Fasteners of metal
The world's leading supplier of metal fasteners.
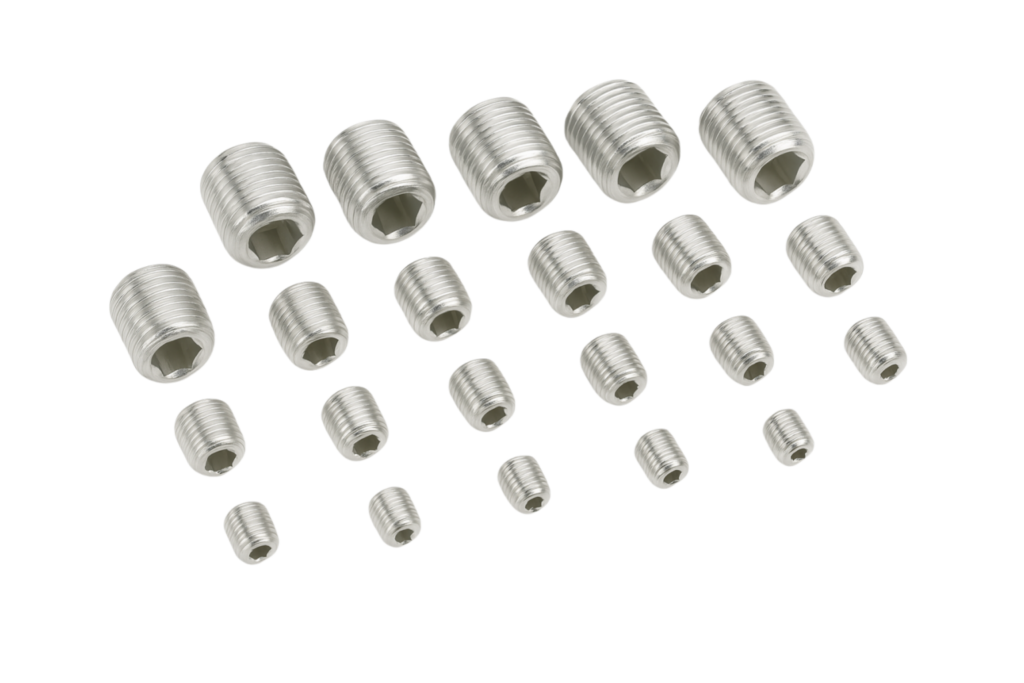
Custom made metal fasteners
In industrial manufacturing, construction engineering, car assembly and other fields, every detail is related to the overall performance and safety. We provide high-quality custom metal fasteners, precisely designed according to your needs, to ensure that every screw, nut, bolt are perfect fit, for your projects to provide super-strong tightening force and durability.
Table Of Contents For This Page
At Prime, we provide you with professional service and high-quality products.
Application fields of customized metal fasteners
Metal fasteners are widely used in many industries, including automotive, aerospace, construction, electronics, home appliances and industrial equipment. Custom metal fasteners provide a reliable solution for high-load environments requiring high-strength connections, as well as for small components in sophisticated electronics.
General Hot Selling Products
Metal fasteners can be divided into several main types according to different processes, and each process has different characteristics and application fields. The following are some common fastener processes and their features and applications:
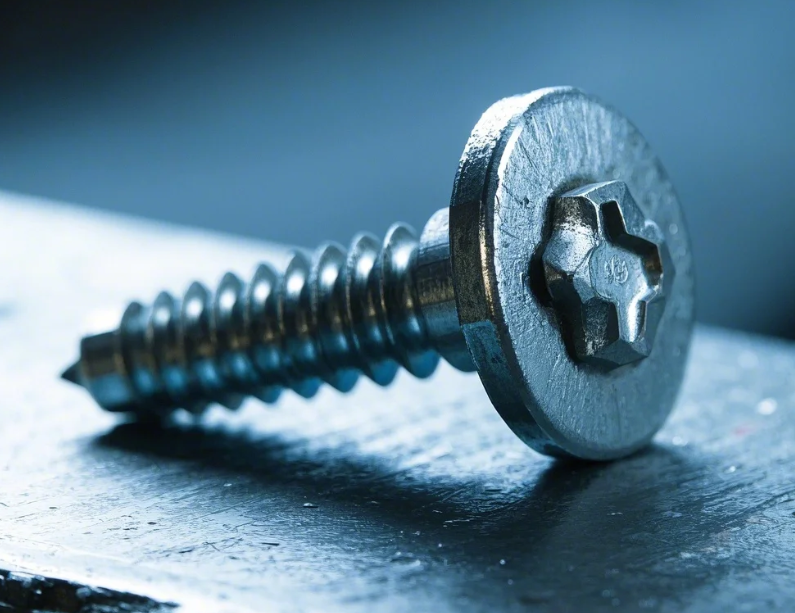
Screws
- Features:
- High precision: Precise screw thread ensures the perfect combination with the mating parts.
- Corrosion resistance: Through surface treatment (such as zinc plating, chromium plating, etc.) , screws can adapt to various environments, corrosion resistance.
- High Strength: The use of high-strength materials (such as stainless steel, carbon steel) , adapt to high load or vibration environment.
Applications:Widely used in electronic equipment, automobile manufacturing, mechanical equipment, construction and other fields, especially for the need for high-strength connection industries.
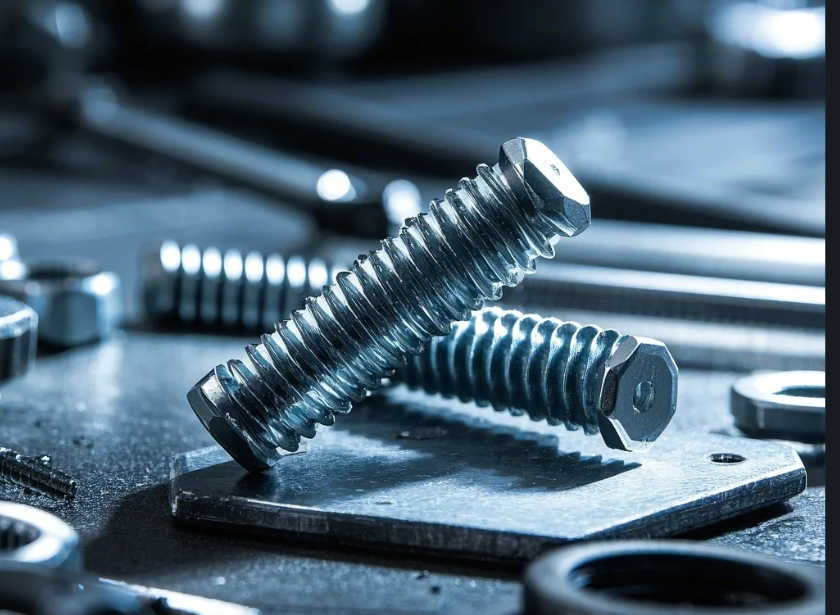
Nuts
- Features:
- Strong tightness: The nut and the bolt match closely, provides the stable connection.
- Durability: The use of high-quality metal materials, high temperature resistance, corrosion resistance, suitable for a variety of industrial environments.
- Wide Adaptability: It can cooperate with bolts and screws of various specifications and flexibly adapt to different needs.
Applications:Commonly used in mechanical assembly, automotive industry, building structures, home appliances, equipment and other fields, especially suitable for the need to firmly fasten the environment.
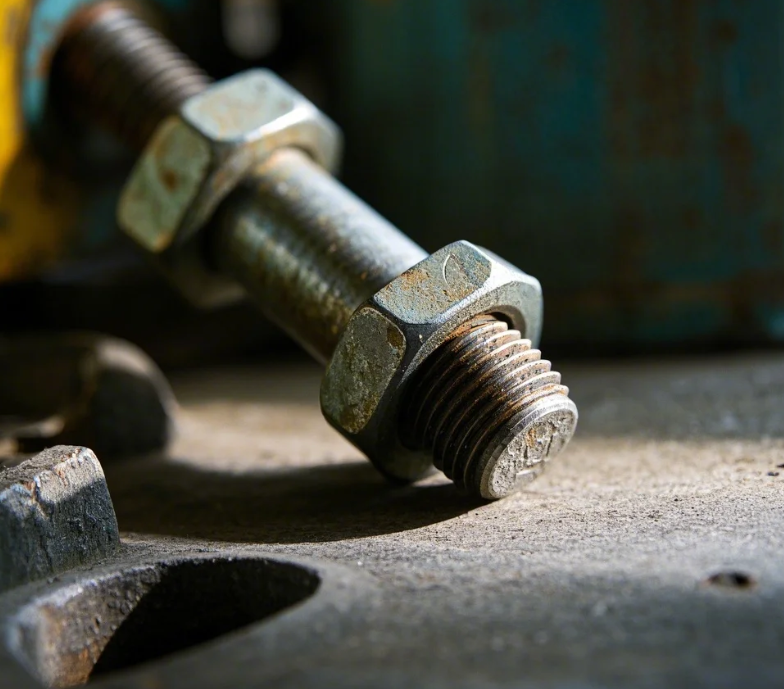
Bolts
- Features:
- High Strength: The bolts produced by forging process have very high mechanical strength and are suitable for heavy equipment.
- Corrosion resistance: Zinc plating, chromium plating and other surface treatment can significantly improve the corrosion resistance of bolts, to adapt to extreme working conditions.
- High Reliability: Through strict quality testing to ensure the safety and stability of each bolt in use.
Application:Common in heavy machinery, building structures, bridge construction, energy fields and other high-intensity demand scenarios, especially for long-term use of the connection point.
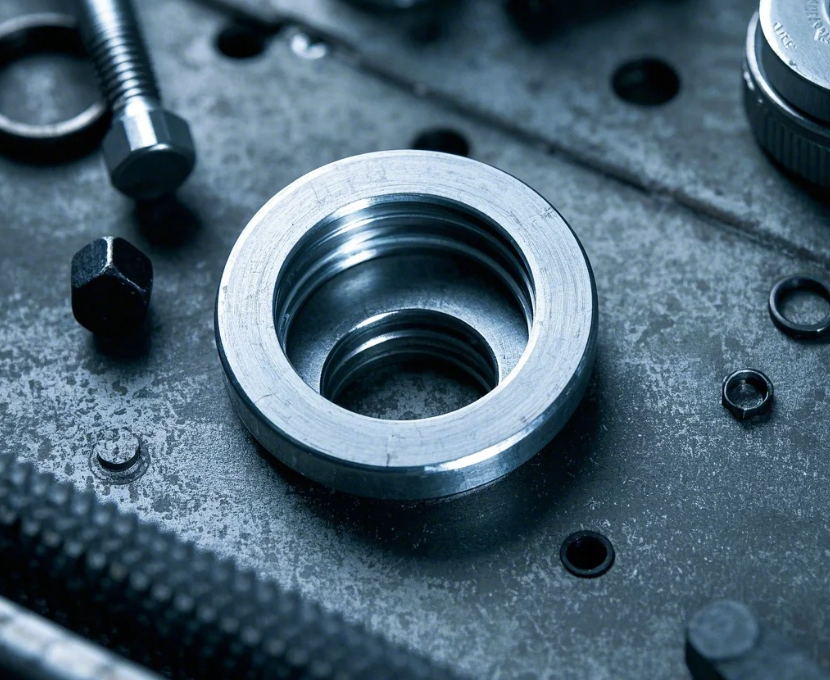
Washers
- Features:
- Shock absorption and compression resistance: The gasket can effectively disperse the pressure, slow down friction and wear, and prolong the service life of the fasteners.
- Prevent loosening: Can be increased by friction to prevent connectors in the use of the process due to vibration and loosening.
- Strong corrosion resistance: Through material selection and surface treatment, washers can be used in corrosive environments.
Application:Widely used in automobiles, mechanical equipment, electrical devices and other fields, especially in high vibration environment, to prevent fasteners loose and wear.
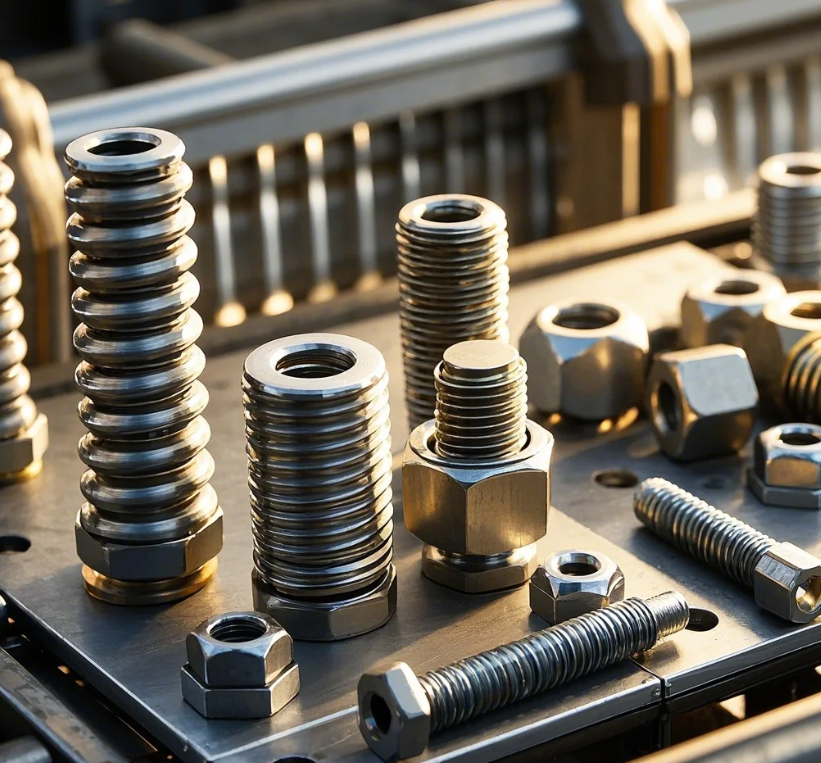
Fasteners of custom shape and size
- Features:
- Highly customized: Customized according to customer needs, to ensure that the specific work environment and design requirements.
- Strong diversity: According to different application needs, the production has a special shape, function or bearing capacity of fasteners.
- High Performance: By selecting the right materials and process, custom fasteners can achieve superior performance over standard products.
Applications:Widely used in special industrial needs, such as aerospace, medical equipment, electronics and other high-precision requirements of the field.
In Summary
Each customized metal fastener product has its unique process and characteristics, which can meet the needs of different industries and application scenarios. Selecting suitable products can not only improve the stability and safety of the project, but also ensure long-term efficient operation. Through customized services, we can provide customers with more accurate solutions to ensure the smooth progress of each project.
The Process Flow & Duration Estimation
The production process of metal fasteners is a precise engineering involving multiple steps, each of which is crucial to ensure the quality and performance of the final product. The following are the main steps in the production of metal fasteners:
Step 1: Preparation of raw materials
The production of metal fasteners begins with the sourcing of high-quality raw materials. Common raw materials include stainless steel, carbon steel, aluminum alloy, etc. . These materials are usually subjected to a rigorous screening process to ensure that they meet the required specifications and standards.
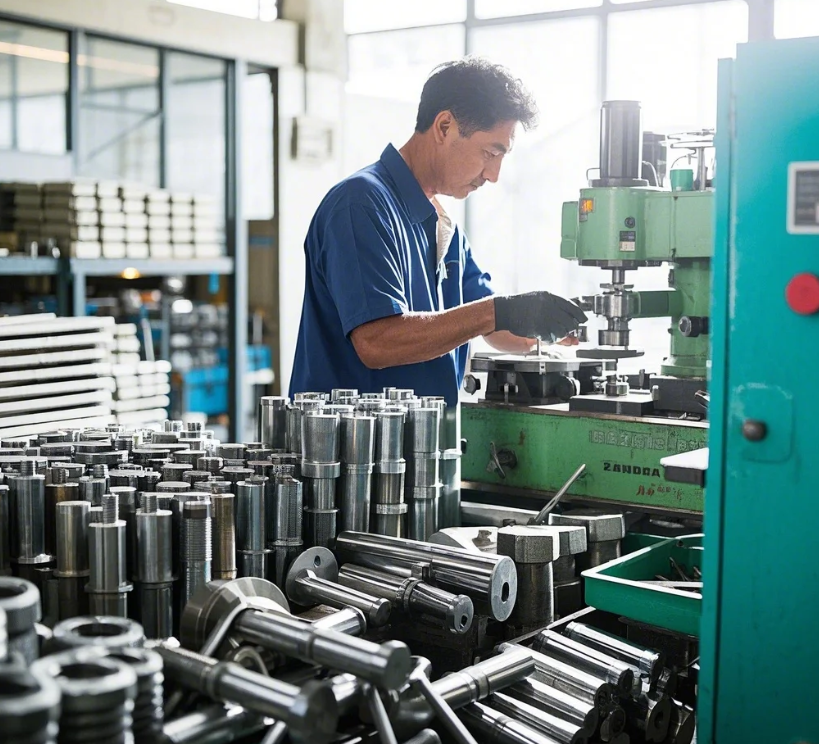
Step 2: Cutting and shaping
In this step, the raw material is cut to the desired length or shape. Cutting is usually done mechanically or by laser to ensure accuracy and consistency. Subsequently, the material is fed into forming equipment, such as stamping machines, thread rolling machine, etc. , a preliminary molding treatment.
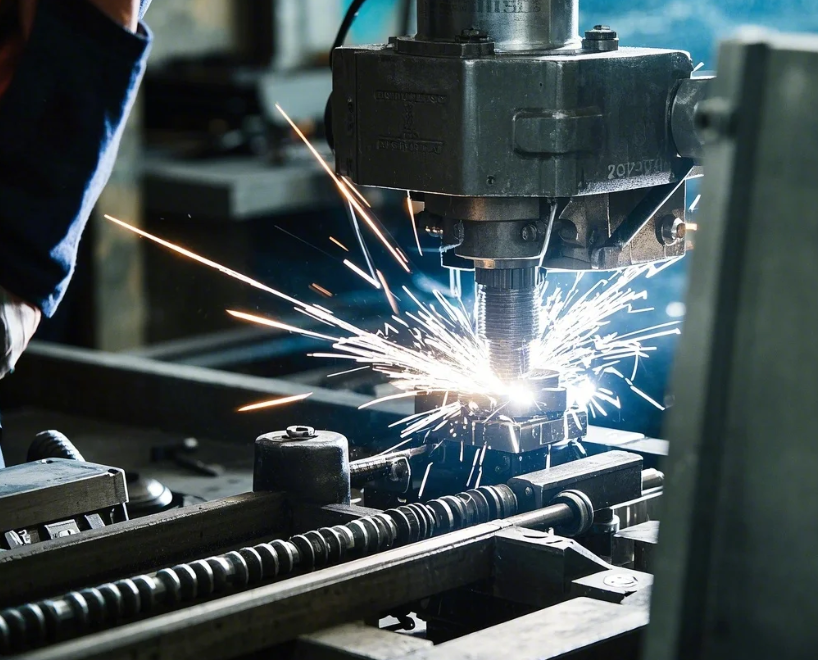
Step 3: Heat Treatment
In order to improve the strength and durability of metal fasteners, many metal materials need to be heat treated. The heat treatment process includes heating, quenching and tempering to change the structure of the material and improve its hardness and tensile strength.
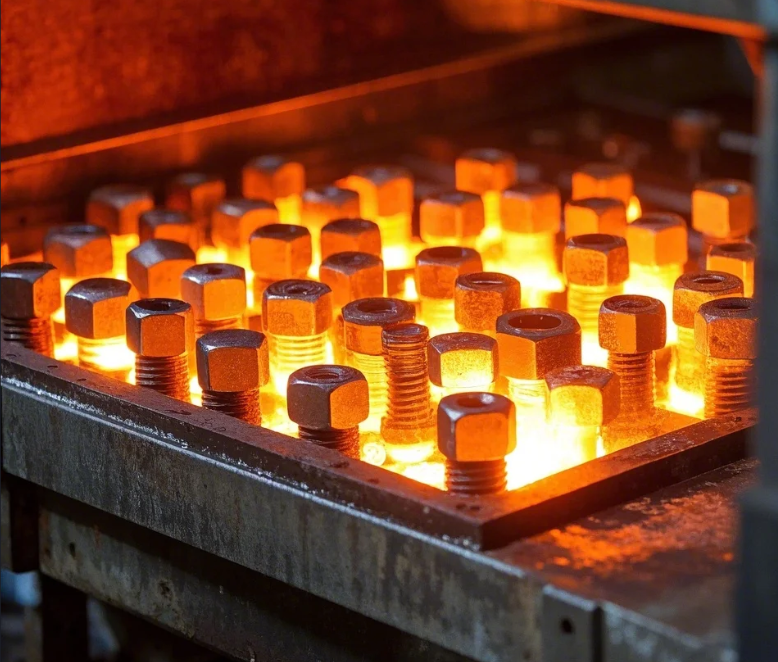
Step 4: Surface treatment
In order to enhance the corrosion resistance and aesthetics of metal fasteners, surface treatment is essential. Common surface treatment methods include zinc plating, plastic spraying, phosphating, electroplating and so on. These treatments can effectively prevent metal surface rust or wear, and prolong service life.
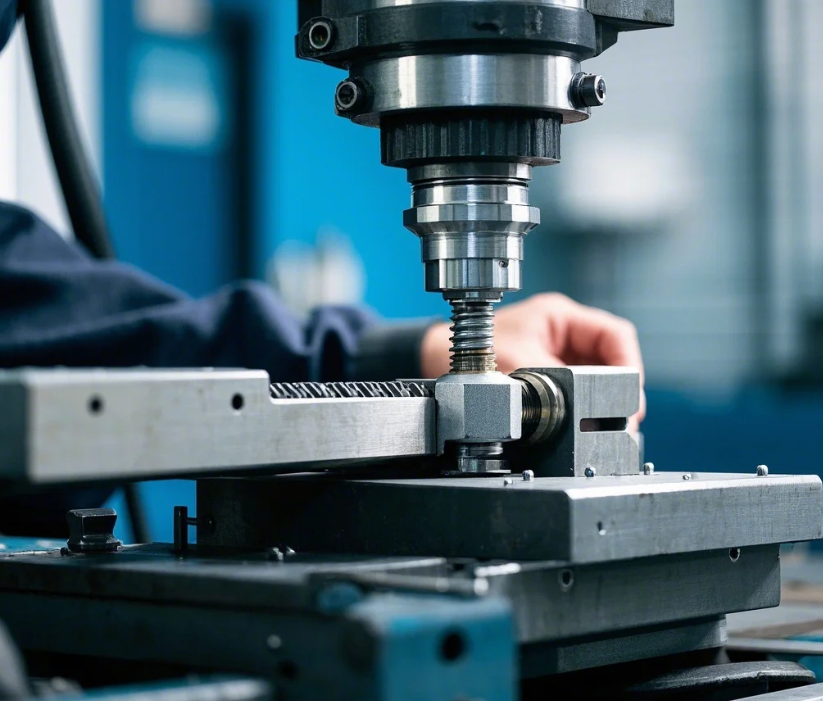
Step 5: Machining and cutting
After heat treatment and surface treatment, metal fasteners into the finishing stage. This stage includes thread processing, hole processing, end trimming, etc. , to ensure that the size of fasteners and threads meet the design requirements.
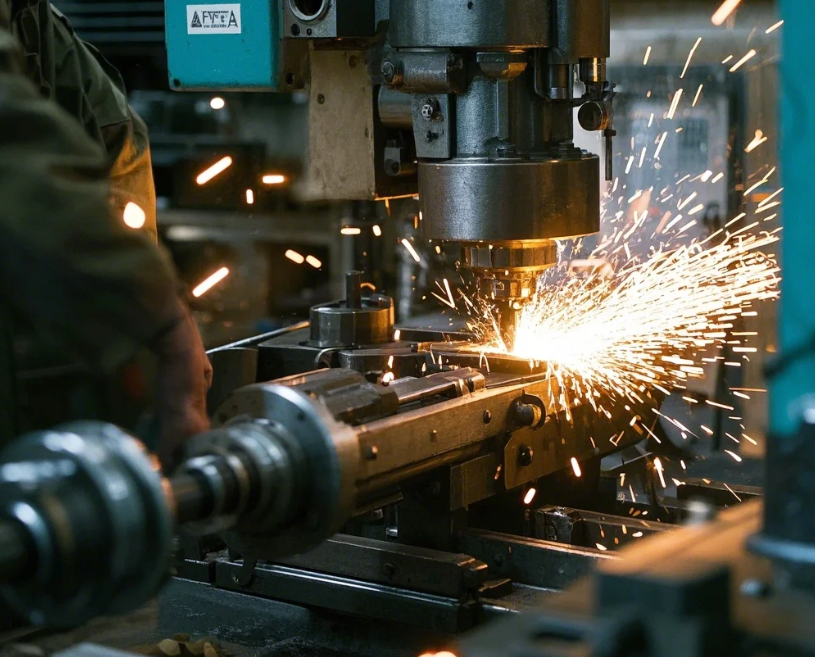
Step 6: Quality inspection
In the production process, strict quality control is an indispensable link. Each batch of production will be subject to detailed inspection, including dimension, strength, thread accuracy, surface quality and other aspects of testing to ensure that the products meet international quality standards.
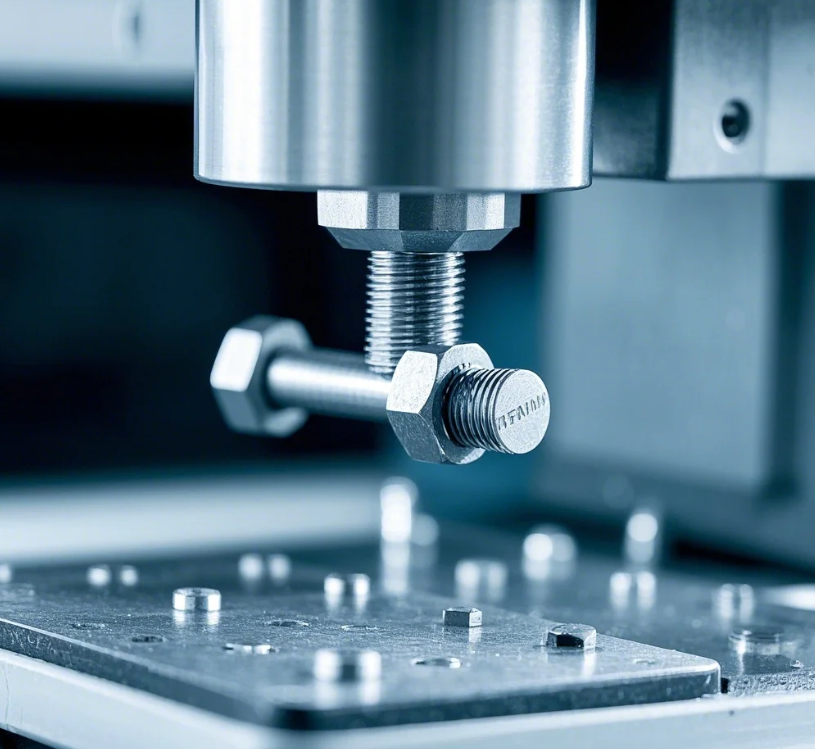
Step 7: Packaging and shipping
After all production and inspection work is completed, the metal fasteners are cleaned, packed and ready for shipment. According to customer requirements, fasteners can be classified and packaged by batch, model, size, etc. to ensure safety and convenience during transportation.
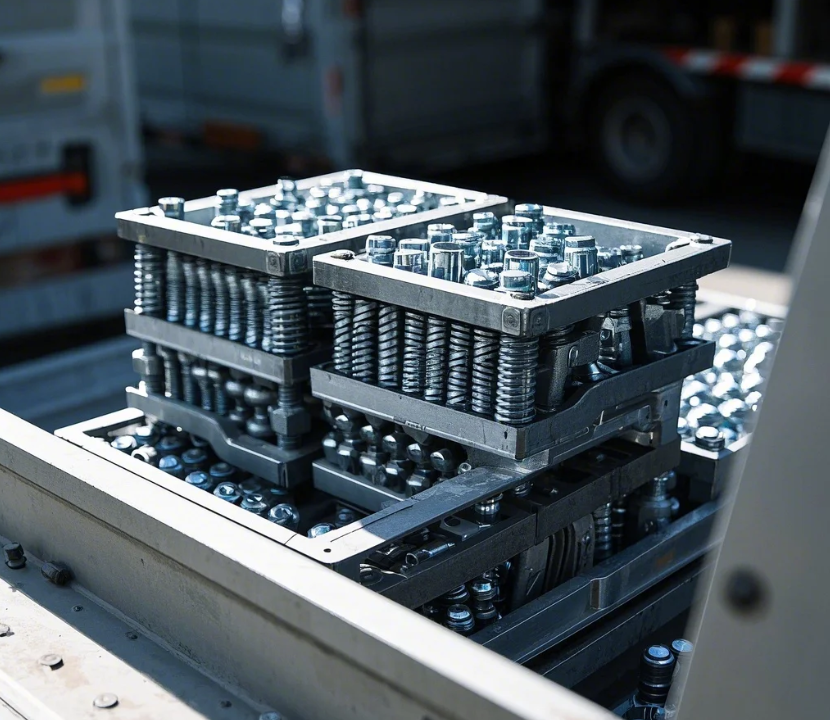
Step 8: Delivery of finished product
Upon completion of all inspection and post-processing, the castings will become the final product, ready to be delivered to the customer or used for assembly.
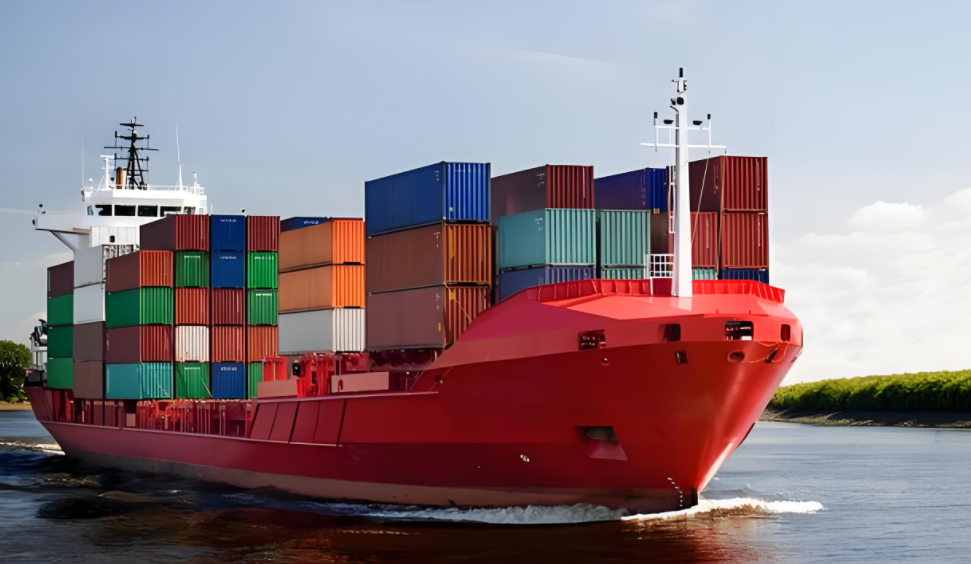
Want to know how to compress lead times?
In order to shorten the production and delivery cycle, we suggest that you tell us your needs in detail, and we will adjust the strategy flexibly according to your requirements to ensure your production and help you succeed!
The Common Pitfalls When Purchasing
Please note that the final cost depends on the customized service you require, the specifications of the raw materials used, the relevant national laws, and the distance of transportation. Take the example of booking a tall container of products:
- Improper material selection: improper material selection may lead to fasteners can not reach the strength, corrosion resistance and other performance requirements, affecting the service life.
- Poor design: immature design can lead to fastener production difficulties, increased costs, and delivery delays.
- Supplier is not reliable: some unprofessional suppliers may not be strict in quality control, resulting in substandard products or delivery is not timely.
Materials used for metal fasteners
Metal fasteners generally use the following materials:
Carbon Steel
Commonly used in manufacturing bolts, screws, nuts and other fasteners. It has good mechanical properties and wear resistance, but in some environments may need to be galvanized to improve corrosion resistance.
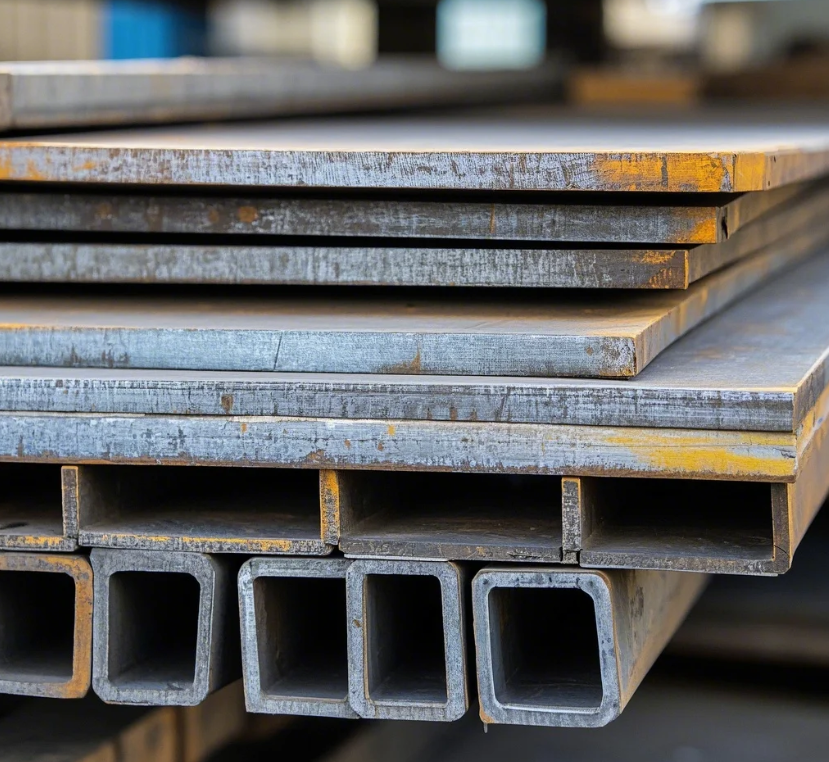
Stainless steel
This material has excellent corrosion resistance and oxidation resistance, suitable for outdoor or wet environment fasteners. Common types include 304 and 316 stainless steel.
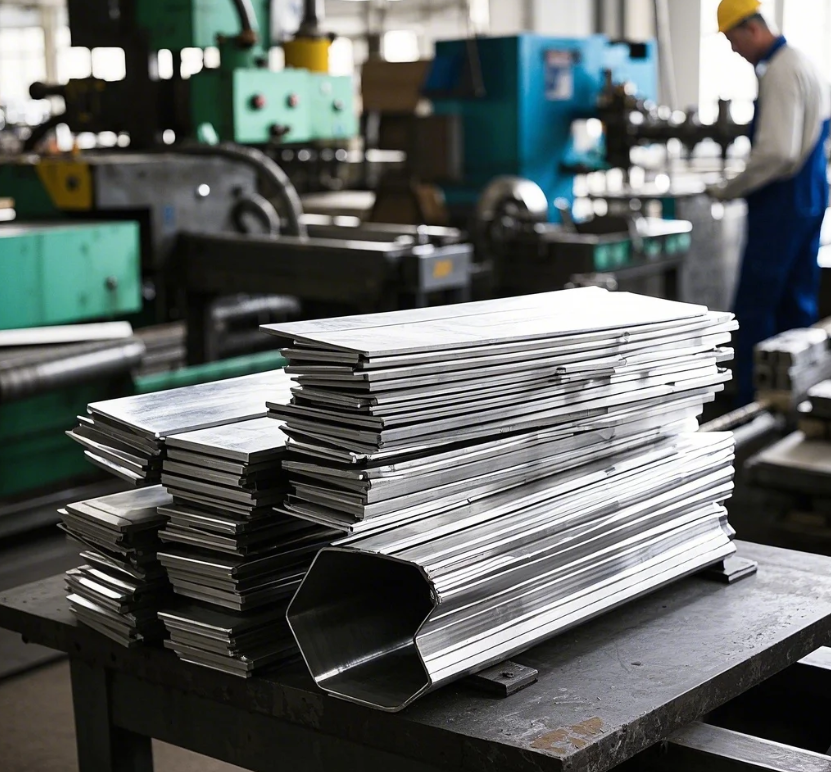
Alloy Steel
Alloy steels (e. g. chrome-molybdenum) perform well under high strength and high temperature conditions and are often used for fasteners with high loads or special requirements.
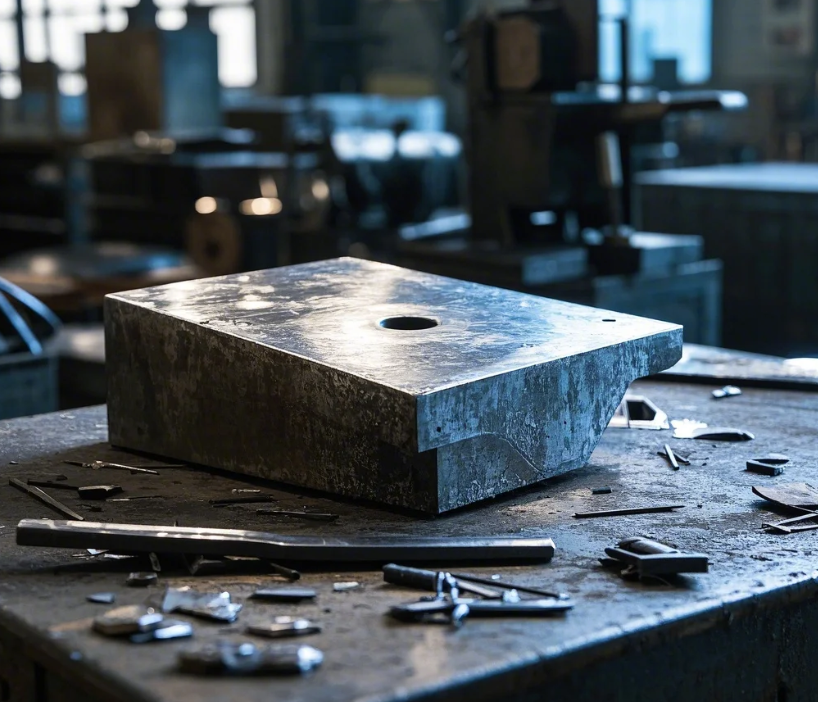
Aluminum
Aluminum fasteners are relatively lightweight and are commonly used in weight-critical applications, such as aerospace.
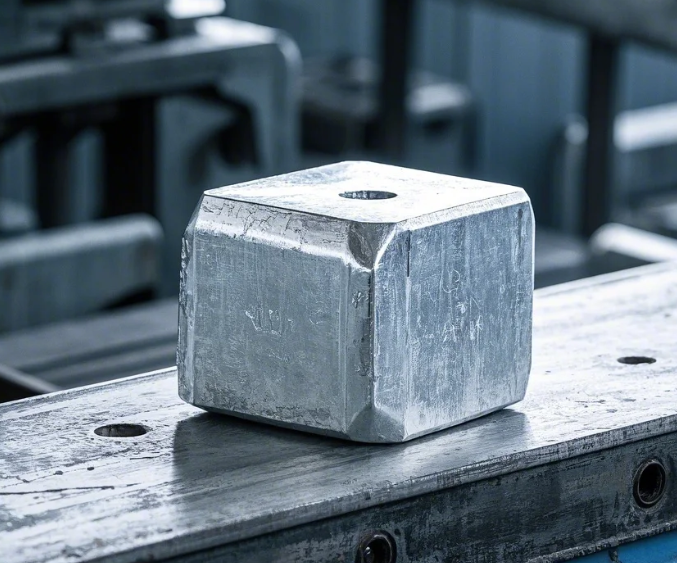
Copper and brass
Copper and brass have good electrical conductivity and corrosion resistance, often used in the electronics industry or wet environment.
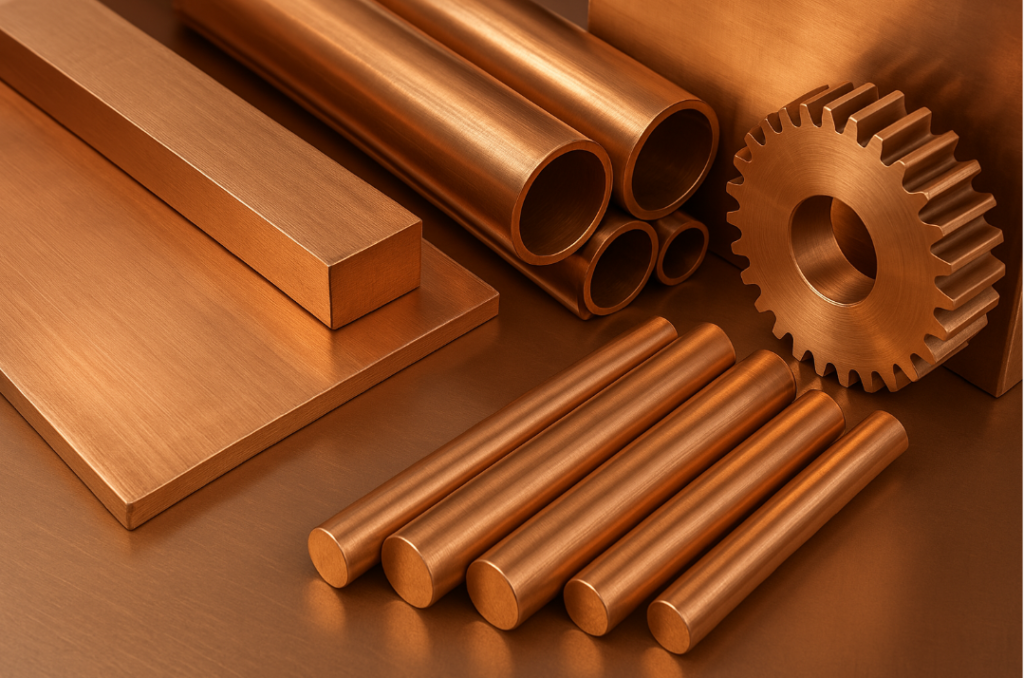
Zinc alloy
Has high corrosion resistance, often used in the automotive and home appliances industry.

Plastic
Sometimes heat-resistant or special-performance plastic materials, such as nylon, are used for nonmetallic fasteners, especially where lightness, insulation, or corrosion resistance are required.
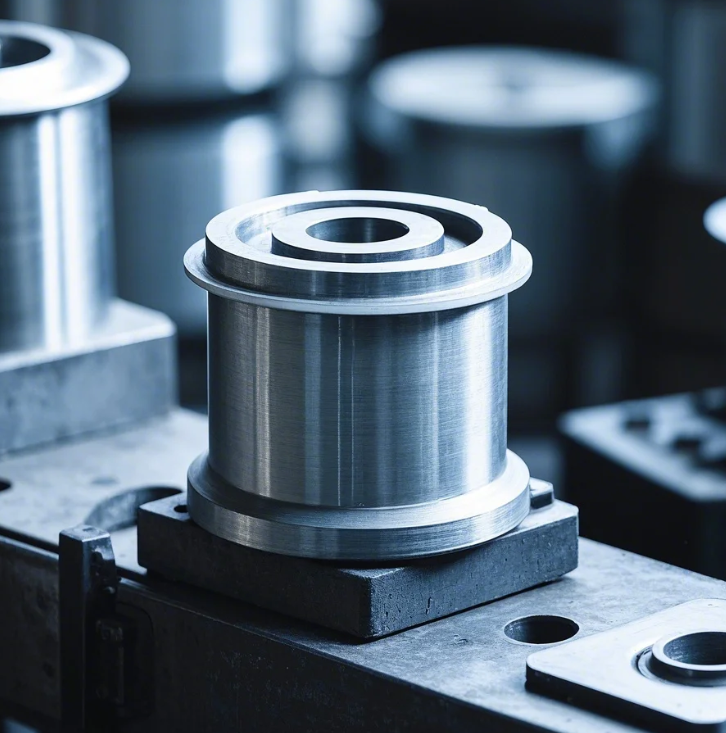
Different materials are suitable for different application scenarios, and it is very important to select the appropriate material according to the specific needs.
A Brief Self-Nomination, Why Choose Prime?
Choose Us, and you will get affordable, high-quality, on-time delivery of metal fasteners solutions.
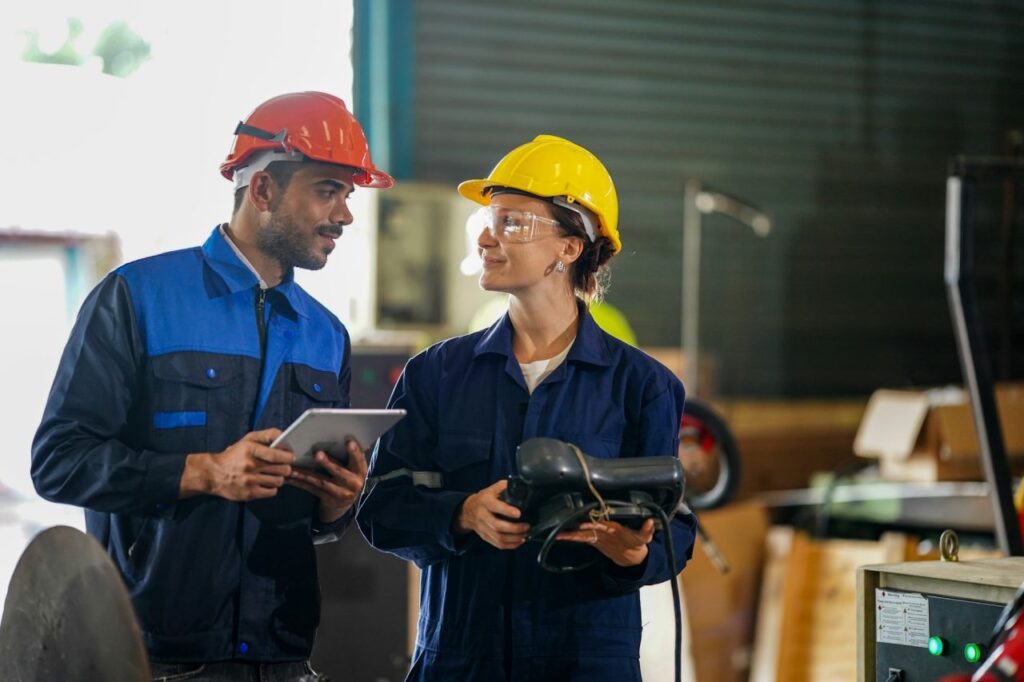
Experience: We have more than 30 years of metal fastener production experience, can provide high-quality customized metal fasteners for various industries.
Professional team: Our Engineering team is familiar with metal fastener technology and can provide precise design and production services.
Quality assurance: WE are ISO 9001 certified to ensure that each fastener meets the highest standards of quality.
Rapid Response: We are committed to providing fast sample production and production cycle, to ensure that your needs can be met in a timely manner.
Global Services: No Matter where you are, we can provide you with quality services to ensure the smooth progress of your business.
Get in touch
Custom Hardware Parts Made Easy
Share detailed information about your needs, including drawings, reference images, and any specific ideas or specifications you have in mind.
Based on your requirements and design, we’ll provide a custom solution and send you a detailed quote within 24 hours.
Once you approve the design and quote, we’ll begin mass production and take care of the shipping, ensuring timely delivery.
Get a Free Quote
Reach out to us for a free quote and expert advice on your custom hardware needs. At Prime, we’ll provide the right solution for your project, ensuring quality and precision every step of the way.