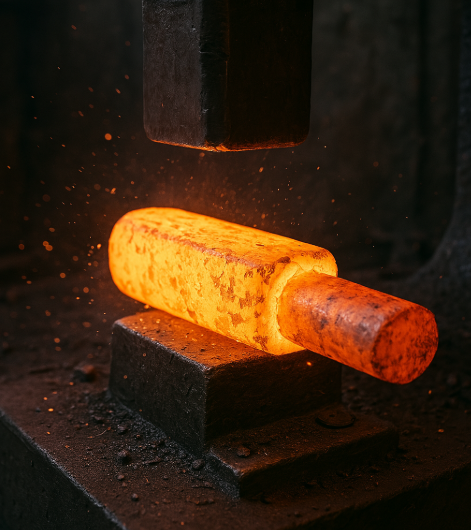
Step 4: Cooling
After forging, the metal parts need to be cooled. The cooling rate can be controlled according to the nature of the metal and requirements, cooling process can be used air cooling, water cooling and other methods.
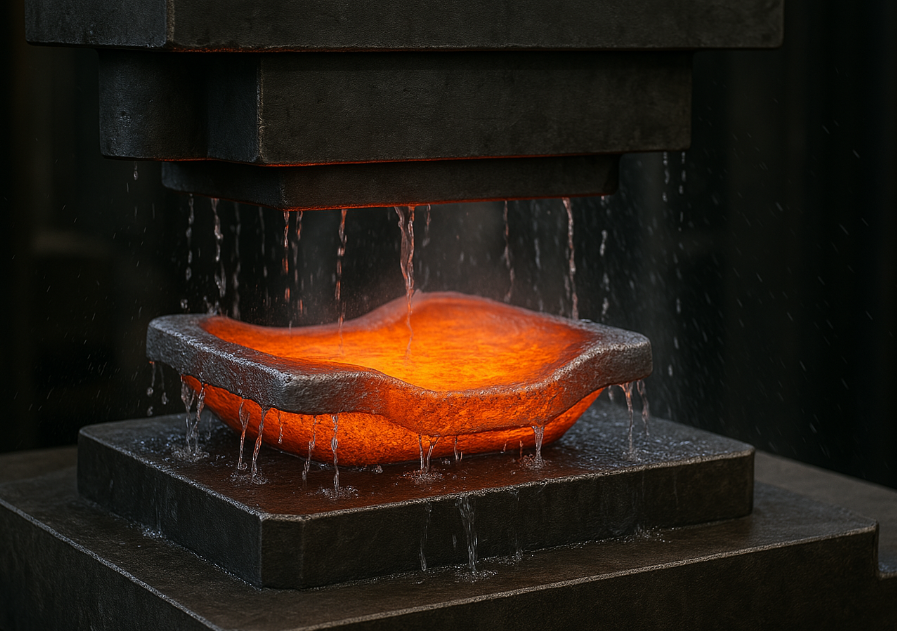
Step 5: Post-processing
In order to eliminate the internal stress and improve the microstructure of the metal, the forgings need to be treated after cooling. Common post-processing methods include:
Annealing: Slow cooling after heating to a certain temperature to reduce the hardness and brittleness of the metal.
Normalizing: Heating to high temperature and then air cooling to improve the structure and properties of metal.
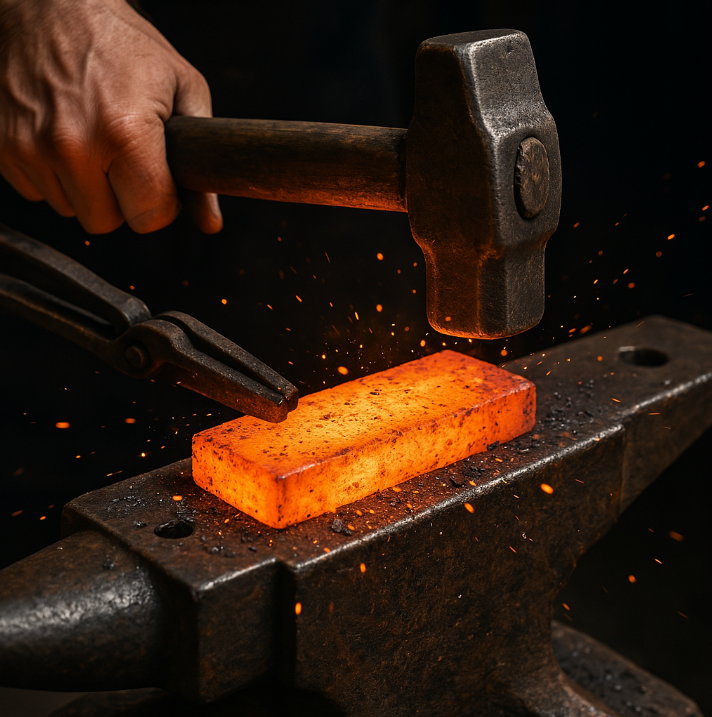
Step 6:Machining
After the forgings have been post-treated, finishing may be required. This includes turning, milling, grinding, etc. to ensure that the product dimensions, Surface finish, etc. meet the requirements.
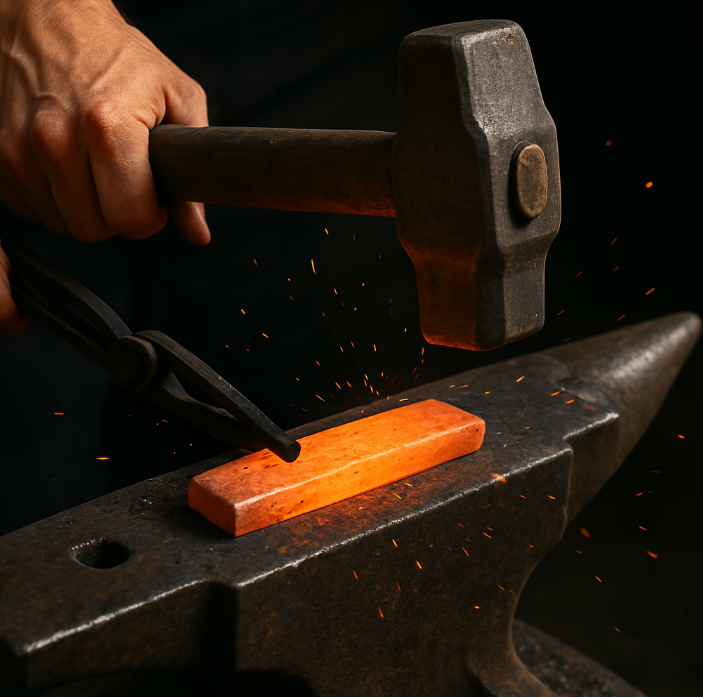
Step 7:Inspection and testing
Carry out strict quality inspection and performance test on the forgings, including size inspection, hardness test, mechanical property test, etc. , to ensure that the products meet the design requirements.
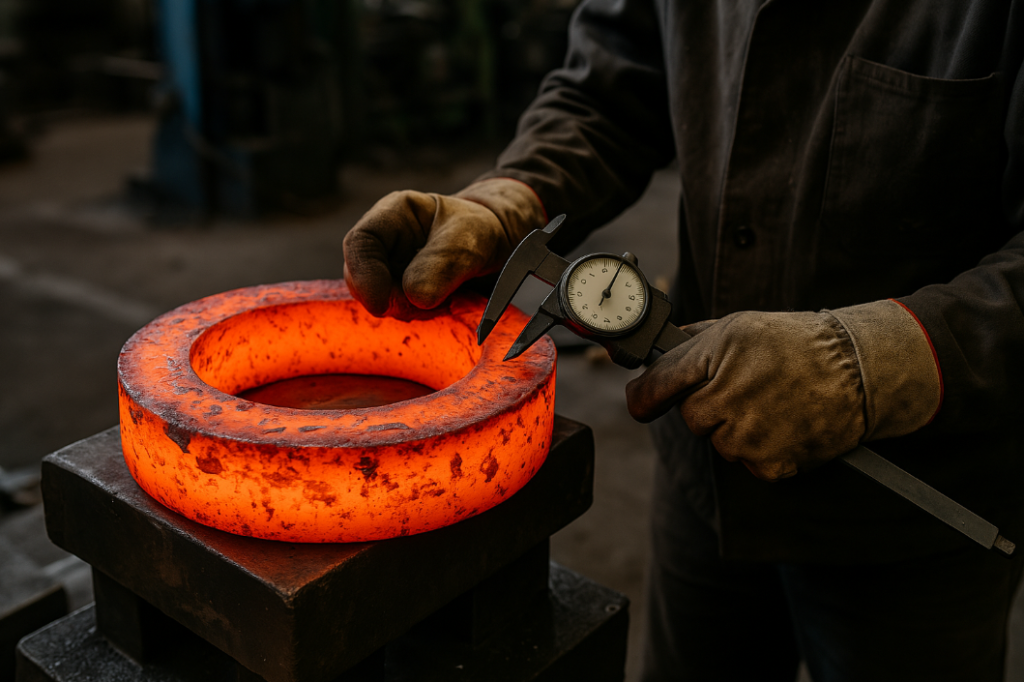
Step 8:Surface treatment
If necessary, forgings may also be surface treatment, such as spraying, galvanizing, heat treatment, etc. to enhance its corrosion resistance, wear resistance and other properties.
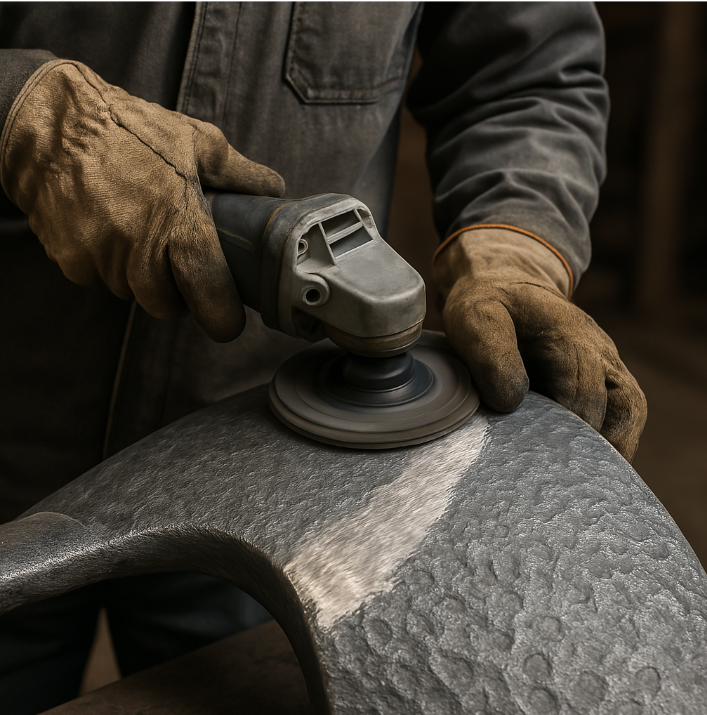
Step 9:Packaging and delivery
After completion of all processes, the metal forgings will be packaged to ensure that they are not damaged during transportation for final delivery to the customer.
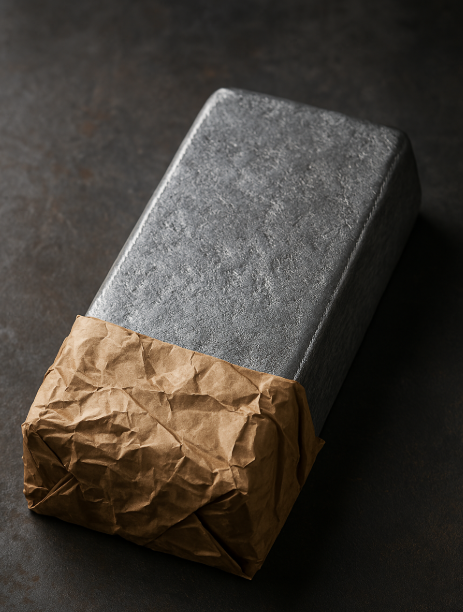
Step 10: Delivery of finished product
Upon completion of all inspection and post-processing, the castings will become the final product, ready to be delivered to the customer or used for assembly.
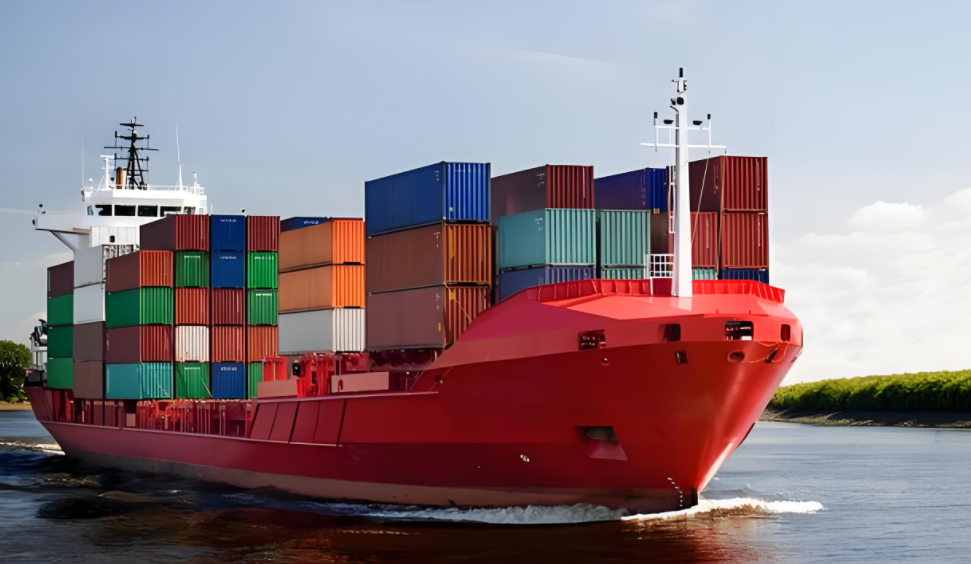
Want to know how to compress lead times?
In order to shorten the production and delivery cycle, we suggest that you tell us your needs in detail, and we will adjust the strategy flexibly according to your requirements to ensure your production and help you succeed!
The Common Pitfalls When Purchasing
Please note that the final cost depends on the customized service you require, the specifications of the raw materials used, the relevant national laws, and the distance of transportation. Take the example of booking a tall container of products:
- Improper selection of materials: Improper selection of materials may lead to forgings can not reach the strength, corrosion resistance and other performance requirements, affecting the service life.
- Poor design: An immature design can lead to forging difficulties, increased costs, and delivery delays.
- Supplier is not reliable: Some unprofessional suppliers may not be strict in quality control, resulting in substandard products or delivery is not timely.
Materials used in casting
The raw materials for metal forgings mainly include the following:
Steel
- Carbon Steel: For the production of high strength components, commonly used in automotive, aerospace and other industries.
- Alloy Steel: The addition of other alloying elements, such as chromium, nickel, molybdenum, etc. , to improve the material's wear resistance, corrosion resistance and thermal stability.
- Stainless steel: Containing at least 10.5% chromium, with excellent corrosion resistance, widely used in chemical, food processing and other industries.
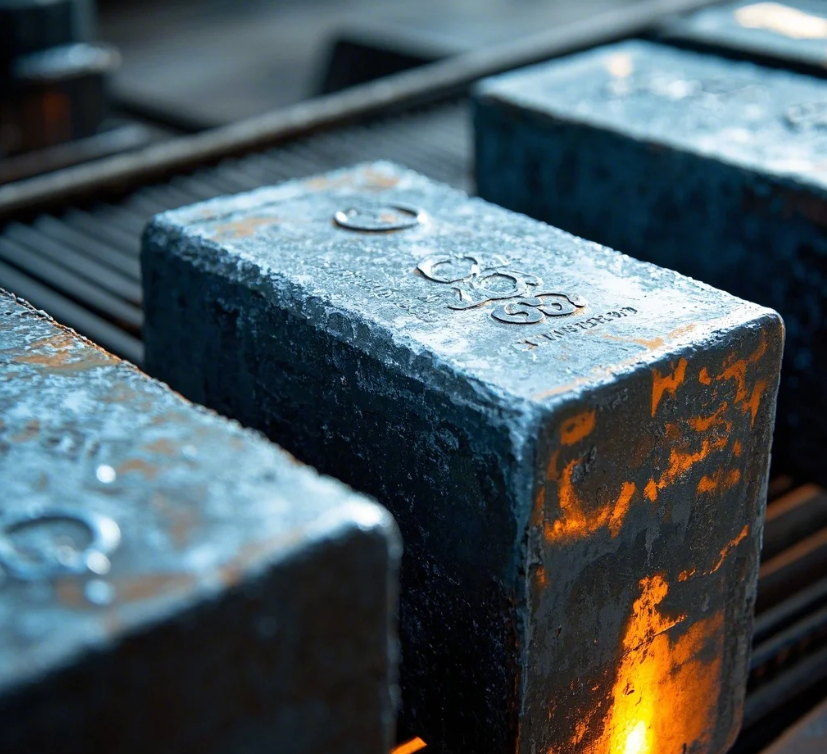
Aluminum
Because of its light weight and strong corrosion resistance, aluminum alloys are widely used in aerospace, automotive and electronic products forgings.
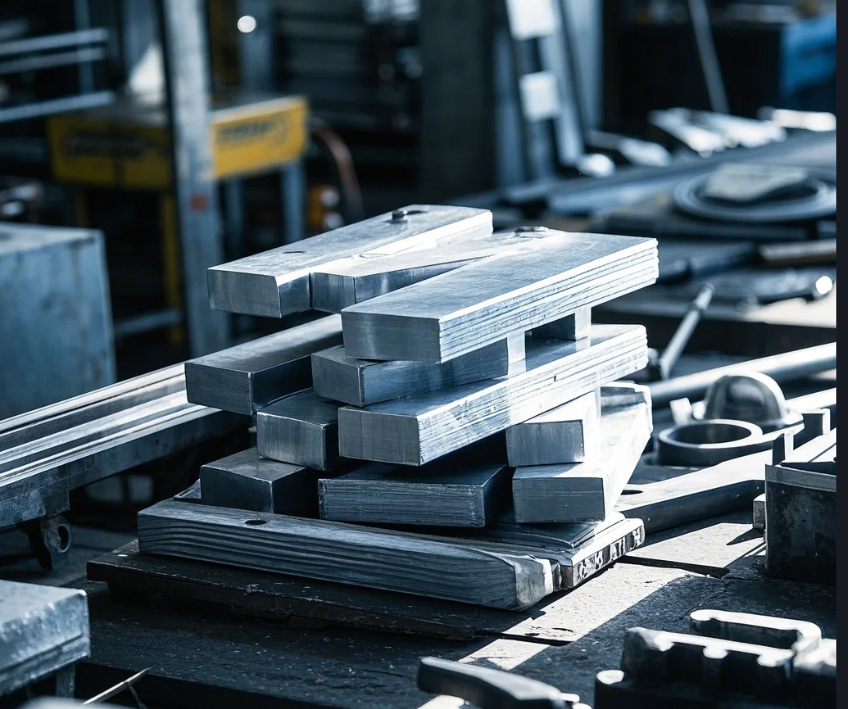
Copper alloy
Copper alloys, including brass, red copper and aluminum bronze, have good electrical conductivity, thermal conductivity and corrosion resistance, and are commonly used in the manufacture of electrical components, pipe fittings, etc. .
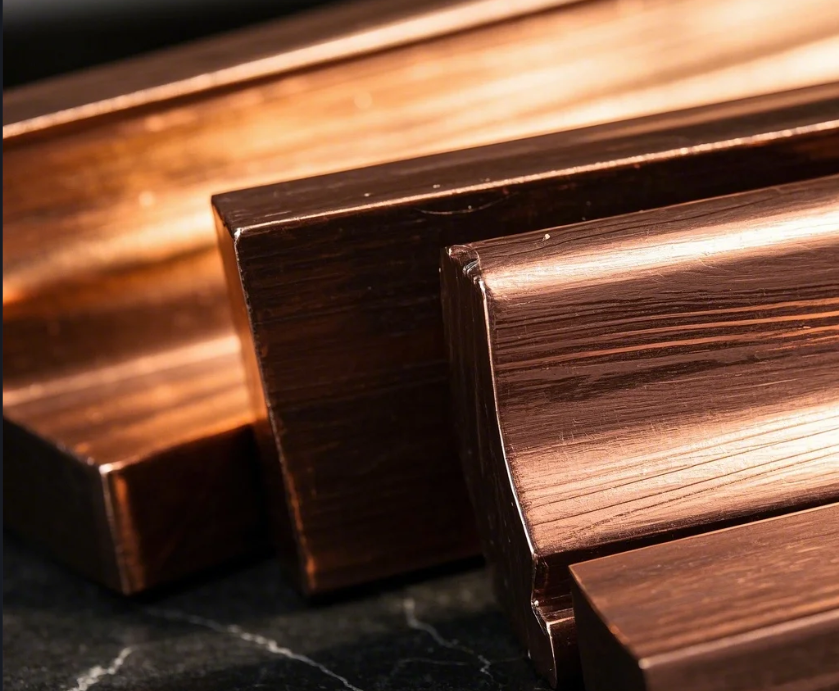
Titanium
The high strength, low density and corrosion resistance of titanium alloys make them ideal materials for aerospace, chemical processing and medical equipment.
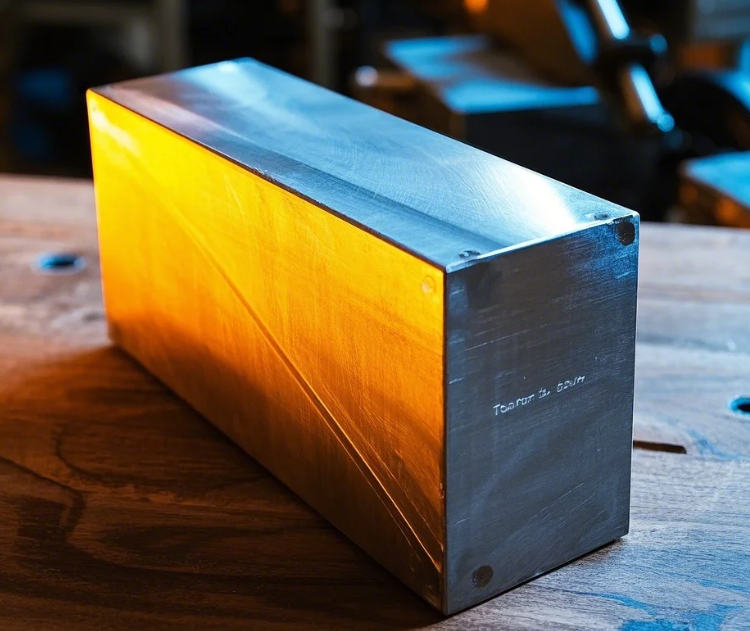
Tool Steel
Tool Steel is a kind of steel with high hardness and wear resistance, which is often used in the manufacture of dies and cutting tools.
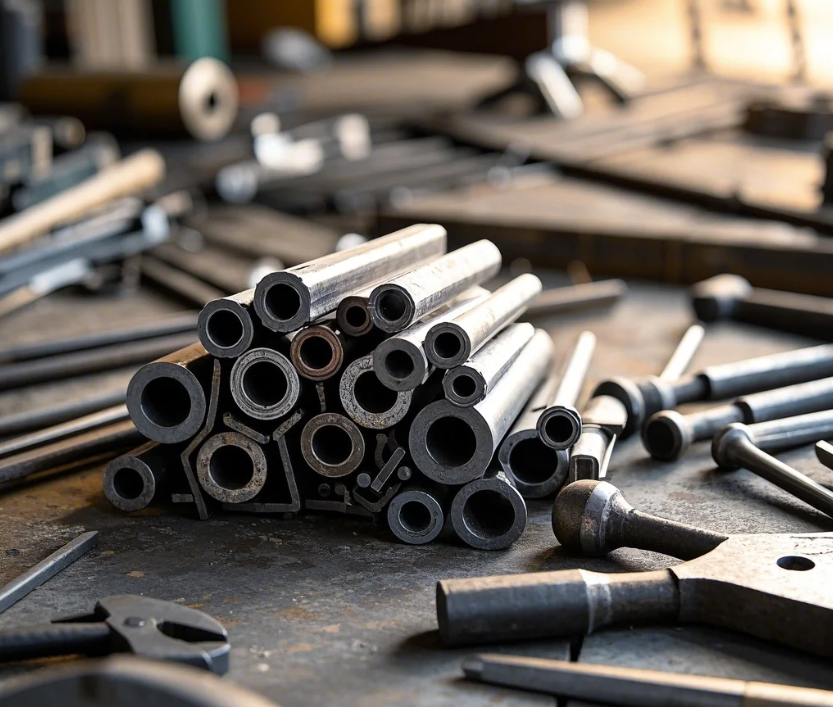
Cast iron
Cast iron has good castability and wear resistance, and is widely used in automobile engine parts and mechanical parts.
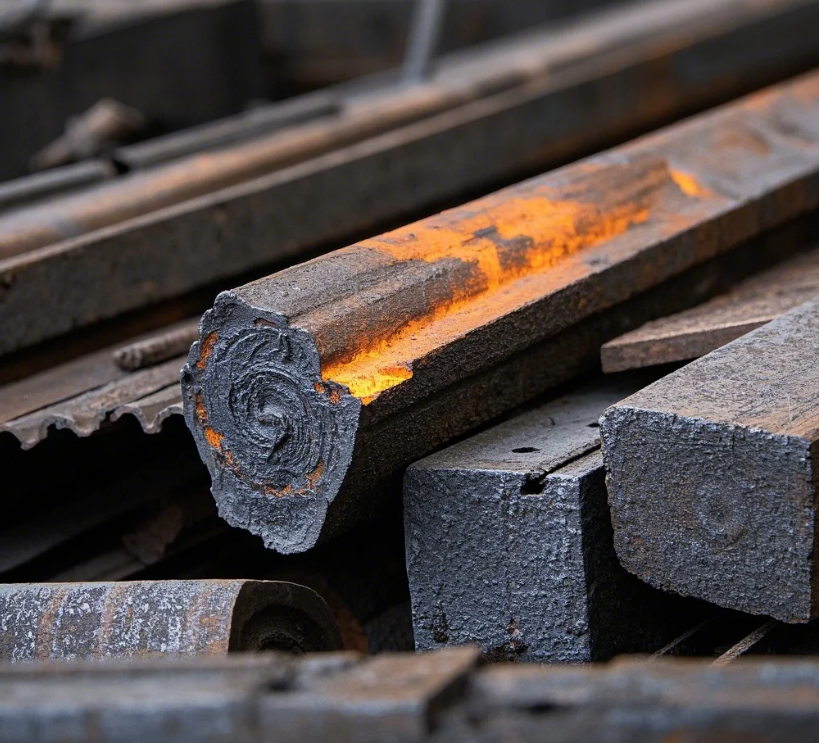
These materials are selected on the basis of the operational requirements, performance requirements and economy of the forging, and are usually subjected to rigorous screening and treatment.
A Brief Self-Nomination, Why Choose Prime?
Choose Us, you will get cost-effective, high-quality, on-time delivery of metal forgings solutions.
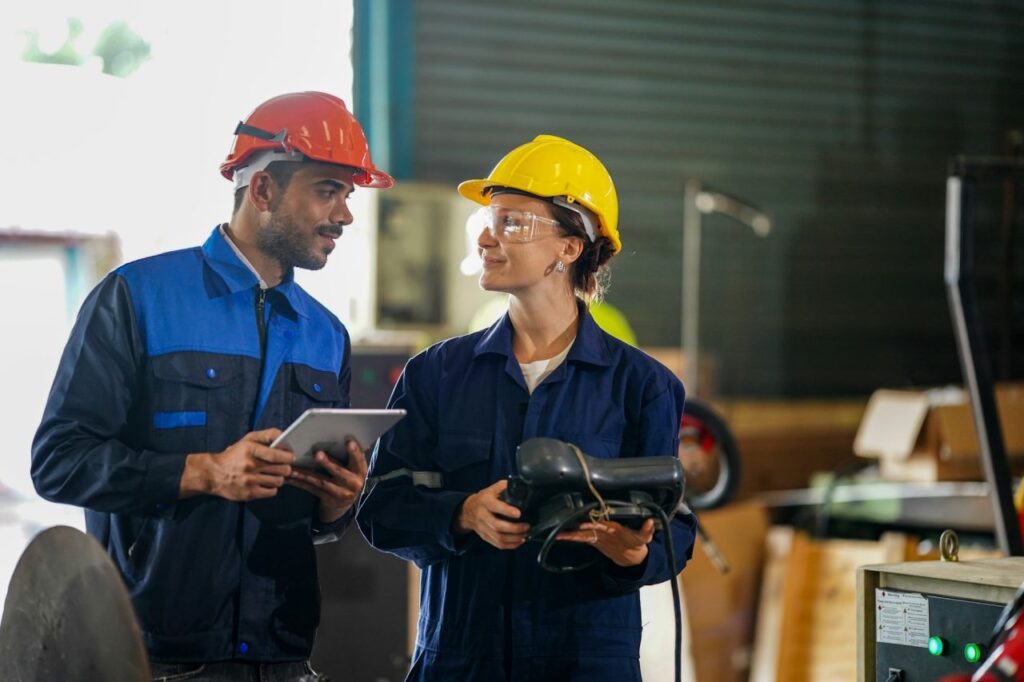
Experience: We have more than 30 years of metal forging production experience, can provide a variety of industries with high-quality custom metal forgings.
Professional team: Our Team of Engineers is familiar with the forging process and can provide precise design and production services.
High quality assurance: We are ISO 9001 certified to ensure that each forging meets the highest standards of quality.
Rapid Response: We are committed to providing fast sample production and production cycle, to ensure that your needs can be met in a timely manner.
Global Services: No matter where you are, we can provide you with quality services to ensure the smooth progress of your business.
Get in touch
Custom Hardware Parts Made Easy
Share detailed information about your needs, including drawings, reference images, and any specific ideas or specifications you have in mind.
Based on your requirements and design, we’ll provide a custom solution and send you a detailed quote within 24 hours.
Once you approve the design and quote, we’ll begin mass production and take care of the shipping, ensuring timely delivery.
Get a Free Quote
Reach out to us for a free quote and expert advice on your custom hardware needs. At Prime, we’ll provide the right solution for your project, ensuring quality and precision every step of the way.