Common Casting Materials and Their Applications
Gray Iron
Excellent vibration damping and compressive strength. Used in engine blocks, machine bases, and motor housings.
Ductile Iron
Stronger and more impact-resistant than gray iron. Common in automotive suspension parts, gears, and industrial valves.
Carbon Steel
Offers high toughness and fatigue strength. Preferred for structural components, agricultural machinery, and construction hardware.
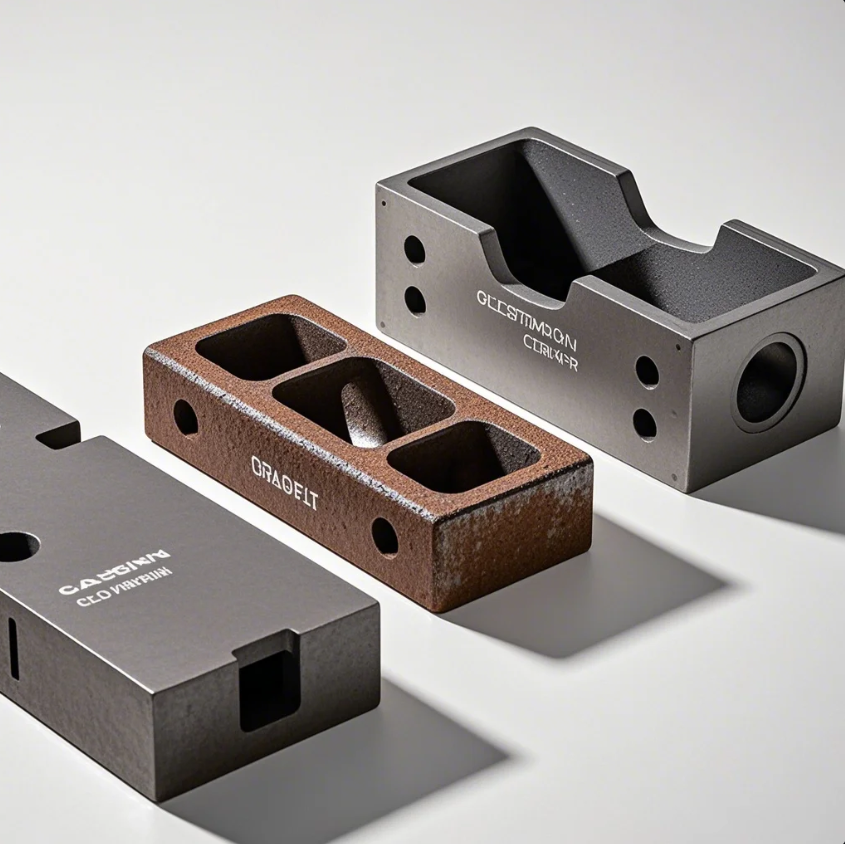
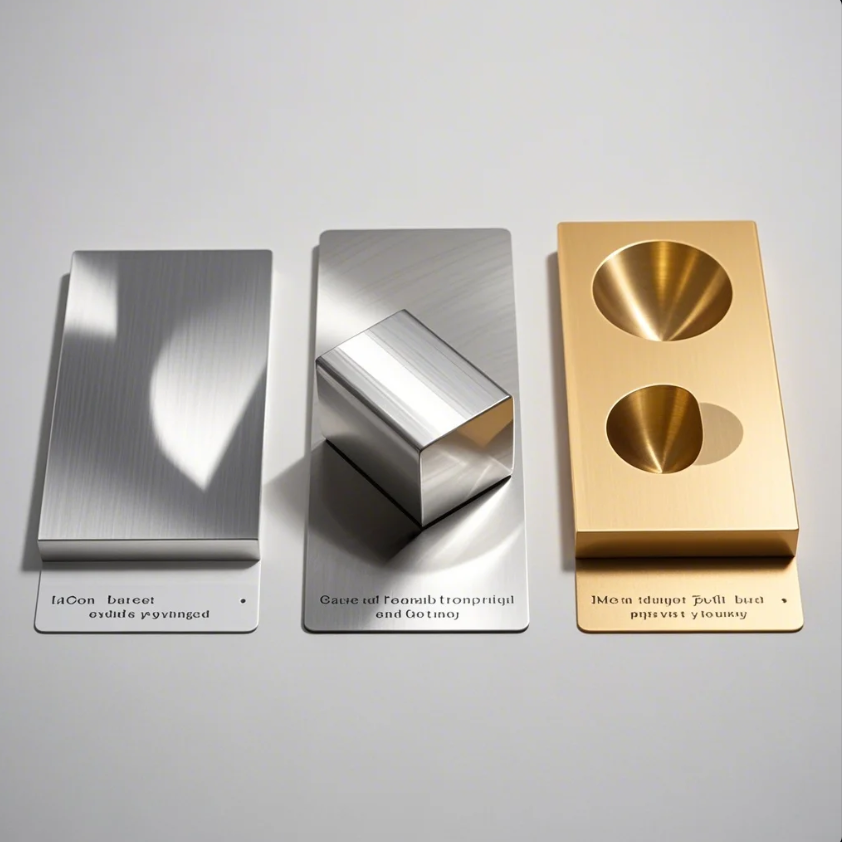
Stainless Stee
Resistant to corrosion, heat, and chemicals. Widely used in pumps, impellers, marine parts, and medical components.
Aluminum Alloys
Lightweight and corrosion-resistant. Ideal for automotive housings, aerospace brackets, and heat sinks.
Brass and Bronze
Used in plumbing, marine applications, and electrical systems due to excellent machinability and corrosion resistance.
Industrial Applications of Casting Parts
Casting parts are indispensable in nearly every industrial sector. Their ability to combine strength, complexity, and mass production makes them a top choice for engineers and procurement professionals.
- Automotive: Cylinder heads, transmission cases, brake drums, intake manifolds
- Aerospace: Turbine blades, brackets, structural mounts
- Oil & Gas: Pump housings, impellers, flanges
- Construction: Pipe fittings, counterweights, anchor plates
- Heavy Machinery: Gearboxes, base plates, axle carriers
- Electronics: Aluminum housings, connectors, heat sinks
- Marine Equipment:Propellers, valve bodies, pump casings
Each application places unique demands on performance — from heat resistance to load-bearing capacity — which casting processes can meet efficiently.
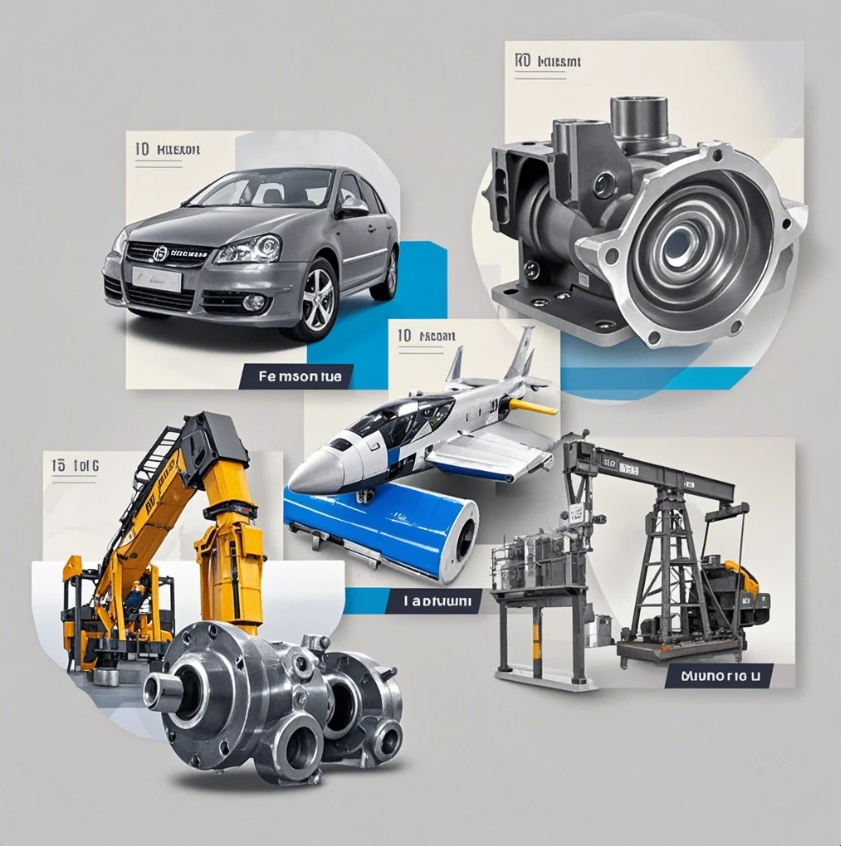
Advantages of Metal Casting
Casting allows the formation of parts with undercuts, internal passages, and intricate curves without expensive machining.
Once molds are made, casting parts can be produced at low per-unit costs, especially in sand and die casting.
From iron to nickel alloys, casting supports a wide range of metals and alloys for diverse mechanical and thermal requirements.
Hollow and lattice structures can be cast to reduce weight without sacrificing performance.
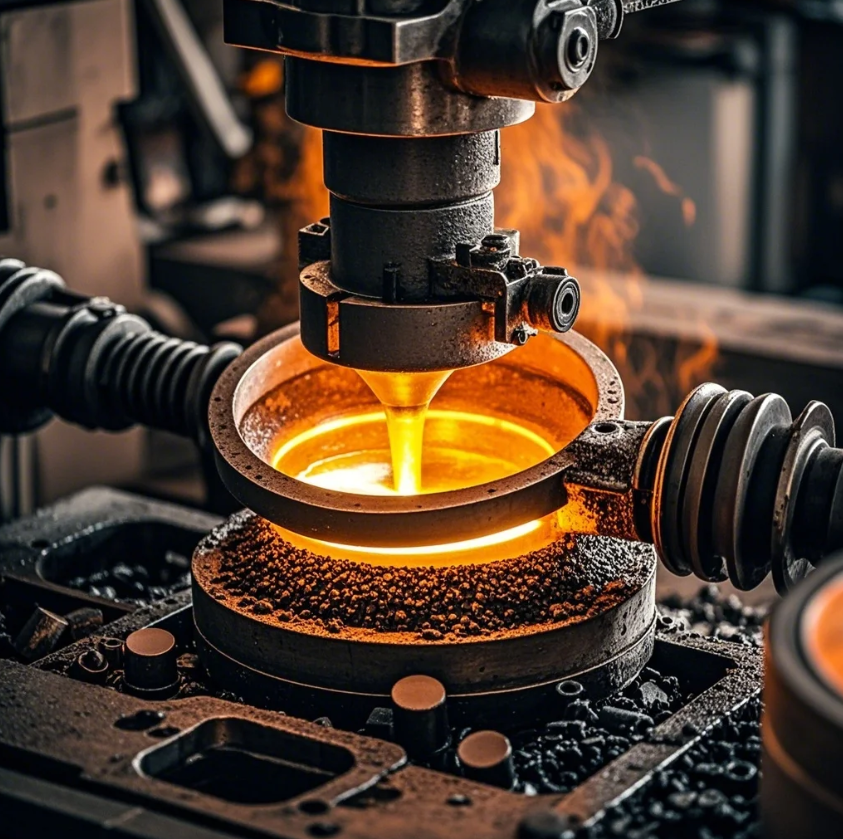
Challenges and Limitations of Casting (And How to Overcome Them)
While casting parts offer many benefits, there are also challenges:
Working with experienced foundries ensures quality and helps you avoid costly mistakes in early development.
How to Choose the Right Casting Parts Supplier
Does the supplier offer casting process selection support, CAD/CAM design, and simulation?
Can the factory handle your volume — whether prototyping or high-volume production?
Look for ISO 9001 certification, in-house inspection tools (CMM, spectrometer, X-ray), and traceability?
Are the parts properly packed for international shipping? Can they deliver on time, globally?
Are you receiving competitive pricing based on accurate material and process quotes?
Whether the quality inspection of each stage is carried out strictly according to the standard ?
Case Study: Reducing Cost and Weight with Aluminum Casting
- 36% weight reduction
- Improved corrosion resistance
- 40% lower fabrication cost
- Simplified assembly process
Production scaled to 30,000 units/year with consistent dimensional tolerances and >98% yield rate.
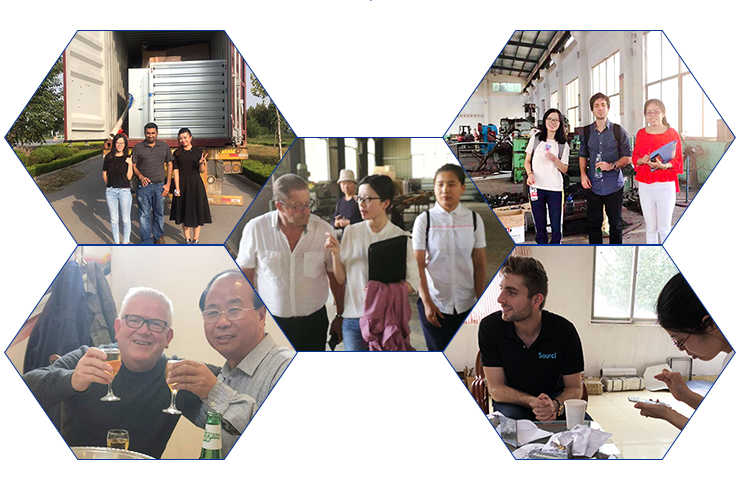
Here are the top questions from global buyers when evaluating a casting parts supplier:
By addressing these concerns, a trusted casting partner becomes a long-term strategic supplier.
- Can you meet my mechanical requirements (tensile strength, hardness)?
- What is the typical lead time for mold development and first sample?
- Do you provide machining, heat treatment, and surface finishing?
- Are certifications and test reports included with shipments?
- What is your standard packaging for international transport?
- How do you handle design changes or engineering feedback?
At Prime, we’ve specialized in producing “custom casting parts” since 1993. With 10 production lines and in-house tooling, machining, and quality inspection capabilities, we deliver end-to-end casting solutions for global industrial buyers.
- Certified by ISO 9001
- Full-service casting (sand, investment, die)
- Engineering support & DFM optimization
- 24-hour quotation response
- Rapid sampling & mass production
- Worldwide shipping & after-sales support
- Whether you're sourcing ductile iron castings, precision stainless steel parts, or custom aluminum die castings, we’re ready to help you reduce cost, improve quality, and scale efficiently.
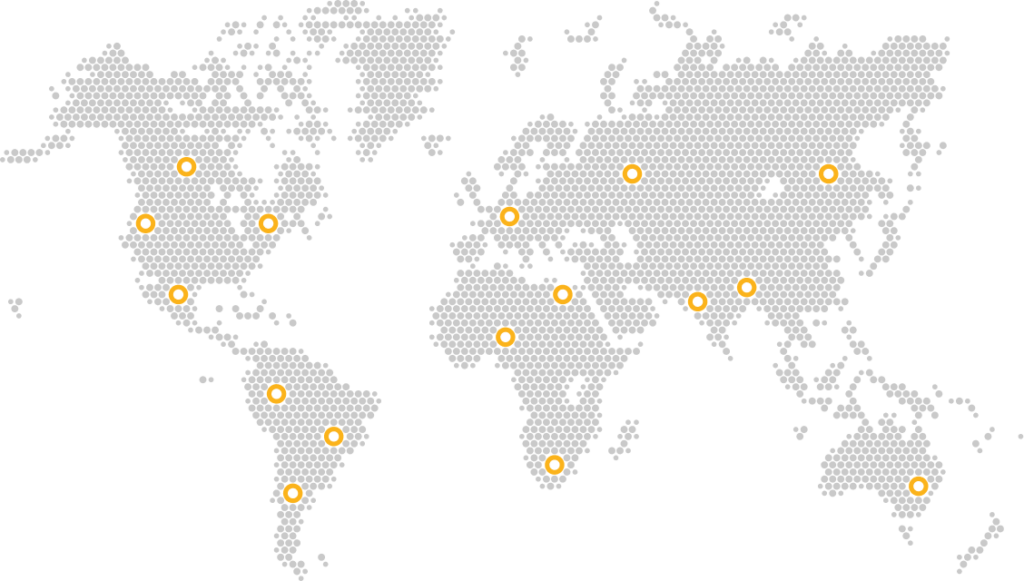
Our Happy Clients
Get a Free Quote
Start Your Project Today
Free consultation
Engineering support
Fast global delivery
Competitive pricing
Stop overpaying. Start scaling. Partner with a manufacturer that delivers results.
Apply for free quotation immediately
And get a 24h response from our expert team. Let us help you reduce costs, improve quality, and accelerate your project timeline.